Initiatives to Address Climate Change Issues
Basic Policy
Climate change is a critical business concern for the JFE Group from the perspective of business continuity. Our steel business, which emits 99.9% of the Group’s total CO2 emissions, has been developing various technologies for saving energy and reducing these emissions. We have applied these technologies to steel manufacturing processes to enable production with low levels of CO2 emission intensity.
Furthermore, we have developed and maintained a variety of eco-friendly products and technologies, including high-performance steel materials that help save energy when customers use them, as well as renewable energy power generation.
We will continue to develop and promote the widespread use of these processes and products. We consider this as an opportunity to apply the technologies we have fostered across the globe and at the same time contribute to tackling climate change.
JFE announced its endorsement for the TCFD recommendations in May 2019 and has identified climate change-related issues based on the scenario analysis advocated in the TCFD to formulate strategies for sustainable growth. In September 2020, JFE disclosed its target of reducing CO2 emissions in FY2030 in the steel business, which accounts for most of the Group’s CO2 emissions. It also announced its intention to achieve carbon neutrality by 2050, ahead of the Japanese government’s announcement of the same goal.
In February 2022, the target of reducing CO2 emissions in FY2030 was revised upward to 30% or more, compared to FY2013, considering advances in measures for carbon neutrality and improvement of external surroundings in the steel sector.
To achieve these targets, the JFE Group will work hard to reduce CO2 emissions and energy consumption.
JFE Group Environmental Vision for 2050
The JFE Group intends to strengthen sustainability through solutions that address global climate change issues while restructuring its business in response to changes in the environment surrounding the steel business. We regard 2020 as a milestone year for further reinforcing our efforts to tackle climate change, and we are actively promoting initiatives for reducing CO2 emissions.
In 2021, we positioned climate change as a top-priority issue in the Seventh Medium-term Business Plan and formulated the JFE Group Environmental Vision for 2050 toward achieving carbon neutrality by that year.
We will systematically address climate change by reflecting the TCFD’s principles in the business strategies of our JFE Group Environmental Vision for 2050. In the steel business, we will reduce CO2 emissions by 18% from FY2013 levels by the end of FY2024. In addition, we announced that the target of reducing CO2 emissions in FY2030 is 30% or more, compared to FY2013, in the steel business. To explore all possibilities for realizing carbon neutrality in 2050, we will take on the challenge of developing ultra-innovative technologies such as carbon-recycling blast furnaces developed with our proprietary technology while also adopting a multitrack approach for pursuing other technologies. In our engineering business, we will widen our contribution to the reduction of CO2 in society as a whole by expanding and advancing renewable power generation and carbon-recycling technologies, supplying high-performance steel products, and other initiatives. Furthermore, we will apply Group strengths to accelerate the commercialization of our offshore wind-power business.
JFE Group Environmental Vision for 2050
- Climate change is a critical business concern for JFE, and we are aiming to achieve carbon neutrality by 2050.
- We will accelerate our research and development of new technologies and pursue ultra-innovative technologies.
- We will seek business opportunities that allow us to enhance corporate value by contributing to CO2 emissions reduction across society.
- The principles of TCFD will be reflected in our business strategies and systematically deployed.
The Target of Reducing CO2 Emissions in FY2024 (Seventh Medium-term Business Plan Initiatives)
- Reduce steel-business CO2 emissions in FY2024 by 18%, compared to FY2013 (steel business)
The Target of Reducing CO2 Emissions in FY2030
- Reduce steel-business CO2 emissions in FY2030 by 30% or more, compared to FY2013 (steel business)
Initiatives for Carbon Neutrality by 2050
-
Reduce steel-business CO2 emissions
- Pursue ultra-innovative technology for carbon-recycling blast furnaces and CCU.
- Develop hydrogen-based ironmaking (direct reduction) technology.
- Leverage top-in-class electric arc furnace technology for high-quality, high-performance steel manufacturing, high efficiency, etc.
- Develop transitional technologies for carbon neutrality, including ferro coke, increased use of steel scrap in converters, energy savings, and low-carbon energy transformations.
-
Expand contributions to CO2 emissions reduction in society
- JFE Engineering: Expand and develop renewable energy power generation and carbon-recycling technologies.
(Reduce CO2 emissions by 12 million tonnes in FY2024 and 25 million tonnes in FY2030) - JFE Steel: Develop and market eco-products and eco-solutions.
- JFE Shoji: Increase trading in biomass fuels, steel scrap, etc., and strengthen business in supply chain management (SCM) for eco-products.
- JFE Engineering: Expand and develop renewable energy power generation and carbon-recycling technologies.
-
Offshore wind-power generation business (Group-wide effort to accelerate commercialization of the offshore wind-power business)
- JFE Engineering: Manufacture monopiles and other seabed-fixed structures for offshore wind-power generation.
- JFE Steel: Produce large and heavy plates by using new continuous casting machine in Kurashiki.
- JFE Shoji: Carry out SCM for steel materials and processed products.
- Japan Marine United Corporation: Manufacture offshore wind-power generation floating structures and construct work vessels.
- Group-wide: Operation and maintenance (O&M) making maximum use of Group resources.
Notes.
- 1Carbon-recycling blast furnace: A technology that converts CO2 from the blast furnace into methane, which is then used as reducing material in the blast furnace
- 2CCU: Carbon dioxide capture and utilization
- 3Transitional technologies: Technologies that advance the transition to carbon neutrality
- 4Ferro coke: Innovative blast furnace raw material that improves the reduction efficiency of iron ore and reduces CO2 generation from the blast furnace
Developing processes to mass produce high-quality, high-performance steel with zero CO2 emissions is essential for a sustainable world. Huge R&D and equipment replacement costs will be inevitable as JFE executes strategies targeting carbon neutrality. Society must decide how these costs should be shouldered, including government support.
Working toward the lofty goal of carbon neutrality by 2050, JFE is focusing on establishing the necessary decarbonization technologies as quickly as possible, ahead of global competitors, assuming that we have the decarbonization infrastructure in place and ability to compete on an equal footing globally.
JFE Group’s Activities for Carbon Neutrality
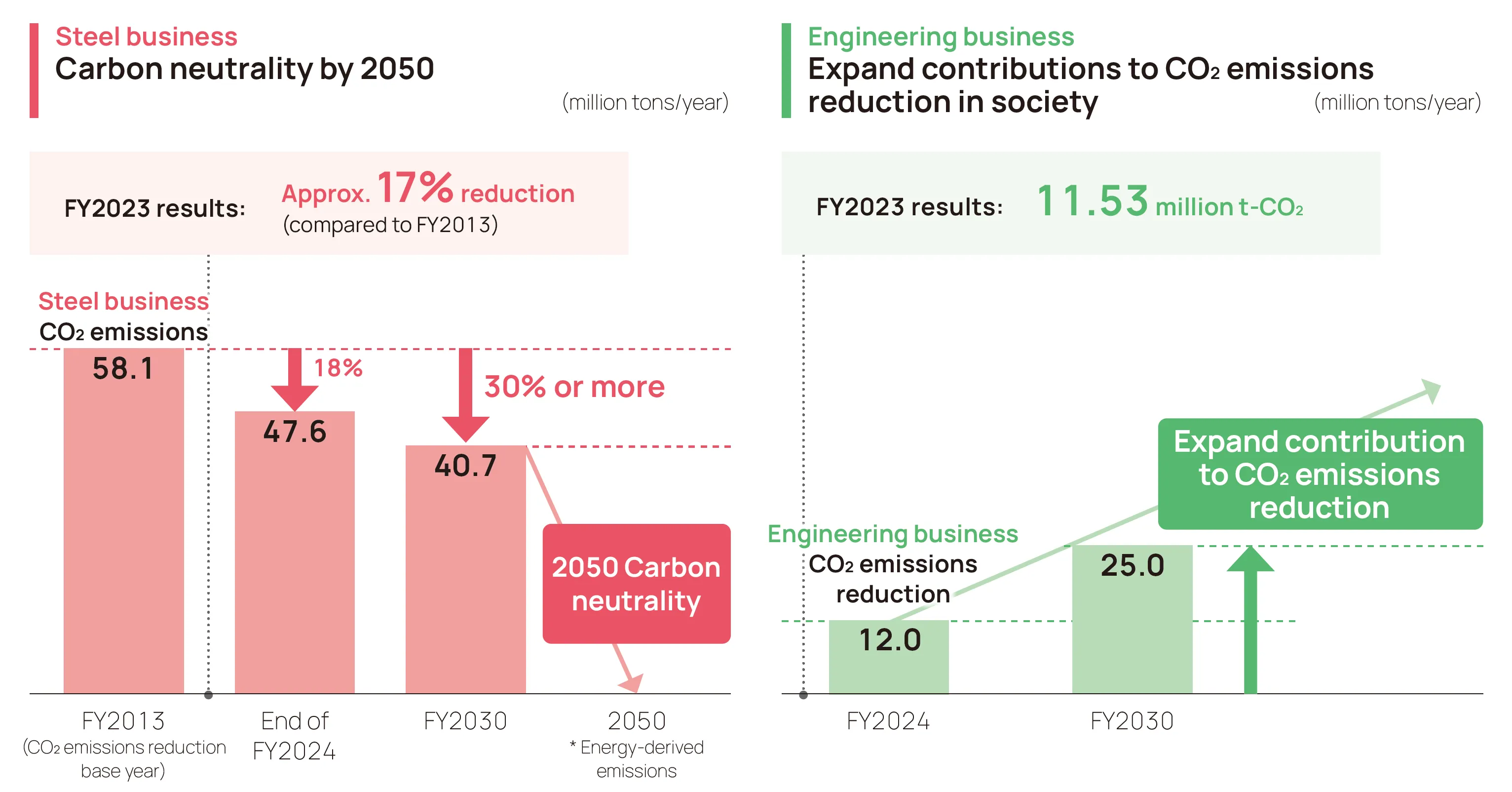
Information Disclosure Based on TCFD Recommendations

On May 27, 2019, JFE Holdings announced its endorsement for the final report of the Task Force on Climate-related Financial Disclosures (TCFD)*.
- * The TCFD was established by the Financial Stability Board (FSB) at the request of G20 finance ministers and central bank governors.
Climate-related risks and opportunities will significantly impact medium- to long-term corporate finance. To reduce the risk of instability in the financial market, the G20 called on the FSB to establish the TCFD. The TCFD considers disclosure methodologies that can be used to appropriately assess climate-related risks and opportunities and releases its findings as a final recommendations report.
It is important for investors to accurately understand the financial impact of climate-related risks and the opportunities of investee companies when they make financial decisions. In this context, the task force recommends disclosures to be made in four core elements of organizational management: governance, strategy, risk management, and metrics and targets.
For the TCFD content index, click on the following link.
Governance (Management Structure: JFE Group)
Under the JFE Group Standards of Business Conduct, the JFE Group actively strives to exist in harmony with the global environment and create a society that is comfortable and convenient. We are aware that efforts to protect the global environment, such as reinforcing our environmental protection activities and addressing climate change issues, are extremely important for creating a sustainable society.
In FY2016, we identified the mitigation of global warming as a material CSR issue to facilitate the PDCA cycle and promote appropriate management of ongoing initiatives, such as reducing CO2 in the iron and steelmaking processes and developing and providing eco-friendly products. In 2021, we relaunched the initiative as a top priority by adding economic perspectives to the material issues and by selecting other vital matters of importance. As part of this effort, we set our goal for helping to address climate change (initiatives to achieve carbon neutrality by 2050) as an area of focus and identified reducing the JFE Group’s CO2 emissions and contribution to CO2 emissions reduction in society as two material issues.
The JFE Group Environmental Committee, chaired by the president of JFE Holdings and operating under the JFE Group Sustainability Council, sets goals for environmental protection, monitors the progress of these initiatives and works to improve the Group’s overall environmental performance.
Key managerial issues such as climate change and other environmental challenges are deliberated on by the Group Management Strategy Committee and reported to the Board of Directors. The board also deliberates on these issues and supervises the initiatives.
Examples of Climate Change-Related Agenda Items Involving Board of Directors Decisions and Reports
- Declaration of endorsement for the final TCFD recommendation report
- Information disclosure consistent with TCFD recommendations (scenario analysis and other information)
- Formulation of the Seventh Medium-term Business Plan, JFE Group Environmental Vision for 2050
- Review the CO2 emissions reduction target for FY2030
- Use of climate-related metrics to determine executive remuneration
JFE Group’s Climate Change Strategy
Various risks and opportunities related to climate change are integrated into the JFE Group’s business strategy. The Group formulated the Seventh Medium-term Business Plan as the main guide for business operations from FY2021 to FY2024, and we positioned efforts to address climate change as the key to achieving sustainable growth and increased value over the medium to long term. Under the plan, the Group defined ensuring environmental and social stability as a core strategy and formulated the JFE Group Environmental Vision for 2050 for achieving carbon neutrality by 2050. Then we concentrated our efforts on our business strategy and reflected the principles of the TCFD recommendations in our management strategy, enabling us to systematically address climate change. Furthermore, we are disclosing information based on the TCFD recommendations, including the scenario analysis, leveraging them to identify and evaluate risks and opportunities, and reflecting them in our management strategy.
For further details on the Results of Scenario Analysis and the JFE Group Environmental Vision for 2050, refer to the following source material.
- Scenario Analysis in Line with the TCFD Recommendations
- JFE Group Environmental Vision for 2050, Presentation Material
In the JFE Group Environmental Vision for 2050, our efforts to achieve carbon neutrality are based on the following three key strategies: reduce CO2 emissions at JFE Steel, expand contributions to the reduction for society as a whole, and accelerate Group-wide commercialization of the offshore wind-power business. In the steelmaking process, along with efforts to reduce CO2 emissions, we will also actively work on reducing environmental impact through reusing water resources and energy, developing environmentally sound products and process technologies, and providing resource recycling solutions.
JFE Steel’s Management Structure to Promote Carbon Neutrality
Governance (Management Structure: JFE Steel)
The key for ensuring JFE Steel’s sustainable growth is to develop and implement a medium- to long-term strategy for realizing Green Transformation (GX). In addition to developing and investing in technologies related to carbon neutrality, other necessary tasks are required for increasing the sales of green steel products, such as forming new markets and strengthening cooperation with government authorities. In April 2024, the Green Transformation Strategy Headquarters was established to formulate and promote a Company-wide strategy to realize Green Transformation. The office is comprised of the recently established Green Transformation Planning Department and departments responsible for developing technologies, specifically the Carbon Recycling Development Department, Advanced Reduction Process Development Department, Advanced Melting Process Development Department, and Green Energy Infrastructures Development Department. The Green TransformationPlanning Department is responsible for developing medium- and long-term strategies for realizing Green Transformation and the market formation and sales of green steel products. It also oversees related technologies, internal and external collaboration, and the planning and implementation of other measures.
JFE Steel’s Management Structure to Promote Carbon Neutrality
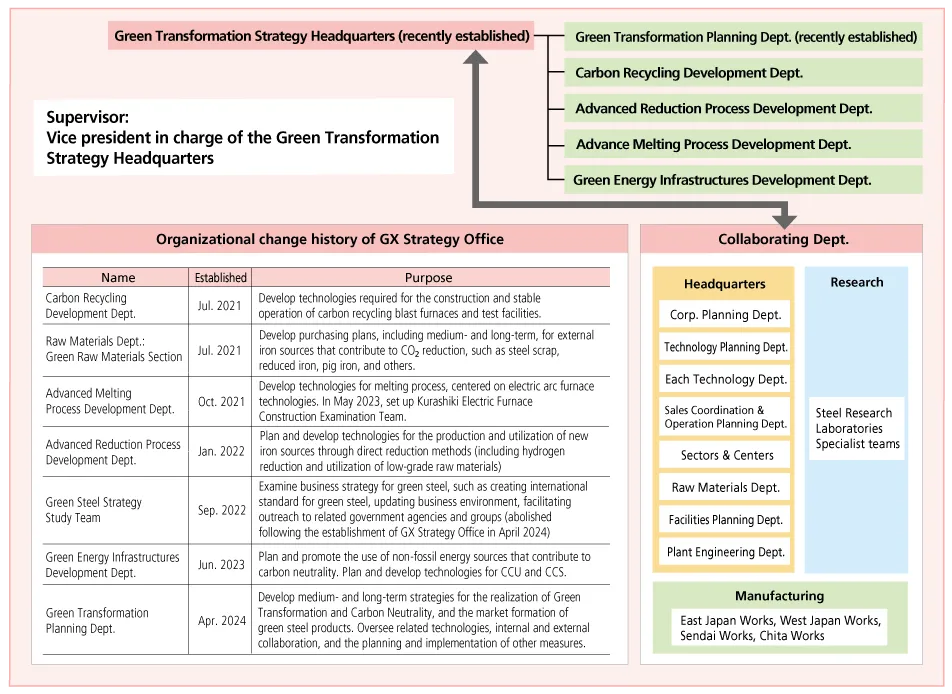
JFE Steel’s Strategy to Reduce CO2 Emissions
The JFE Group has adopted a multipronged approach, including the development of ultra-innovative technologies, to achieve carbon neutrality by 2050. In the steel business, we have set a target for reducing CO2 emissions by 18% as of the end of FY2024 and by 30% or more by FY2030, compared to FY2013. We have defined the period up to 2030 as a transition phase and the period after that as an innovation phase. In the transition phase, we will focus more on initiatives to reduce emissions through an expanded application of low-carbon technologies to steadily advance toward achieving the CO2 reduction target in FY2030. In this phase, we will also accelerate the development of ultra-innovative technologies to prepare for the innovation phase. In the innovation phase, we will advance initiatives for the wise use of resources, including the commercialization of carbon-recycling blast furnaces that leverage our proprietary carbon-recycling technology and direct reduction steelmaking, as well as the expansion of CCU applications. Furthermore, we will undertake CO2 sequestration through CCS to create a carbon-neutral society together with local communities and industrial complexes. We will achieve carbon neutrality through initiatives under these three themes.
Transition to Low-Carbon Steel Processes
Our multi-pronged approach includes developing ultra-innovative technologies for achieving carbon neutrality by 2050. We have defined the period up to 2030 as a transition phase and the period after that as an innovation phase. In the transition phase, the steel business is promoting energy-saving and high-efficiency improvements in existing processes and the use of electric furnace technology. We anticipate that achieving the CO2 reduction target for FY2030 may require investments and loans of around one trillion yen, and approximately 300 billion yen has been approved by FY2023. We intend to steadily advance toward obtaining the necessary investments and loans to achieve the reduction target.
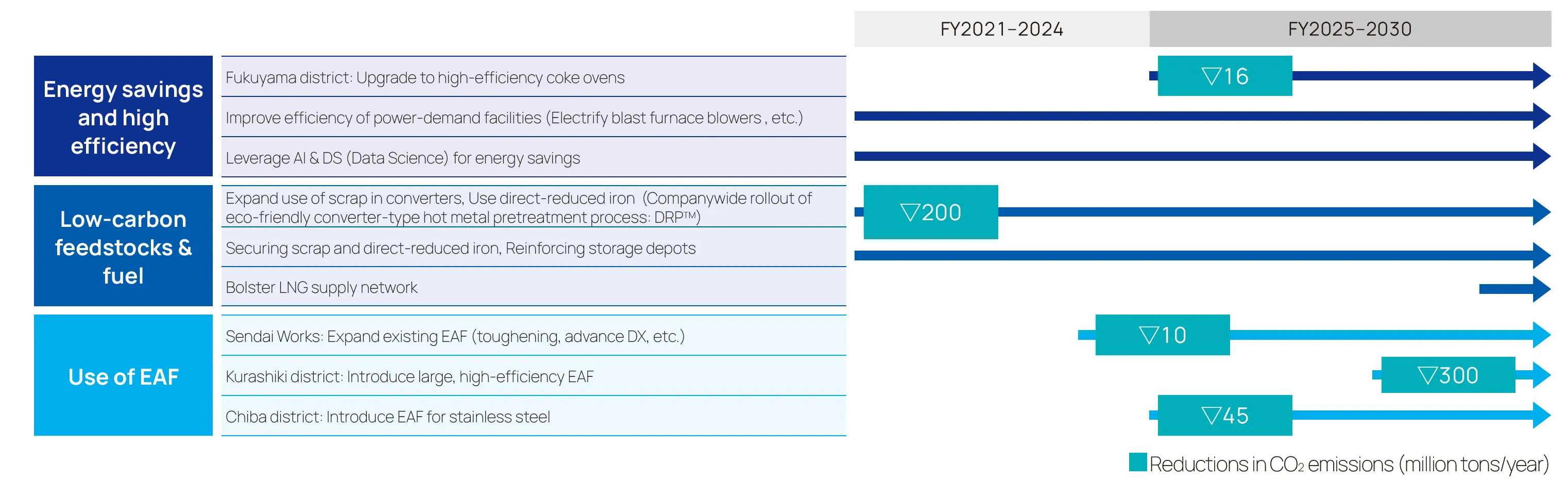
Development of Electric Arc Furnace Process Technology
An electric arc furnace process is one of the JFE Group’s development efforts in steelmaking technologies for carbon neutrality. With this technology, steel products are manufactured by melting steel scrap and direct-reduced iron in an electric arc furnace. So far, we have managed to reduce CO2 emissions from this steelmaking process down to one-quarter of that of the blast furnace-converter method. We are striving to eliminate CO2 emissions generated by the electric arc furnace process in the future by using the aforementioned hydrogen-reduced iron as the raw material and non-fossil electricity.
Although the electric arc furnace process has the advantage of reducing CO2 emissions, there are two major problems compared to the blast furnace-converter method: the productivity of the electric arc furnace process in general is about 30% lower than that of the blast furnace-converter method, and the use of scrap as the raw material inevitably increases the concentration of impurities, which limits the production of high-quality, high-performance steel products. We are working to address these issues, for utilizing Transition Finance, to establish technologies that will enable the production of high-quality, high-performance steel with high productivity using the electric arc furnace process. The innovative electric furnace is the super-advanced technology that can be most quickly implemented. We view it as a replacement for one of the blast furnaces in Kurashiki District, which is due for refurbishment in FY2027. We are planning to make the investment decision within FY2024, subject to government support, and begin operation in FY2027.
Use Electric Arc Furnaces to Increase the Use of Scrap
JFE Steel is planning to increase the production capacity of the electric arc furnaces in the Sendai Works by approximately 0.14 million tonnes per year by FY2024 through reinforcing the electric arc furnaces in the Sendai Works, implementing capacity-boosting DX measures, and improving the load handling equipment. This is expected to result in a reduction of approximately 0.10 million tons of CO2 emissions per year.
We are planning to install a new electric arc furnace in the Chiba district for stainless steel production. This will allow the facility to replace part of the feedstock from molten iron from blast furnaces with scrap and thus reduce CO2 emissions. This could increase by up to six times the volume of scrap used, and we expect to reduce CO2 emissions by a maximum of about 450,000 tons per year.
Furthermore, in the Kurashiki district, we are considering switching to a newer process technology by replacing one of the blast furnaces, which needs to undergo preventive maintenance within the period of 2027–2030, with a large, high-efficiency electric arc furnace.
Feasibility Study on New Venture Business to Secure Reduced Iron Supply
In the transition phase up to 2030, we expect a shortage in domestic scrap supply. The use of direct-reduced iron is considered an effective way to supplement this in the production of high-quality steel using electric arc furnaces and in the reduction of CO2 emissions from blast furnaces.
JFE Steel has agreed with EMSTEEL, the largest steel producer in the UAE, and ITOCHU Corporation (ITOCHU) to jointly conduct detailed feasibility studies on the establishment of a supply chain of reduced iron with low carbon emissions. Under a joint venture to be established in the UAE, we are focusing on producing direct-reduced iron with low carbon emissions from the second half of FY2025 using CCUS (EOR*), which takes full advantage of the geographic location of the UAE.
- * Enhanced oil recovery
Collaboration to Establish a Supply Chain of Ferrous Raw Material for Green Ironmaking with Low Carbon Emissions
JFE Steel regards the use of green ferrous raw material as a key initiative for reducing CO2 emissions. We are participating as a core member in the establishment of a reduced iron supply chain with low carbon emissions along with ITOCHU and EMSTEEL, and we are jointly pursuing a detailed feasibility study with Abu Dhabi as a candidate project site.
At the Japan-UAE Business Forum that was held on July 17, in the presence of Japanese Prime Minister Fumio Kishida, JFE Steel has signed and exchanged a memorandum of understanding (MOU) with ITOCHU, EMSTEEL, and the Abu Dhabi Ports Group (ADPG) to develop collaborative systems for the establishment of a supply chain to handle ferrous raw material for green ironmaking with low carbon emissions.
ADPG, the state-owned port operator and economic and industrial zones developer in Abu Dhabi in which the project is planned to be developed, owns 10 ports and 550km2 of economic and industrial areas. The parties have agreed that ADPG will participate fully in project-related port development and operations, land leasing and services, and infrastructure development. Collaboration with ADPG will provide the undertaking with access to a suitable site for building a distribution and logistics system capable of stably importing raw materials and shipping products for the envisioned supply chain.
●Overview of EMSTEEL
Company name: EMSTEEL
Representative: HE Engineer Saeed Ghumran Al Remeithi (Group CEO)
Business: Steel
●Overview of ADPG
Company name: Abu Dhabi Ports Group
Representative: Captain Mohamed Juma Al Shamisi
Business: Port operations, shipping, logistics and special economic zone development
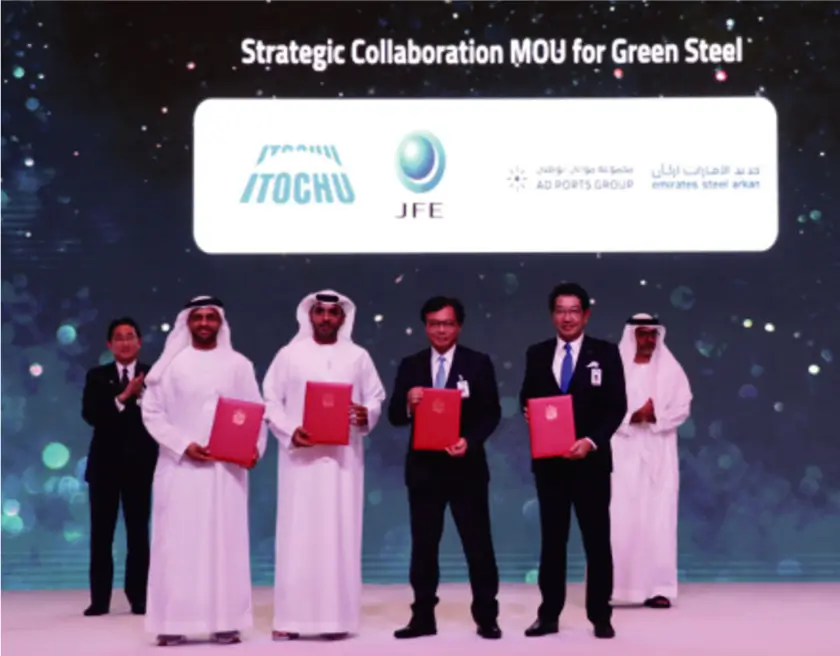
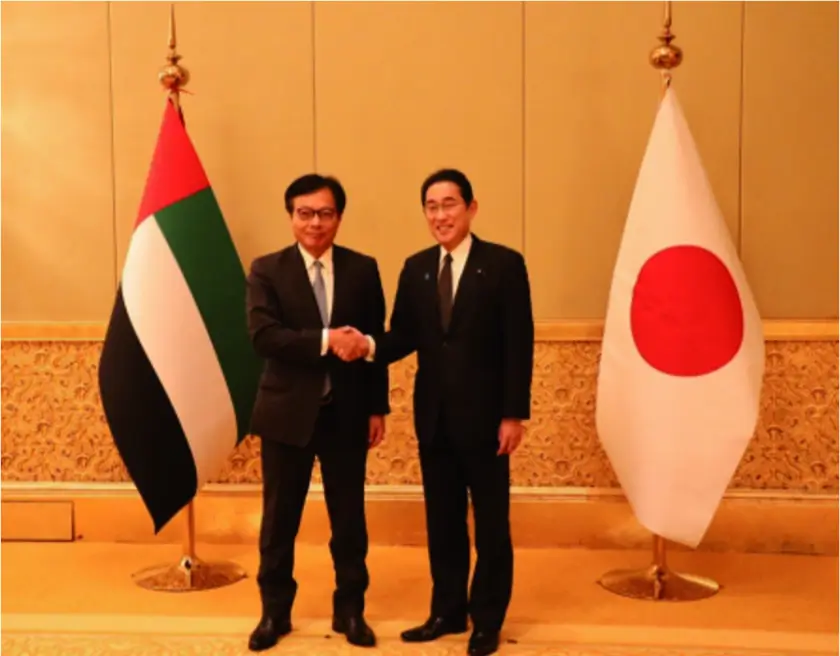
Improve productivity of the electric arc furnace process
To improve productivity of the electric arc furnace process, the JFE Group have developed ECOARC™, our proprietary, eco- friendly, high-efficiency electric arc furnace, and installed it at our operating companies. With this technology, a shaft is attached to the upper part of the electric arc furnace and is used to continuously feed scrap materials into the furnace. It uses the high-temperature exhaust gas from the furnace to preheat the scrap material, allowing for subsequent high-efficiency and high-speed melting. As well as improving the productivity of the electric arc furnaces, the technology also reduces the energy (electricity) required for the melting process.
The Group already has achieved industry-leading productivity and energy (electricity) efficiency with these technologies, but we are working to raise productivity even further.
Overview of the Demonstration Tests
We are developing a process that reduces the electric arc furnace’s melting power consumption and also enables high-speed melting of cold iron sources (scrap and reduced iron). We will verify the following during demonstration tests.
- Optimal methods for preheating and feeding reduced iron
- Methods for using heating burners
- Optimal methods for molten steel stirring
Research and Development for Electric Arc Furnaces
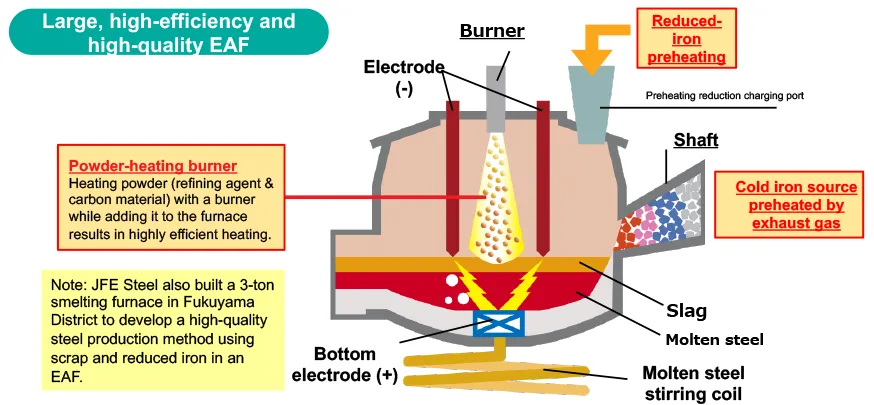
Manufacturing Higher-Grade Steels Using the Electric Arc Furnace Process
The electric arc furnace process uses scrap and reduced iron as raw materials. The higher concentration of impurities in these materials, such as copper, causes material degradation, including surface defects and reduced workability in steel sheets and deterioration of properties in electrical steel sheets. We are working on two technologies to address the issue, one to remove impurities and another to detoxify impurities, so that we can use the electric arc furnace process to produce high-quality steel products such as steel sheets for automobiles and electrical steel sheets.
East Japan Works (Chiba District) to Produce Stainless Steel with Electric-Arc Furnace
JFE Steel has decided to install a new electric-arc furnace at the No. 4 steelmaking shop at the East Japan Works (Chiba district) in the second half of FY2025 (planned). Scrap melting capacity is expected to increase by up to six times compared to the conventional process, to approximately 300,000 tonnes per year (planned), and CO2 emissions are expected to be reduced by up to about 450,000 tonnes per year. We have defined the period up to 2030 as a transition phase toward carbon neutrality and consider the electric furnace process to be an effective means of reducing CO2 emissions. Looking ahead, we will continue to develop ultra-innovative technologies in a multi-pronged approach and make steady progress toward realizing carbon neutrality.
Increased Use of Scrap Iron in Steelmaking
JFE Steel completed introducing the Double-slag Refining Process (DRP™), an eco-friendly converter-type molten-iron pretreatment process, in all of its sites in 2021. This increased the amount of scrap iron to be used in converters, leading to reduced CO2 emissions.
DRP makes full use of silicon in molten iron as a heat source, thereby increasing the amount of scrap iron to be used in converters. It allows reducing the molten-iron blending ratio (molten iron vs. scrap charged into the converter) to 82%, down from 90% through conventional methods.
The Company introduced this process in all of its steelmaking facilities, and the increased use of scrap iron in converters enabled us to reduce CO2 emissions by approximately 0.60 million tons per year in FY2022. In the future, we will develop technologies to increase heating margins to further boost the use of scrap and invest in facility expansion to reduce CO2 emissions by about 2 million tons per year by FY2030.
Eco-friendly converter-type molten iron pretreatment process
DRP™: Double-slag Refining Process
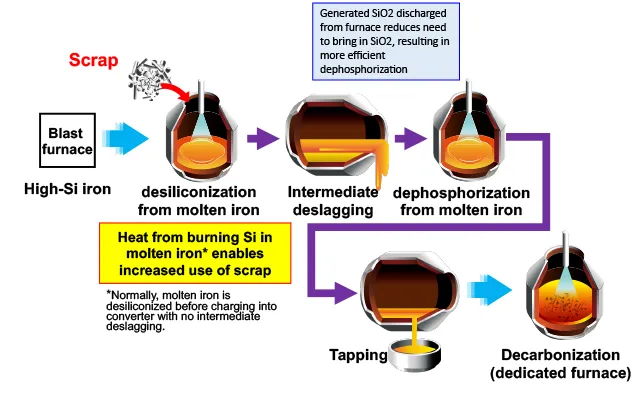
Started supplying JGreeX™: green steel products
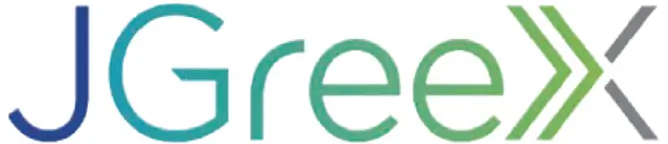
Name origin: JFE + Green + GX
We invited the relevant departments to propose names and selected this name from the suggestions because it clearly expresses being a green steel product provided by JFE Steel.
Logo design:
The logo combines the letter X with an arrow to express our intention to move forward toward carbon neutrality.
In the first half of FY2023, JFE Steel began supplying JGreeX™, a brand of green steel products that significantly reduce CO2 emissions in the steel manufacturing process compared to conventional products. With the current technology, it is difficult to immediately supply green steel products with significantly lower or zero emissions, so the reductions created by our technologies are allocated to any steel products by applying the mass balance method*1 and then supplied as green steel products. With regard to the amount of CO2 emission reductions and the emission intensity of each product, we have obtained a third-party certification from Nippon Kaiji Kyokai (ClassNK), which verified 600,000 tonnes of CO2 emission reduction in FY2022.
In October 2023, JGreeX™ was selected by Sumitomo Corporation for its new office building, tentatively named Suidobashi PREX (Photo 1) . This was the first application of green steel materials in both the real estate and construction industries. In October of the same year, it was selected for transformers that will be manufactured in Europe. Grain-oriented electrical steel was selected. This was the first order for JGreeX™ outside of Japan and its first use in electrical steel sheets.
Its application in shipbuilding is expanding. In December 2023, shipping company Kawasaki Kisen Kaisha, Ltd. selected JGreeX™ for an Ultramax dry bulk carrier*2 to be built by Imabari Shipbuilding Co., Ltd. (Photo 2). All steel materials*3 used in the construction of this vessel will be JGreeX™ products, making it one of the world’s largest ships made entirely of green steel. JFE Steel expects to supply 7,000 tons of JGreeX™ products starting in 2024, and the vessel is slated for commissioning in 2026. Separately, shipping company Daiichi Chuo Kisen Kaisha selected JGreeX™ for two coastal dry bulkers to be built by Higaki Shipbuilding Co., Ltd., and based on this development, JFE Steel expects to supply 7,000 tons of JGreeX™ products between 2024 and 2026. All told, JGreeX™ has now been selected by five companies for a total of nine dry bulk vessels, bringing JFE Steel’s total expected supply of JGreeX™ products to approximately 36,000 tons. In June 2024, the first bulk carrier built entirely with JGreeX™ was launched (Photo 3). A naming and launch ceremony was held at the headquarters of Higaki Shipbuilding Co., Ltd., with the ship receiving the name BRIGHT QUEEN. It is the world’s first ship built entirely with green steel. This is the first of two bulk carriers that Higaki Shipbuilding is constructing for shipping company NYK Bulk & Projects Carriers Ltd. (NBP) and for which JGreeX™ was selected back in June 2023. The vessel is also expected to be the first to receive the a-EA (GRS)*5 designation, indicating a hull structure made of green steel materials, in accordance with new environmental guidelines*4 developed by ClassNK, a Japanese non-profit NGO engaged in ship classification and environmental protection.
In January 2024, JGreeX™ was selected for pinback buttons (can badges) produced and sold by MoNo Factory, marking the first use of JGreeX™ in consumer products as well as tin-plated steel. In February 2024, JFE Steel started selling JGreeX™ green steel to Hock Seng Hoe, a leading steel wholesaler in Singapore that wholesales steel plates for shipbuilding, construction and offshore structures in Southeast Asia. This marks the first sale of JGreeX™ to a Southeast Asian company. In June 2024, JGreeX™ was selected by the world leading manufacturer of IT data center transformers in the United States, marking the first application of JGreeX™ in that country. In July 2024, it was selected for use in resource-recycling containers (Photo 5: LOOPOX) and logistics warehouses (Photo 6: tentatively named Shin-Harumi Warehouse) , with additional applications expected.
Reduction of CO2 throughout the supply chain is rapidly progressing. JFE Steel will contribute to the decarbonization of society by expanding its capacity for supplying JGreeX™ and further reducing CO2 emissions through the use of advanced low-carbon technologies as well as energy-saving, high-efficiency technologies.
- *1 Consolidate the environmental value of CO2 emission reduction from the entire product manufacturing process, allocate the value to some steel products, and regard them as having low CO2 emission intensity
- *2 Cargo ships that transport large quantities of dry cargo
- *3 Steel products purchased directly by shipbuilding companies
- *4 Environmental guidelines developed by ClassNK, a Japanese non-profit NGO
- *5 Advanced Environmental Awareness (GRS). The vessel is expected to receive this designation when it enters service in September 2024.
Photo 1
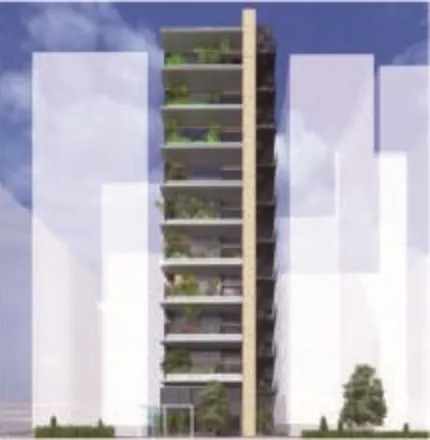
Photo 2
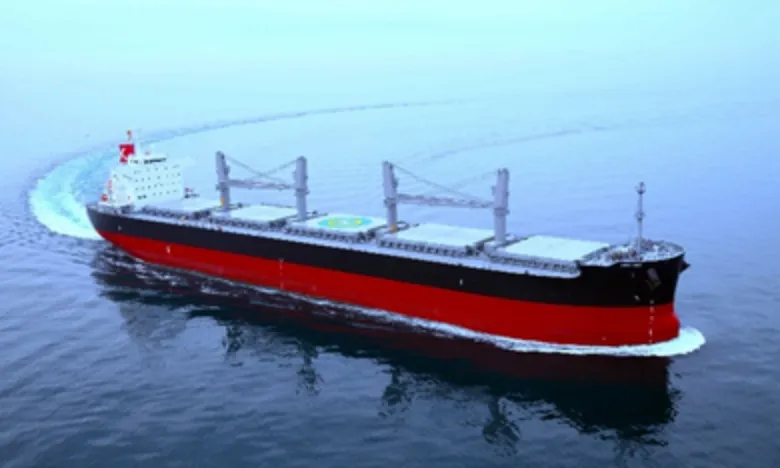
Photo 3
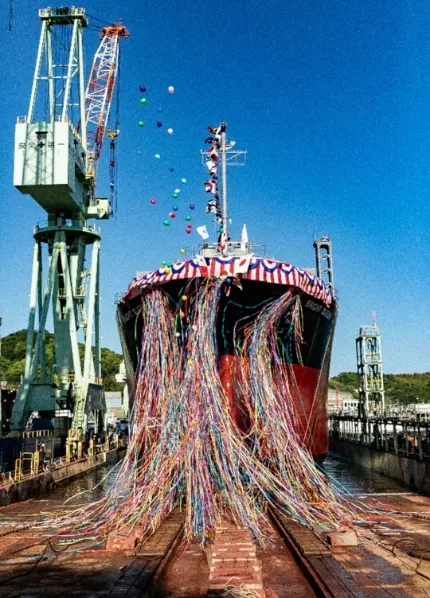
Photo 4
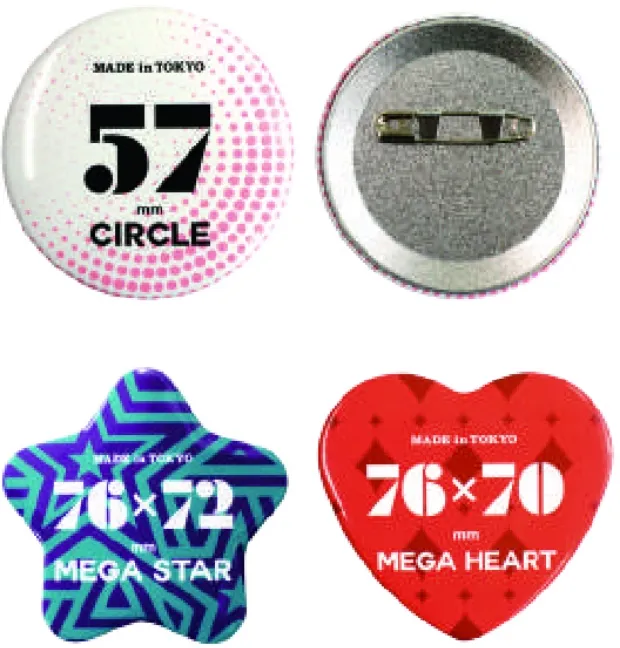
Photo 5
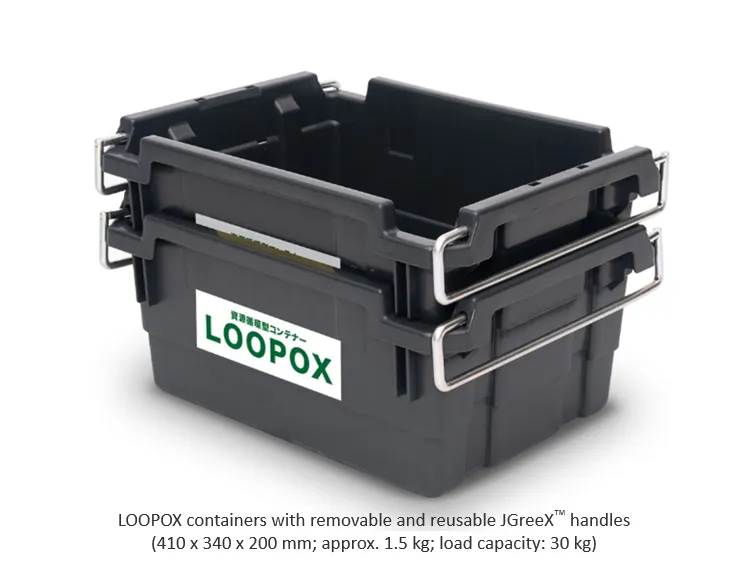
Photo 6
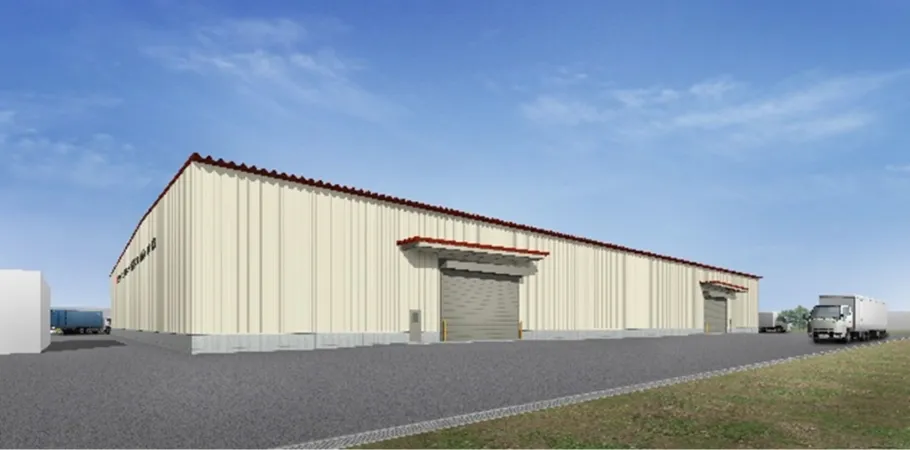
JGreeX™ Adoption Status in Dry Bulk Carriers
Shipping Company | Status | Related News Release | |
---|---|---|---|
1 | NYK Bulk & Projects Carriers, Ltd. | Launched in June 2024 | June 20, 2023 Large Cargo Ships to be Made Exclusively with JFE Steel’s JGreeX™ Green Steel |
2 | NYK Bulk & Projects Carriers, Ltd. | - | |
3 | MOL Drybulk Ltd. | - | |
4 | Toko Kaiun Kaisha, Ltd. | - | |
5 | Kawasaki Kisen Kaisha, Ltd. | - | December 20, 2023 JFE Steel’s JGreeX™ Green Steel Selected for Large Dry Bulk Carrier—Working with Shippers to Promote the Value of CO2 Reduction |
6 | Daiichi Chuo Kisen Kaisha | - | |
7 | Daiichi Chuo Kisen Kaisha | - | |
8 | NYK Bulk & Projects Carriers, Ltd. | - | |
9 | NYK Bulk & Projects Carriers, Ltd. | - |
Overview of green steel JGreeX™
Supply start | First half of FY2023 |
---|---|
Supply capacity | |
Target products | |
認Certification body | Nippon Kaiji Kyokai (ClassNK) |
Overview of the steel mass balance approach
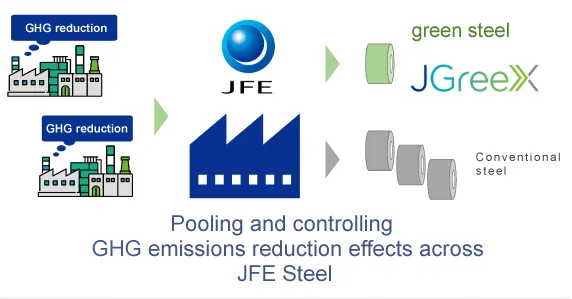
STEP 1
Calculate the emissions intensity of any steel product to apply this approach
STEP 2
Identify emissions reduction projects and determine their emissions reduction levels
STEP 3
Issue a reduction certificate based on the determined reduction level, grant the certificate, and supply steel materials.
- * This certificate and the GHG emission reductions listed in this certificate do not represent carbon credits and cannot be transferred or sold to third parties.
- * The scope of GHG emissions calculation is within the scope of Scope 1, Scope 2 and Scope 3.
- * Reduction allocations are within the scope of Scope 1 and Scope 2.
Innovations toward Carbon Neutrality
We will work on developing carbon-recycling blast furnaces (CR blast furnaces), hydrogen steelmaking (direct reduction), and electric arc furnace process (high-efficiency, large-scale electric arc furnaces) in a multi-pronged approach to achieve carbon neutrality by 2050 as announced in the JFE Group Environmental Vision for 2050. We are particularly focused on a technology that combines a CR blast furnace and CCU, which allows us to efficiently mass produce high-grade steel and reuse the CO2 in the blast furnace. This technology is focused on achieving virtually zero emissions by using the remaining CO2, which cannot be fully reused to manufacture basic chemicals such as methanol.
Demonstration Tests for NEDO Project (GREINS) for Hydrogen Utilization in Iron and Steelmaking Processes
JFE Steel formed a consortium with Nippon Steel Corporation, Kobe Steel, Ltd., and the Japan Research and Development Center for Metals and jointly commissioned the Green Innovation Fund Project (GREINS) of the New Energy and Industrial Technology Development Organization (NEDO) for Hydrogen Utilization in Iron and Steelmaking Processes, and work toward achieving carbon neutrality by 2050.
In order to further advance the development of ultra-innovative technologies to achieve carbon neutrality by 2050, JFE Steel has decided to construct all the necessary facilities for the demonstration tests for the project centrally in the East Japan Works (Chiba district) to increase the efficiency of the development effort. We will work together with consortium members to accelerate the development of ultra-innovative technologies.
Details of the Planned Demonstration Tests
- Carbon-recycling pilot blast furnace (150m3)
Start construction in 2023, start demonstration tests in April 2025, complete demonstration tests by 2026 - Direct reduction compact bench pilot furnace
Start construction in 2023, start demonstration tests in the second half of 2024, complete demonstration tests by 2026 - Pilot electric arc furnace (10 t pilot furnace)
Start construction in 2023, start demonstration tests in the second half of 2024, complete demonstration tests by 2025
Details for each are as follows.
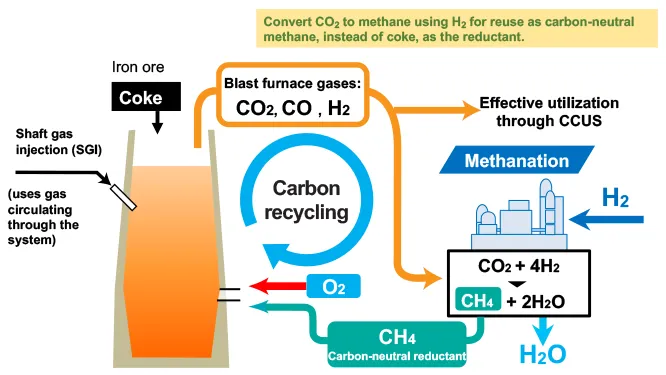
Technical Features of a CR Blast Furnace
The CR blast furnace incorporates an ultra-innovative technology that converts CO2 in the furnace exhaust gas into carbon-neutral methane through methanation, which is then reused as reducing material in the furnace. The technology is expected to reduce CO2 by 50% in the blast furnace process and to ultimately help achieve carbon neutrality by leveraging CCU/CCUS*. The thermal efficiency of the process can be further enhanced by replacing the air blown into the blast furnace with pure oxygen, as the energy used to heat the nitrogen in the air can then be used to heat methane. In addition, the lack of nitrogen facilitates the separation of CO2, so the equipment necessary to separate CO2 for methanation can be more compact and efficient while more effectively using gas at CCUS.
Overview of the Demonstration Tests
We are planning to develop a process that converts the CO2 produced in the blast furnace into methane using hydrogen, allowing the carbon to be repeatedly used in the furnace as a reducing agent and thus reducing CO2 emissions. We will verify the following during demonstration tests.
- Methods for blowing a large volume of methane along with oxygen into the furnace
- Applications for the heating burner that uses the circulation gas
- Methods for linking the operations of the furnace and the methanation facility that converts CO2 from the blast furnace gases to methane
Development of Direct Hydrogen Reduction Technology (Carbon-Recycling Direct Reduction Process)
Hydrogen reduction ironmaking technology is another steelmaking process that the JFE Group is working on to achieve carbon neutrality. With this technology, the natural gas currently used in direct reduction ironmaking is replaced by 100% hydrogen to eliminate CO2 emissions when iron ore is reduced.
Technology for Processing Raw Materials
Currently, the only raw material that can be used for direct reduction ironmaking is high-grade iron ore. Its production volume, however, is limited, and we expect it will become even more difficult to obtain in the future if direct reduction ironmaking were to expand worldwide.
To address this, JFE and one of its iron ore suppliers, BHP, are collaborating in the development of a new raw material processing technology for low- and medium-grade ores, which are currently used as raw materials for blast furnaces due to their large production volume. We are hoping that this new technology will allow us to use low- and medium-grade ores as raw materials for direct reduction ironmaking, thus expanding the raw material sourcing for direct reduction ironmaking.
Technology for Pre-Heating Raw Materials, Technology for Heating Hydrogen Gas
One challenge of hydrogen reduction is that the reduction of iron ore by hydrogen is an endothermic reaction, which means that heat must be applied externally for the reaction to proceed. A sufficient reduction reaction may not take place if there is not enough heat. Thus, technologies for heating raw materials and hydrogen gas must be developed.
Overview of the Demonstration Tests
We are developing a process to convert the CO2 produced in the direct-reduction furnace into methane using hydrogen, allowing the carbon to be repeatedly used in the furnace as the reducing agent and thus reducing CO2 emissions. We will verify the following during demonstration tests.
- Optimal methods for recycling CO2 through methanation
- Methods for using low-grade ores
Carbon-Recycling Direct Reduction Process
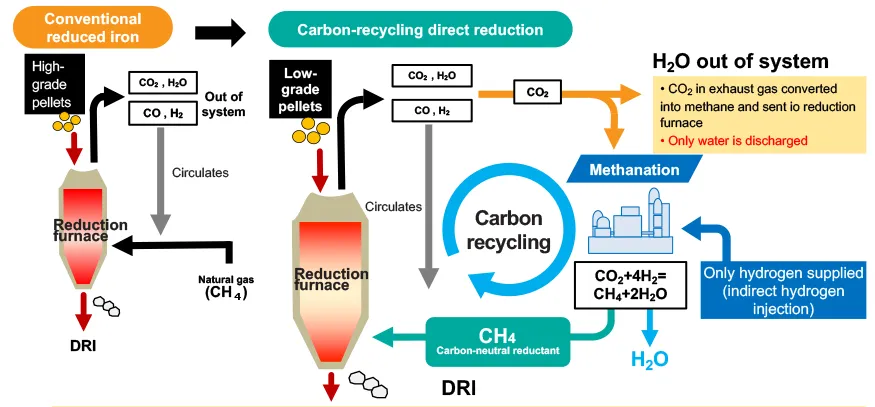
Practical Applications of CO2 Utilization Technologies
JFE Steel is working on the Optimum System for Methanol Synthesis Using CO2, an R&D project, in collaboration with the Research Institute of Innovative Technology for the Earth (RITE) (Figure 1). On-site construction of a test facility commenced in FY2022 in the Fukuyama district of the West Japan Works, with operations scheduled to start in FY2023 and integrated practical application tests to be completed by the end of FY2025. The project focuses on establishing an optimal overall methanol synthetic system, mainly by developing technologies for low-cost CO2 separation and high-efficiency methanol synthesis. The ultimate goal is to combine this newly established system with carbon-recycling blast furnaces and other ironmaking processes to achieve large-scale CCU process.
JFE Steel is also working on an R&D project, Innovative CO2 Sequestration Technology through Quick, Large-quantity Carbonation of Steel Slag, in collaboration with Ehime University (Figure 2). Construction for a practical application test facility is scheduled to commence in FY2023 in the Chiba district of the East Japan Works. The process principles will be verified by FY2022, and tests will be conducted during the FY2024–FY2025 period. The project will develop a new technology to sequester the CO2 generated from ironmaking processes such as carbon-recycling blast furnaces and from nearby thermal power plants in slag, and at the same time verify technologies for recovering heat after carbon sequestration and for converting the steel slag to roadbed materials and other products.
Japan Petroleum Exploration Co., Ltd. (JAPEX), JGC Holdings Corporation (JGC HD), Kawasaki Kisen Kaisha, Ltd. (“K” LINE), The Chugoku Electric Power Co., Inc. (EnerGia), Nippon Gas Line Co., Ltd. (NGL), and JFE Steel have agreed to jointly evaluate the establishment of a CCS (Carbon Capture and Storage)*1 value chain originated from Japan and concluded a Memorandum of Understanding (MOU). The six companies will conduct the joint evaluation, collaborating with the CCS commercialization project development, to establish the CCS value chain, from CO2 separation and capture at JFE Steel’s steelworks and EnerGia Group’s power plant to marine transportation (including domestic marine transportation in the Setouchi area) of liquefied CO2 to the receiving point(s) in Malaysia, including estimation of required facilities and costs.
By executing the joint evaluation for the early commercialization of the CCS project, JAPEX, JGC HD, “K” LINE, JFE Steel, EnerGia, and NGL aim to contribute to realizing carbon neutrality by 2050, including the realization of a de-carbonized society in Asia targeted by the Asia Energy Transition Initiative (AETI)*2.
Figure 1
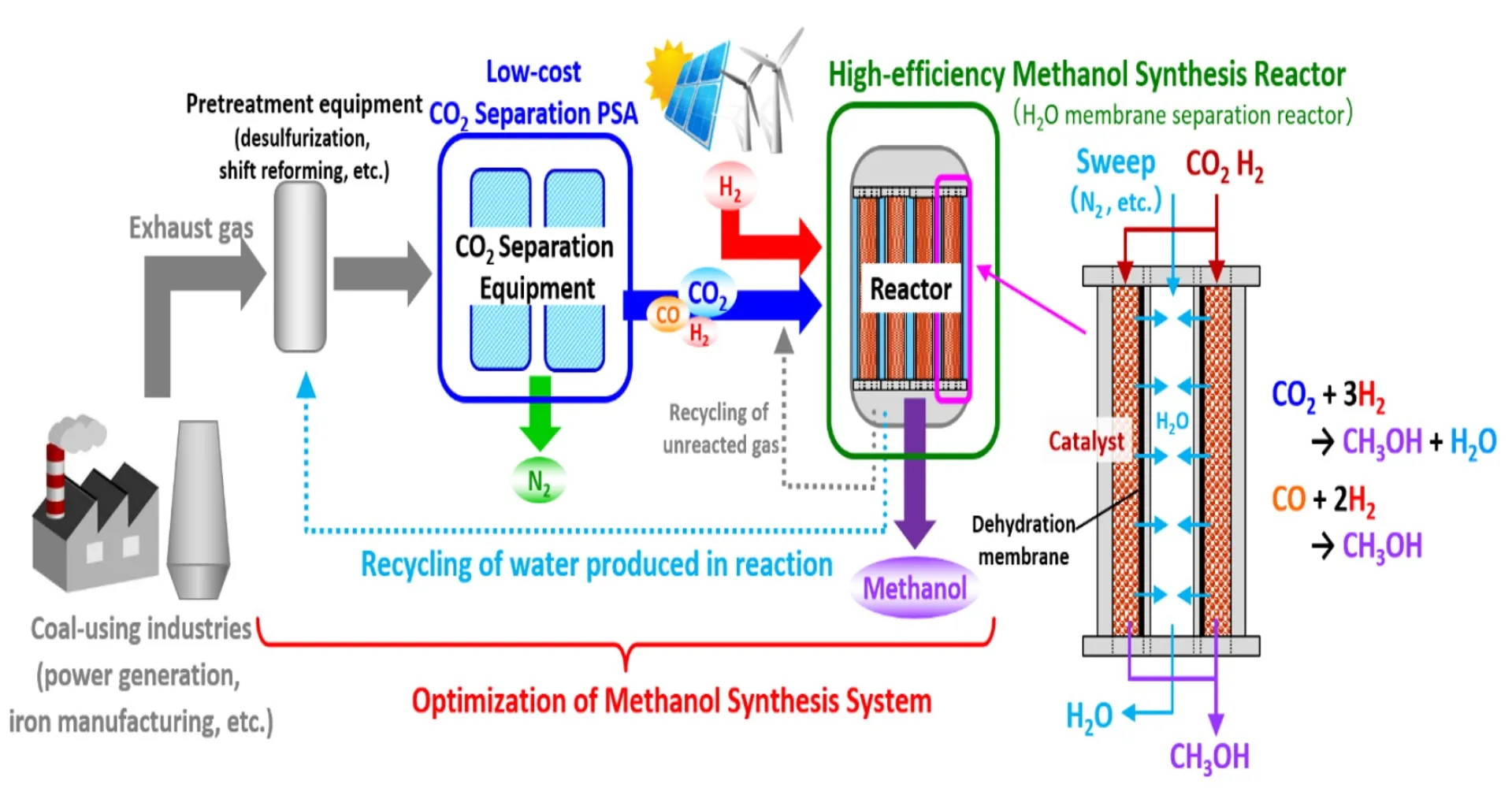
Figure 2
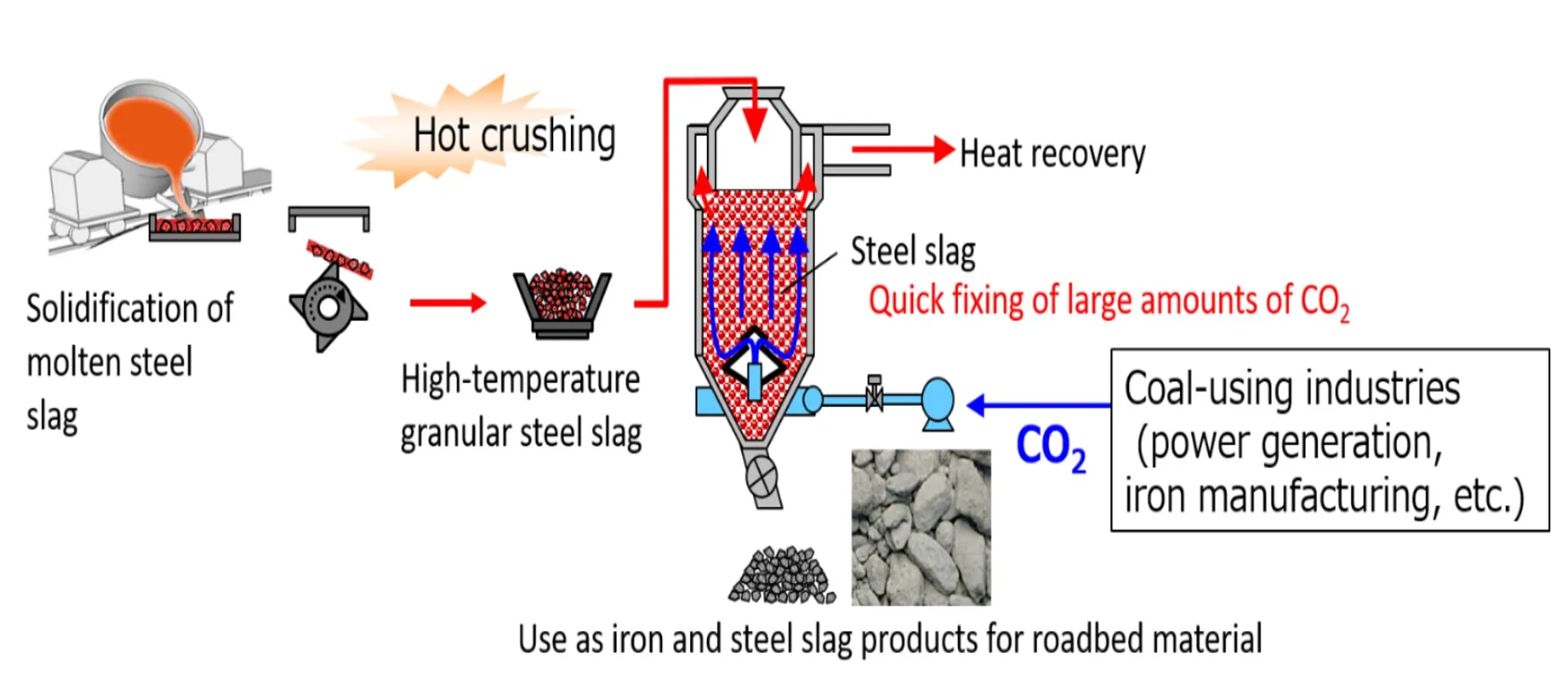
- *1 A technology for capturing CO2 from exhaust gases and storing it underground.
- *2 The Japanese Government’s initiative announced in May 2021 for simultaneously achieving sustainable economic growth and carbon neutrality in Asia.
関連する商品・技術一覧
Roadmap to Carbon Neutrality in 2050
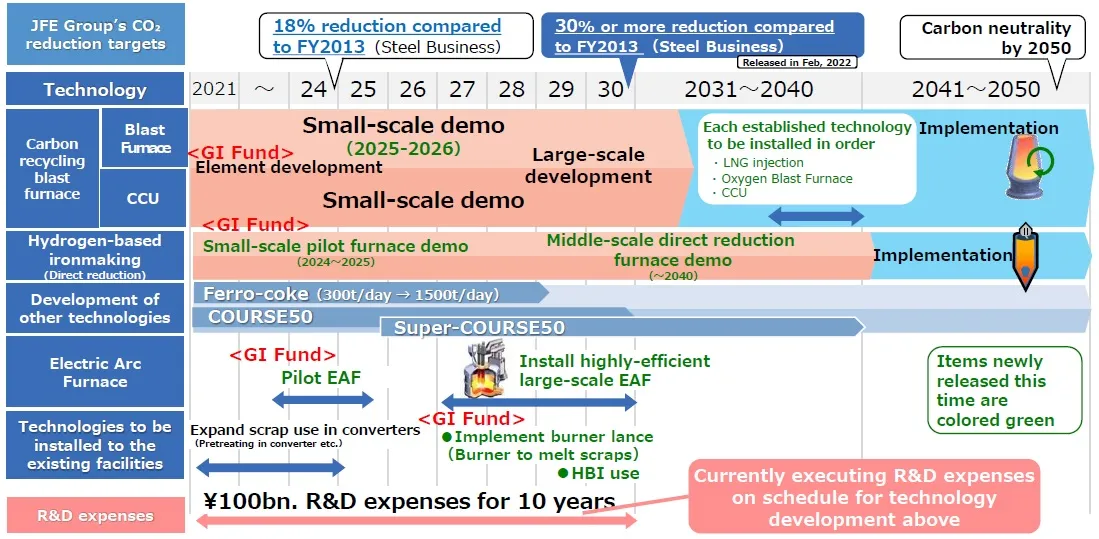
Expand Contributions to CO2 Emissions Reduction in Society
The JFE Group promotes various initiatives to reduce CO2, mainly through JFE Engineering’s businesses. Furthermore, in areas where demand is expanding, such as electrical steel sheets, we are working with the relevant operating companies to maximize the effectiveness of these initiatives.
Contribution to CO2 Reduction through our Engineering Business
Demand is expected to rise for power generation plants using renewable energy sources that do not emit carbon. Through JFE Engineering, the JFE Group is handling the design, procurement, construction, and operation of various renewable energy generation plants including biomass, geothermal, solar, and onshore wind power. We are also working to increase the amount of power generated at waste treatment facilities in order to promote recycling and the effective use of resources.
Furthermore, we are actively engaged in the retailing of electricity, which uses these renewable energies as the main power source, supporting the establishment and operation of new regional electricity companies that focus on local production and consumption of energy using renewable sources, and in expanding the Multisite Energy Total Service (JFE- METS), which optimizes energy use for multiple sites within the same corporate group through centralized management.
As new initiatives for carbon neutrality, we are developing a technology to safely and efficiently transport large amounts of hydrogen, ammonia, and CO2, and working on demonstrating a process that separates and collects CO2 for reuse from the exhaust gas of waste treatment facilities.
As new initiatives for material recycling, we are working on bottle-to-bottle, an effort through which collected PET bottles are recycled and used as raw material for bottles, and the recycling of solar panels that are discarded due to age-related deterioration.
These will contribute to reducing CO2 emissions in society by 12 million tonnes by FY2024 and 25 million tonnes by FY2030.
The following key initiatives contributed to CO2 reduction in FY2023.
Large-Scale Biomass Power Generation
Started construction work for the Tahara Biomass Power Plant, one of the largest woody biomass combustion power plants in Japan, with an output of 112,000 kW.
Tahara Biomass Power LLC, a joint venture between JFE Engineering Corporation, Chubu Electric Power Co., Inc., Toho Gas Co., Ltd., and Tokyo Century Corporation, has started construction work on the Tahara Biomass Power Plant. The plant, to be constructed in Tahara, Aichi Prefecture, is one of the largest woody biomass power plants in Japan, with an output of 112,000 kW, and is scheduled to start operations in September 2025.
Food Waste Recycling Power Generation
Construction of a new food waste recycling biogas power generation plant in Fukuoka, Fukuoka Prefecture: J&T Recycling’s first food recycling business in Kyushu.
J&T Recycling Co., a subsidiary of JFE Engineering, and Kankyou Agency have jointly established Fukuoka Bio Food Recycle Co. Ltd. in Fukuoka City to engage in the food waste recycling and biogas power generation business, in which food waste is collected and fermented to produce methane gas, which is then used as fuel to generate power. The plant to be built for the project will accept up to 100 tonnes of food waste per day and generate electricity using methane gas produced by microbial fermentation as fuel (output: 1,560 kW, estimated annual generation: approx. 12,000 MWh). The project will also support the secondary use of fermented sludge and digested liquid generated in the treatment process on nearby agricultural land.
We have other projects for expanding our food waste power generation businesses throughout Japan, including Tohoku Bio Food Recycle Corporation, which is started its food waste power generation in Sendai in May 2022, and Sapporo Bio Food Recycle Corporation in Sapporo, which is constructing a new plant to expand its capacity.
Multisite Energy Total Service (JFE-METS)
The House Foods Group has agreed to adopt the Multisite Energy Total Service at 18 sites across 8 group companies, driving CO2 reduction.
JFE Engineering has signed a basic agreement with House Foods Group Inc. to provide JFE-METS. We will install a gas cogeneration system at the House Foods Shizuoka Plant and use JFE-METS to supply surplus electricity from the system and electricity provisioned by the JFE Group to 18 sites across 8 companies in the House Foods Group nationwide. The service is expected to reduce CO2 emissions by approximately 16.3% and energy consumption by approximately 21.5% (compared to FY2022) at these sites. Operations commenced in April 2024.
CCUS
Contract received for the construction of CO2 liquefaction, storage and loading/unloading facilities, a large-scale, long-distance, lower cost transportation system for liquid CO2 to realize a CCUS society.
JFE Engineering has received an order from Japan CCS Co., Ltd. to construct its CO2 liquefaction, storage, and loading/ unloading facilities (EPC project). The EPC project is aimed at constructing part of the facilities to be used in the NEDO project: Research, Development and Demonstration of CCUS Technology / Large-scale CCUS demonstration testing at Tomakomai / Demonstration testing on CO2 Transportation. We will be involved in the design and construction of onshore facilities capable of liquefying and storing 10,000 tonnes per year of CO2 separated and recovered from coal combustion gas supplied by the Maizuru plant of Kansai Electric Power Co.
PET Bottle Recycling (Bottle-to-Bottle)
Kyoei J&T Recycling Corporation’s West Japan PET Bottle MR Center to start full commercial operation.
Kyoei J&T Recycling, a subsidiary of JFE Engineering, after starting the operations of the flake manufacturing plant in October 2021, has completed the construction of the pellet production line and started full-scale commercial operations at the PET bottle recycling raw material manufacturing plant (West Japan PET Bottle MR center) in Tsu, Mie Prefecture. With an annual processing capacity of 60,000 tonnes (approximately 10 million bottles per day), the plant can recycle approximately 10% of the total number of PET bottles shipped nationwide.
By producing flakes and pellets from used PET bottles and supplying them to bottle manufacturers, we contribute to the production of plastic bottles using 100% recycled materials, which generates 63% less CO2 than the production of crude oil- derived pellets.
Contribute to CO2 Reduction through Group Collaboration
The JFE Group leverages the respective strengths of each operating company and maximizes their synergies by linking projects. Three main projects being implemented through Group collaboration are: (1) initiatives related to the electrical steel sheet strategy, (2) initiatives in the Keihin waterfront areas, and (3) initiatives in the offshore wind power generation business. We will contribute to CO2 reduction and carbon neutrality by developing projects that combine the technologies and know-how of each company.
Electrical Steel Sheets Strategy
Electrical steel sheets are widely used as core materials for electrical equipment such as motors and transformers and therefore play an important role in determining the performance of this electrical equipment. JFE Steel is contributing to reducing CO2 emissions on a global scale by supplying high-performance electrical steel sheets.
Non-Oriented Electrical Steel Sheets—Expand and Strengthen Production Capacity at the West Japan Works (Kurashiki District)
In order to achieve carbon neutrality for society as a whole, a major shift is required in the social structure, from a society that relies on fossil fuels for energy to one that primarily uses carbon-free energy sources. Transitioning to a future society in which electric vehicles (EVs) are the main mobility platform and where zero-emission electricity is the main energy source will depend on highly efficient motors, for which the key materials are high-performance, non-oriented electrical steel sheets.
Our high-grade non-oriented electrical steel sheets improve the performance of EV motors. Their excellent low iron loss property contributes to higher efficiency, while their high magnetic flux density supports downsizing. These characteristics are highly regarded, and many automobile manufacturers use them in products. Demand for such high-grade non-oriented electrical steel sheets is expected to grow rapidly, and to meet this demand, we are investing approximately 49 billion yen at the West Japan Works (Kurashiki district) to double its production capacity in the first half of FY2024.
Furthermore, as the shift toward EVs accelerates, we expect the demand for high-grade non-oriented electrical steel sheets to grow even more rapidly. We have therefore decided to further strengthen the production capacity high-grade non- oriented electrical steel sheets at the West Japan Works (Kurashiki district). Furthermore, we plan to make an additional investment of approximately 46 billion yen to triple the manufacturing capacity of high-grade non-oriented electrical steel sheets for EV main motors by the end of FY2026 (including the effect of the investment already made).
Demand for Non-Oriented Electrical Steel Sheets
(Calculated by JFE, 2020 results = 1.0)
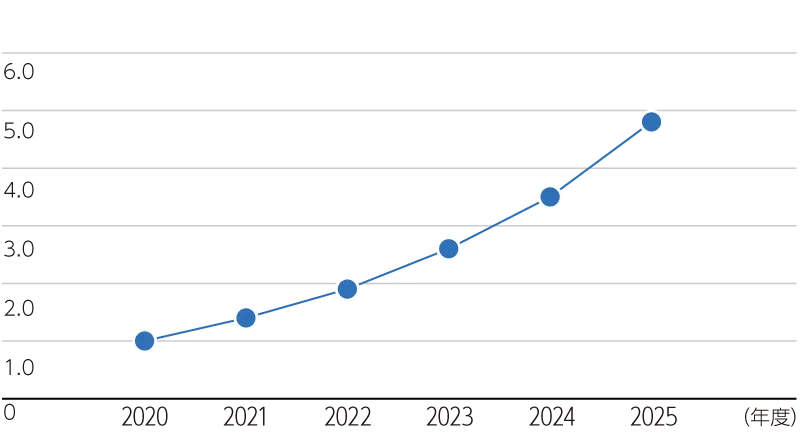
Grain-Oriented Electrical Steel Sheets—Establish a Joint Venture Company with JSW
The global demand for grain-oriented electrical steel sheets in transformers is expected to increase due to continuously growing demand for electric power and the expanding adoption of renewable energy. The demand for grain-oriented electrical steel sheets, particularly in India, is expected to increase by 1.8 times in 2030, compared to 2019.
To this end, in August 2023, JFE Steel and JSW Steel Limited (JSW) signed an agreement to establish a grain-oriented electrical steel sheet manufacturing joint venture company, JSW JFE Electrical Steel Private Limited. We will work with JSW to establish an integrated manufacturing system for this type of steel sheet in India. By locally manufacturing a full line-up of mainly high-grade, energy-efficient grain-oriented electrical steel sheets, in which JFE Steel has accumulated expertise over many years, the joint venture will contribute to the development of a greener power transmission and distribution infrastructure in India and to the remarkable growth of the Indian economy.
The total investment between the two companies is planned to be 670 million dollars, and we plan to begin full production in FY2027.
Demand for Grain-Oriented Electrical Steel Sheets in India
(Calculated by JFE, 2019 results = 1.0)
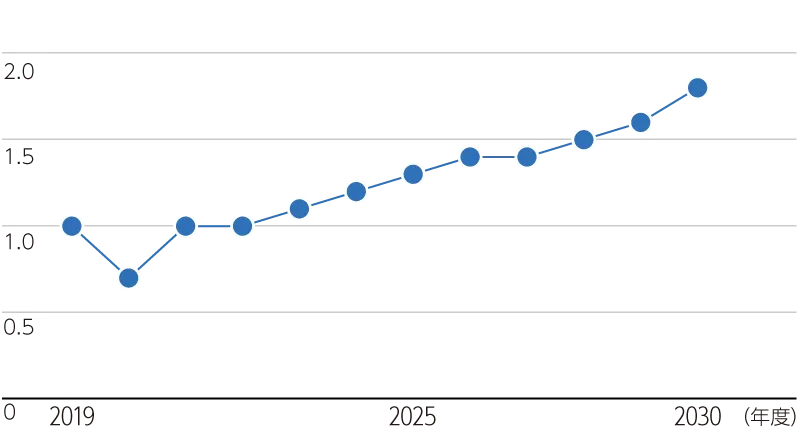
Signed an agreement to establish a grain-oriented electrical steel sheet manufacturing joint venture company
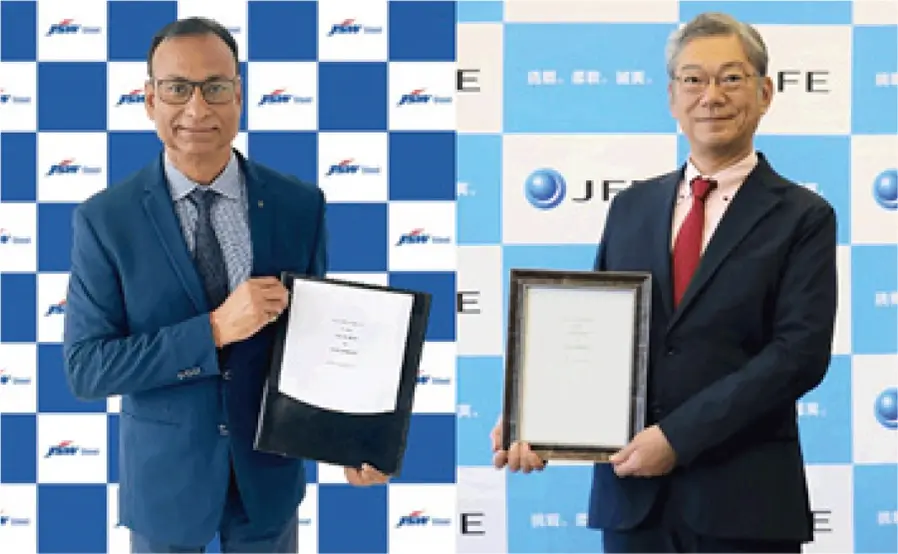
Further Expanding the Global Supply Chain for the Steel Sheets Business (JFE Shoji)
The key factor in initiatives for countering climate change, including those for reducing CO2 emissions, is minimizing electricity loss and using generated electricity without loss. Motors found in places such as power plants, factories and homes are responsible for 40–50% of all electricity consumed globally. In Japan, the ratio is approximately 55%. Improving the efficiency of motors by 1% in Japan would contribute to the equivalent of a 500,000 kW-class power generation plant in energy savings. Motors for electric vehicles, which are expected to become increasingly popular as we move toward a decarbonized society, and industrial motors that are essential for factory automation, need to become even more efficient and lighter through downsizing. In addition, continuous improvement in efficiency is required in transformers, which are essential for distributing electricity from source to factories and homes, in order to minimize energy loss in power transmission and distribution.
JFE Shoji has established a stable global supply chain that includes sourcing high-quality electrical steel sheets which are essential for improving the efficiency of motors and transformers from JFE Steel and other manufacturers and processing the products for meeting customer needs. Customers who require high-quality electrical steel sheets, such as manufacturers of motors and transformers, typically operate manufacturing facilities across the globe. To align with this trend, the company has been working to expand its electrical steel sheets supply chain bases in Japan, America, China, and ASEAN, and recently it has also established a new processing base in Serbia with the aim of starting operations in FY2025. JFE Shoji will continue to take actions to capture demand, such as by reinforcing its stamping facilities at locations in and outside Japan to establish the world’s number one global distribution and processing system for high-quality electrical steel sheets. By further expanding its supply chain and processing capabilities and collaborations with alliance companies, JFE Shoji is striving to significantly improve the distribution and processing of electrical steel sheets.
Related Products and Technologies
Initiatives for Achieving Carbon Neutrality in the Keihin Waterfront Areas
JFE Holdings has released OHGISHIMA 2025, the JFE Group’s conceptual plan for the reuse of land currently occupied by JFE Steel’s East Japan Works (Keihin District), following the suspension of blast furnace operations and other upstream processes there, and in accordance with Kawasaki City’s land use policy. The concept is to create fields of innovation and enterprise that will address the complex challenges involved in the pursuit of carbon neutrality. Through implementation of its OHGISHIMA 2050 plan, the JFE Group aims to convert the land for use on projects that will offer significant public benefit and help address some of the key challenges Japan faces. By attracting new industries and creating jobs that will benefit the country over the next 100 years, the JFE Group hopes to contribute to the sustainable development of local communities and society as a whole.
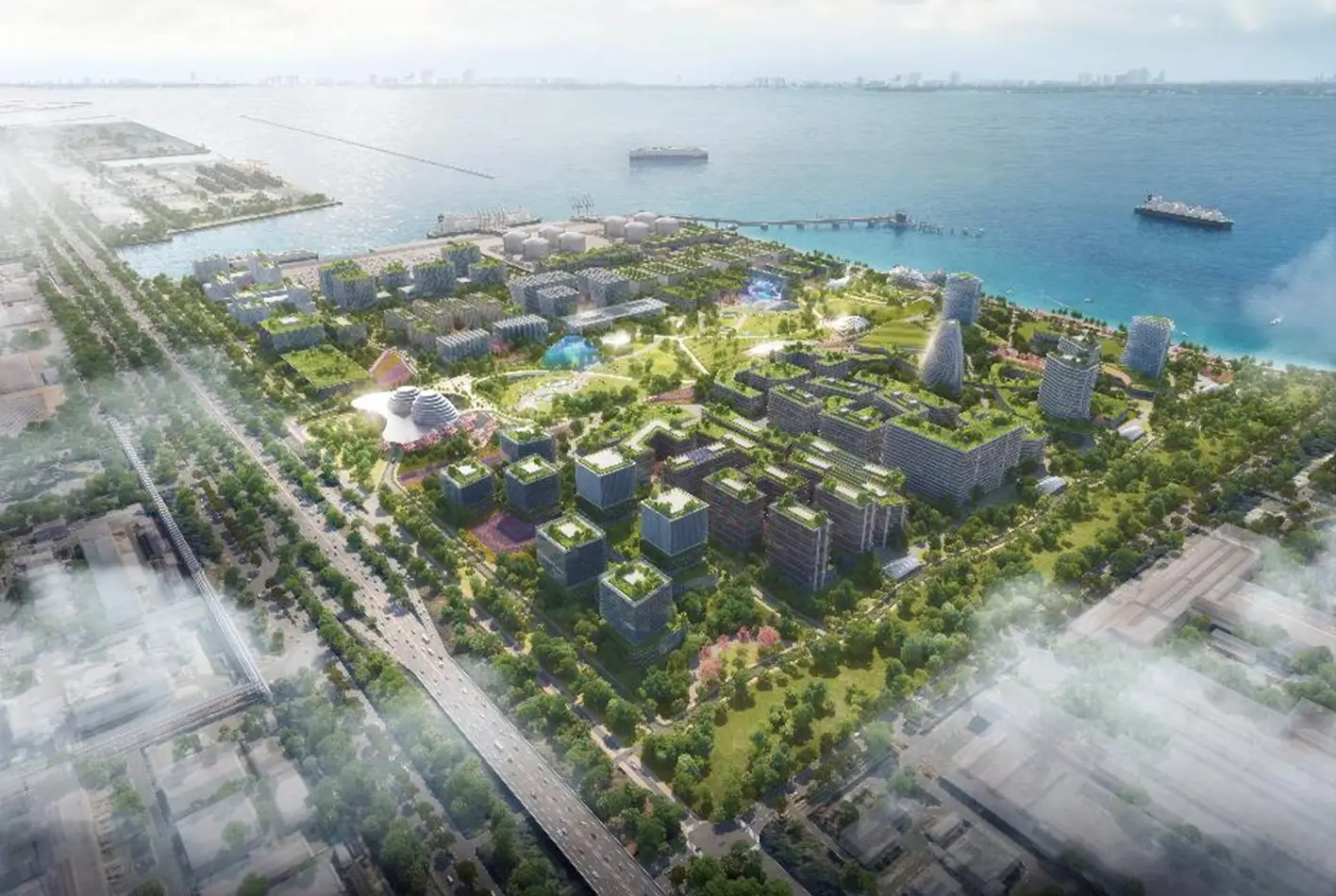
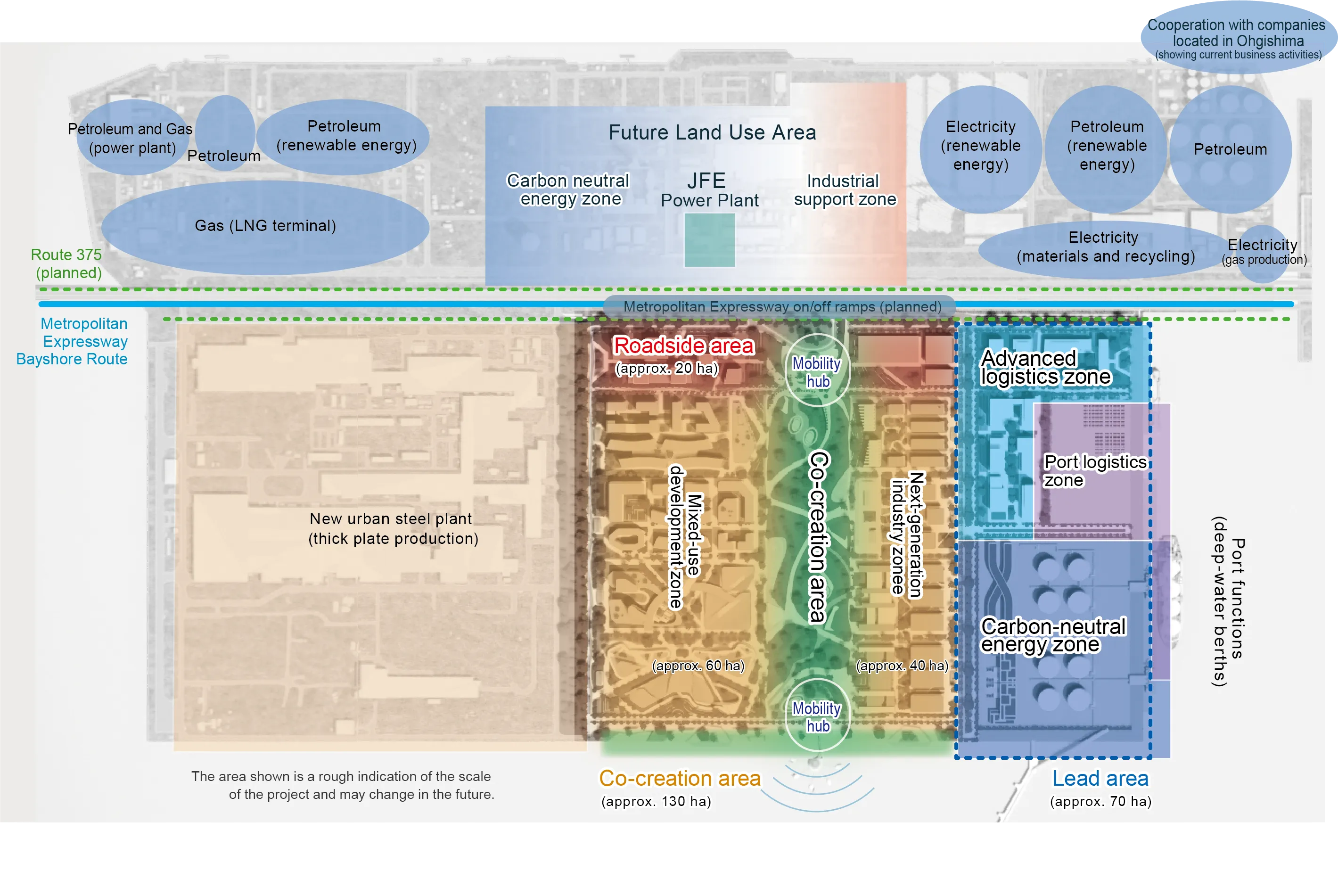
Initiatives for Developing a Hydrogen Supply Hub in the Carbon-Neutral Energy Zone
The Lead Area of the Ohgishima district has been designated as a Carbon-neutral Energy Zone, where hydrogen supply facilities will be deployed. Dramatically improved access to these facilities will support carbon neutrality and innovation across the entire district.
Since April 2022, JFE Holdings, ENEOS Corporation, and JERA Co., Inc. are conducting a joint study on establishing a hydrogen and ammonia receiving and supply base. As part of this effort, we are considering using the deep-water wharves and adjacent land areas of the Ohgishima district. In March 2023, the Kawasaki waterfront area was selected as a candidate site for receiving liquefied hydrogen for the Liquefied Hydrogen Supply Chain Commercialization Demonstration Project, a joint initiative by Japan Suiso Energy Ltd. and ENEOS Corporation that is part of NEDO’s Green Innovation Fund Project: Large-scale Hydrogen Supply Chain Establishment. The three companies have been actively exchanging information, and on July 2024, JFE Steel and Japan Suiso Energy Ltd. signed a land-lease agreement to initiate the necessary construction work in preparation for starting the commercialization demonstration in FY2028.
The JFE Group intends to play a role in building a stable and economical supply chain for hydrogen and other decarbonized fuels, starting with Ohgishima, and to contribute to realizing carbon neutrality in the Keihin waterfront areas and for society as a whole.
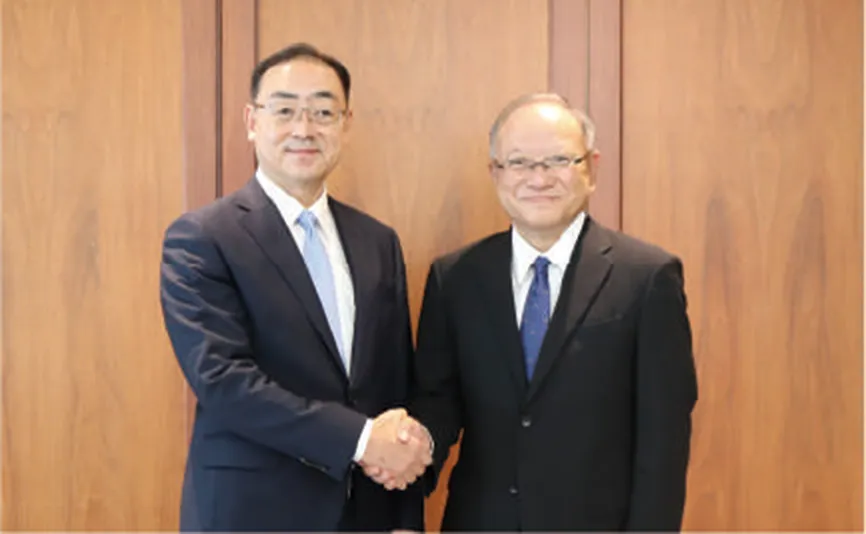
Initiatives for Developing a Recycling Hub in the Mizue District
In order to promote the sustainable development of the Keihin waterfront areas, the JFE Group is focused on comprehensive land management, encompassing site sales, leasing, and business use. In the Mizue district, we are collaborating with Kawasaki City to develop the site as a major recycling hub for the Greater Tokyo region. JFE Engineering’s group company J&T Recycling Corporation established J-Circular System Co., Ltd. as a pioneering project with JR East and other companies, and in April 2024 it started constructing the J Circular System Kawasaki Super Sorting Center, a plastic recycling facility that will be one of the largest in the Greater Tokyo area. The facility is scheduled to begin full-scale operations in April 2025.
Land management target areas in the Keihin waterfront areas
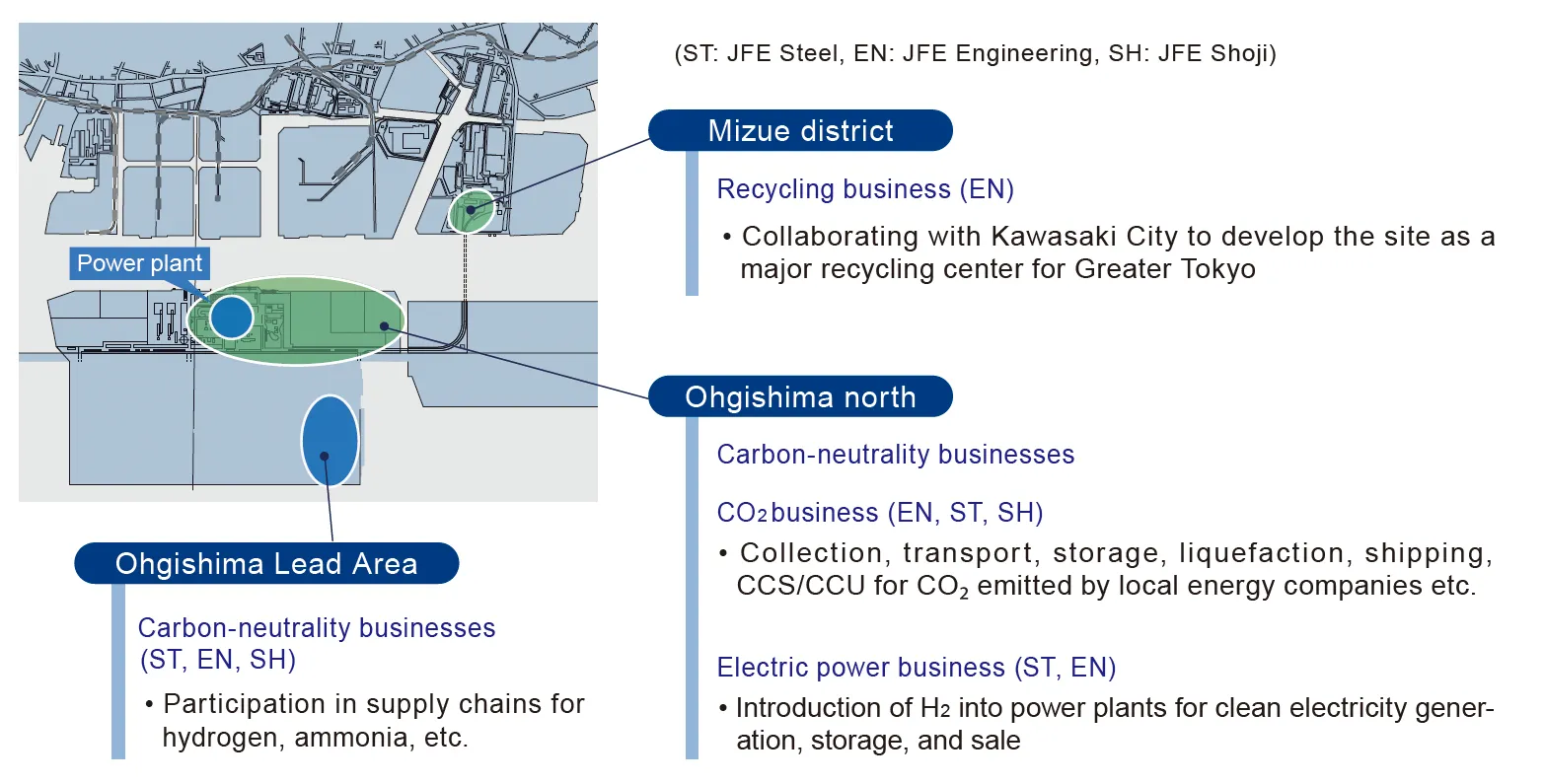
Accelerate Group-Wide Commercialization of the Offshore Wind Power Business
Offshore wind power generation is a key initiative of the Japanese government’s Green Growth Strategy to achieve carbon neutrality by 2050. We will participate in this effort by leveraging the Group’s collective strength with our engineering business acting as the main driver. Specifically, the Group will work on commercializing the manufacturing and O&M* of foundation structures (monopiles, jackets) in addition to establishing a supply chain encompassing material procurement, manufacturing, and O&M. We anticipate this will significantly contribute to the JFE Group’s efforts to achieve carbon neutrality as well as the government’s strategy to achieve carbon neutrality.
- * Operation and maintenance
EN Construction of Monopile Manufacturing Base Completed
JFE Engineering has completed construction of the monopile manufacturing plant in Kasaoka, Okayama Prefecture and operations commenced in April 2024. Monopiles are the foundational structural components for offshore wind power generation and are extremely large steel structures, approximately 10 m in diameter, 100 mm thick, and 100 m long. The plant is the only one in Japan capable of manufacturing such large structures. It was designed for production efficiency, implementing manufacturing processes based on the experiences gained in the manufacturing of large steel structures at the Tsu Works. The plant site includes extensive grounds and a quay from which manufactured structures can be directly shipped, as well as state-of-the-art equipment such as large-diameter bending machines and welding machines for extra-thick plates. When operating at full capacity, the plant is capable of manufacturing up to 100,000 tonnes annually, and it is expected to significantly contribute to the establishment of a domestic supply chain in the offshore wind power generation business and to the realization of carbon neutrality.
Overview of New Monopile Manufacturing Plant (Kasaoka)
Construction site | Kasaoka City, Okayama Prefecture (JFE Steel West Japan Works Fukuyama area) |
Investment amount | Approximately 40 billion yen* (plant building, mechanical equipment, quay reinforcement)
|
---|---|---|---|
Construction start | Site area | Approximately 20 ha (includes storage area) | |
Operation start | Production capacity | Approximately 80,000-100,000 tonnes per year (Approx. 50 sets) | |
Length of shipping quay | 200 m (quay total length: 400 m) | Quay depth | -11 m |
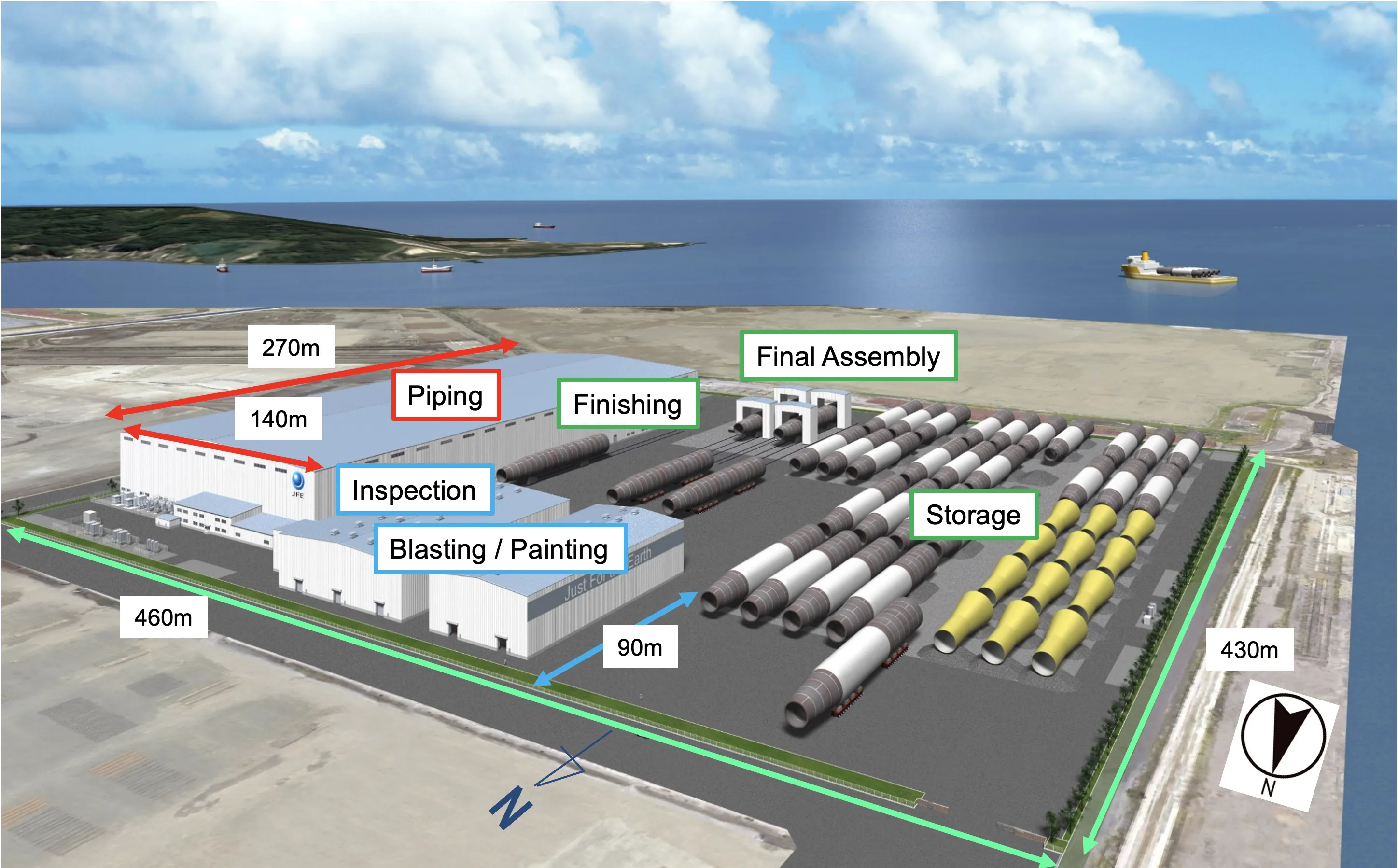
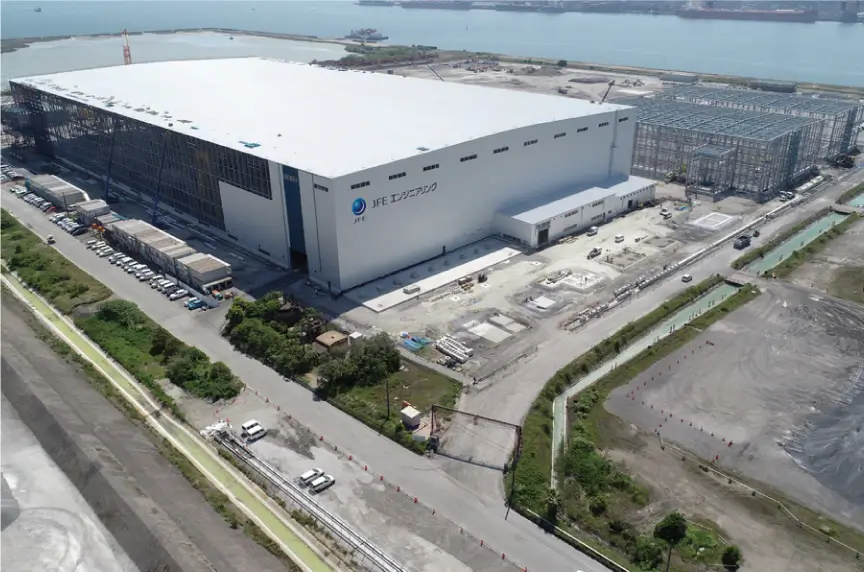
ST Large and Heavy Steel Plates for Offshore Wind Power Generation
The large and heavy steel plate J-TerraPlate™, produced with the No. 7 continuous caster of the Kurashiki Plant at the JFE Steel’s West Japan Works, has been selected for the first time for the production of monopile foundations for offshore wind power generation.
Offshore wind turbines have recently grown in size, requiring larger monopiles and other foundational structures to support them. The monopiles are manufactured by welding ultra-thick steel plates, resulting in increased welding workloads that require monopile manufacturers to improve the efficiency of the operations. Using larger and heavier steel plates makes it possible to reduce the volume of welding operations, compared to conventional small-size plates, and also helps to raise process efficiency while lower manufacturing costs.
We have been investing in equipment at the plate mills and other facilities to manufacture and supply steel plates of up to 37 tonnes (previously limited to around 20 to 28 tonnes per plate in general), the largest in Asia and capable of supporting wind turbines in harsh offshore environments over the long term and in large quantities using the extra-large slabs produced with the state-of-the-art No. 7 continuous casting machine. These investments have resulted in the first-time adoption of this product for the production of monopile foundations.
Manufacturing Process of Large and Heavy Steel Plates for Offshore Wind Power Generation
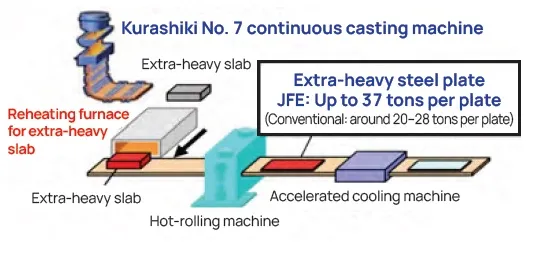
Advantages of Using Large and Heavy Steel Plates for Monopiles
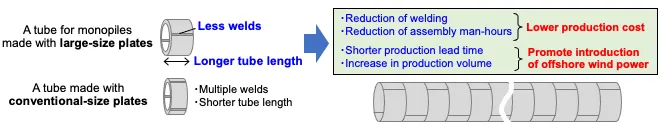
Commercialization of Offshore Wind-Power Business
- By commercializing our manufacturing of foundation structures (monopiles), we will become the forerunner in the business of offshore wind-power generation and establish a supply chain across the entire Group, including foundation manufacturing and O&M.*1
- We will strive to expand business in the field of renewable energy by leveraging the JFE Group’s collective strengths (synergies), with JFE Engineering as the main player.
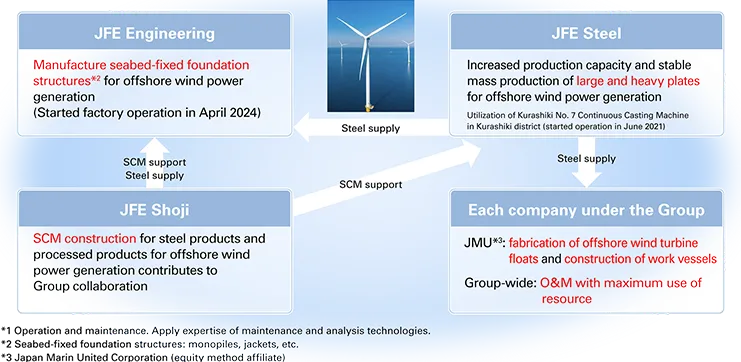
Technologies of Group Companies
Category | Company | Details |
---|---|---|
Foundation structures | JFE Engineering | Seabed foundations (monopiles, jackets, etc.) |
Japan Marine United | Floating foundations (semi-submersible) | |
JFE Steel | High-quality, large and heavy steel plates, high-strength steel (reduced using HBL series steel plates) | |
Construction | Japan Marine United | SEP vessels (self-elevating platform) |
JFE Engineering | JFE-RAPID (cable laying method) | |
Battery systems for power storage | ||
GECOSS | Stands for large steel structures | |
JFE Steel | Natural stone substitute materials (use of steel slags) | |
O&M (operation and maintenance) |
JFE Engineering | Technologies for remote monitoring and operation |
JFE Advantech | Vibration measurement equipment and systems, sea monitoring tools (water quality, sea conditions) | |
Japan Marine United | Offshore support vessels (work vessels) | |
JFE Plant Engineering | Wind turbine maintenance (diagnosis and repair) | |
JFE Technos | Technologies and expertise in planning, constructing, and maintaining onshore turbines | |
JFE Techno-Research | Equipment evaluation and analysis for corrosion, fatigue, vibration, etc., diagnosis of remaining service life, strength and durability testing and evaluation techniques for large structures | |
Supply chain | JFE Shoji | Contribution to optimizing offshore wind power generation project execution |
SH Building a Supply Chain for the Offshore Wind Power Generation Industry
Initiatives toward carbon neutrality are expanding around the world to tackle the shared issue of climate change. Japan has set its goal to achieve carbon neutrality by 2050 and formulated the Sixth Strategic Energy Plan in 2021 to lay out strategies to that end. These ambitious strategies include reducing greenhouse gas emissions by 46% in FY2030, boosting renewable energy in its electricity mix to 36–38%, and increasing the ratio of wind in the renewable energy mix to 5% (generating capacity of 23.6 GW) compared to the 0.9% (generating capacity of 4.5 GW) in FY2019.
As for offshore wind power generation, the industry is planning projects that will achieve 10 GW capacity by 2030 and 30–45 GW by 2040. Steadfast efforts are also being made to adopt a large number of internationally competitive technologies, such as the adoption of a demonstration project for a floating offshore wind power generation system under the Green Innovation Fund.
JFE Shoji is collaborating with a local enterprise that manufactures the windmill foundations in Taiwan, which is leading in the offshore wind power generation market, and have been achieving progress regarding supply chain of steel materials for foundation structures. Looking ahead, the company will capitalize on the knowledge acquired and contribute to the realization of carbon neutrality by establishing a supply chain that supports the domestic production of goods and the local economy while also meeting customer demand in the offshore wind power generation industry in Japan.
Adapting to Climate Change (Contribution to Achieving Societal Resilience)
Contributions to Disaster Prevention and Mitigation and Increased National Resilience
The JFE Group is not only focused on reducing CO2 emissions (climate change mitigation); we also intend to contribute to the resilience of society in general by adapting to climate change.
With infrastructure such as hybrid tide embankments and permeable steel slit dams, the Group will contribute to preventing and mitigating disaster-related damage to infrastructure critical to daily life and economic activities, and to strengthening their resilience.
Hybrid Tide Embankments
Hybrid tide embankments are made of steel and concrete. Because of their hybrid structure, they require shorter construction time and less space.
Concrete blocks for hybrid tide embankments are precast at a JFE Group factory, while steel pipe piles for foundations are installed at the construction site, thereby reducing the time required for on-site construction by about 60%. This arrangement does not require large amounts of materials, equipment, or workers on site, so it does not interfere with other construction work. Furthermore, compared to a conventional embankment structure, the land area occupied by the embankment can be reduced by about 80%, saving considerable space. We will continue to apply and advance our technology to further contribute to disaster prevention in the region.
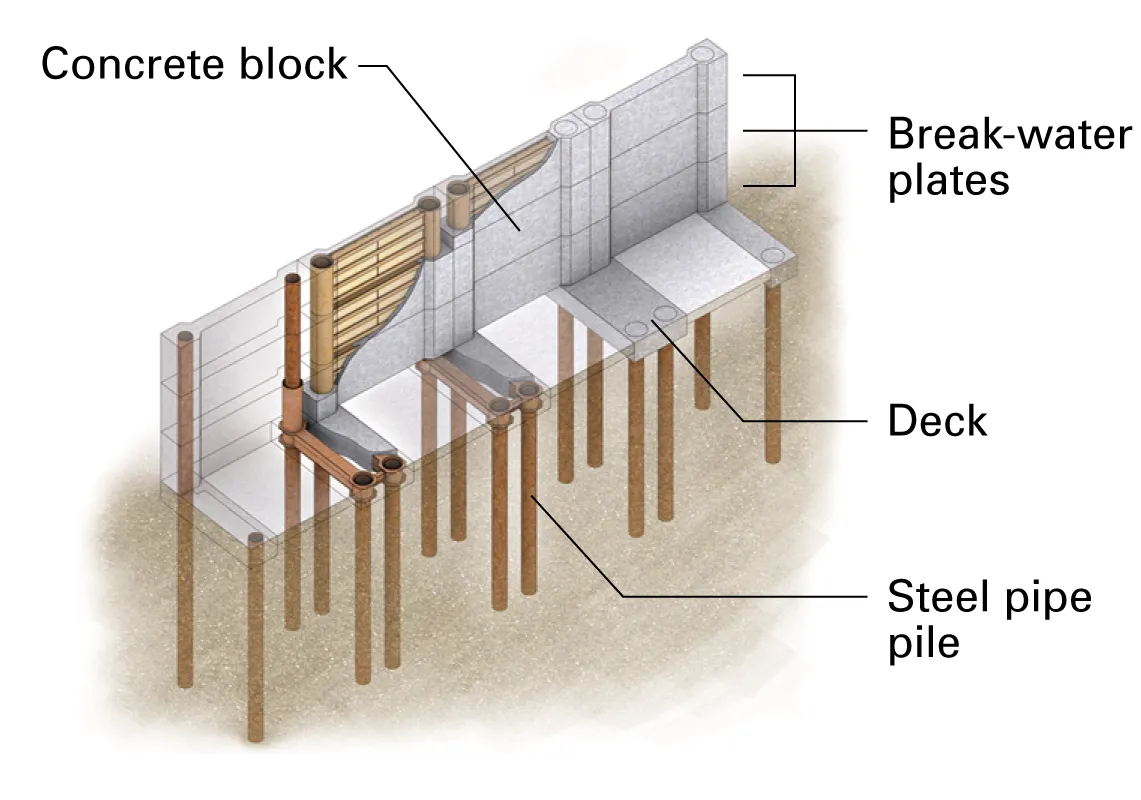
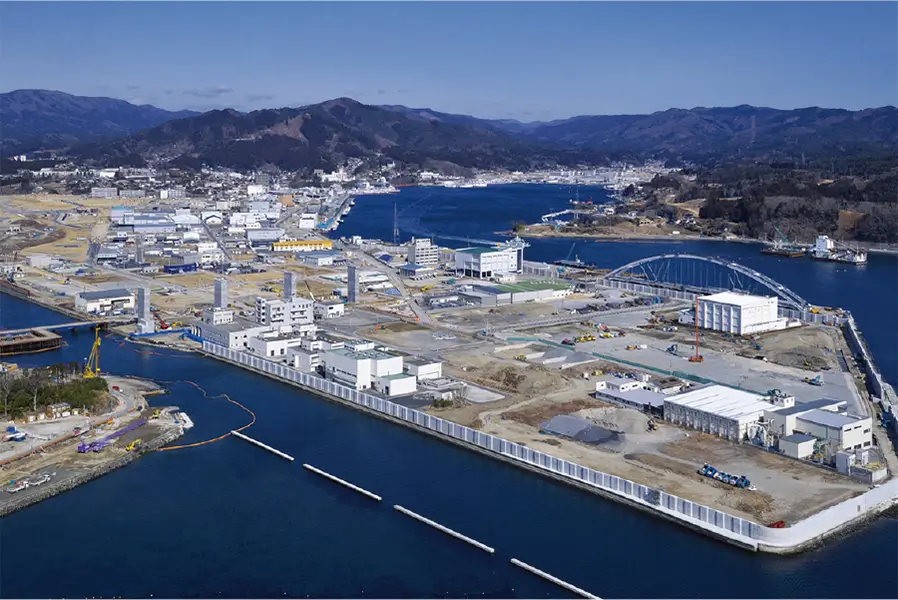
Permeable Steel Slit Dams
A permeable steel slit dam is a steel pipe structure installed in a river to trap debris flows.
Made of strong steel pipes to withstand the impact of driftwood and huge debris, it has large openings to let water and sediment to pass through, which prevents the water level from rising upstream during floods and also ensuring that debris does not flow downstream. Since it does not block the flow of water, unlike a dam, it can be shaped to the slope of a riverbed to protect the ecosystem. The JFE Group is working to expand the use of permeable steel slit dams by reducing installation costs and shortening the construction period through structural innovations.
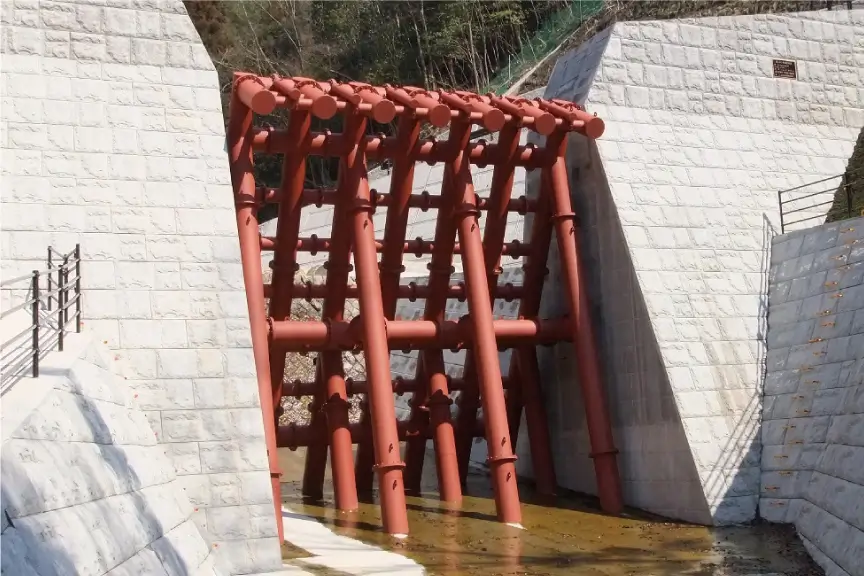
Terre Armée Method
The Terre Armée method drove the spread of the reinforced soil technology in Japan. This reinforced soil wall construction method was introduced to Japan about half a century ago, and since then, it has been used in a variety of situations, mainly in domestic infrastructure development, such as highway and other road structures, and the construction of airports, schools, and defense facilities. By applying layers of steel reinforcement in the embankment, friction between the steel strips and the earth results in a vertically strong structure that exhibits excellent earthquake resistance.
JFE Shoji Terre One Corporation, a subsidiary of JFE Shoji, has developed a new Terre Armée method, with an innovative fail-safe system. The feature helps to visually confirm the health of structures after being subject to unforeseen forces, such as massive earthquakes. Being able to easily detect the internal anomalies of reinforced embankments helps to determine the safety of the infrastructure and schedule necessary maintenance work in a timelier manner.
We will contribute to building disaster-resistant roads and towns by promoting the Terre Armée method and by expanding sales of other products that contribute to disaster prevention, disaster mitigation, and national land resilience.
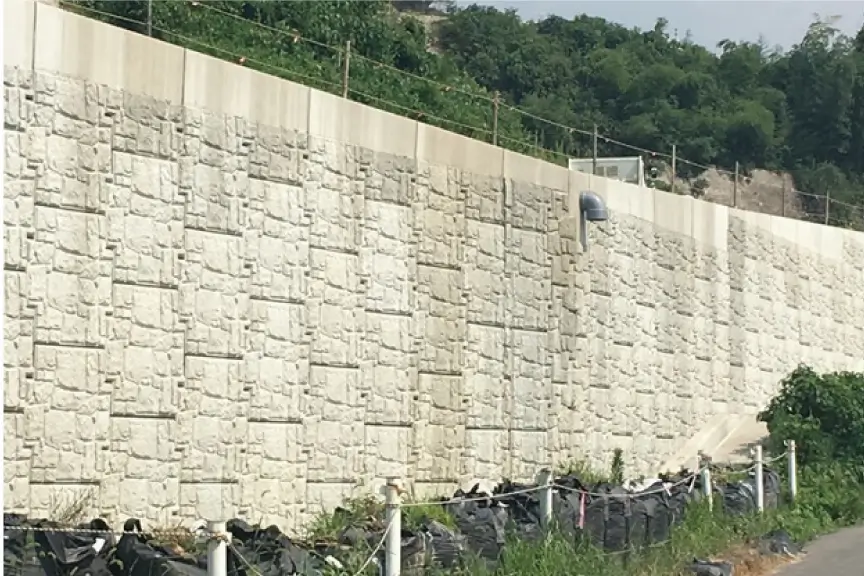
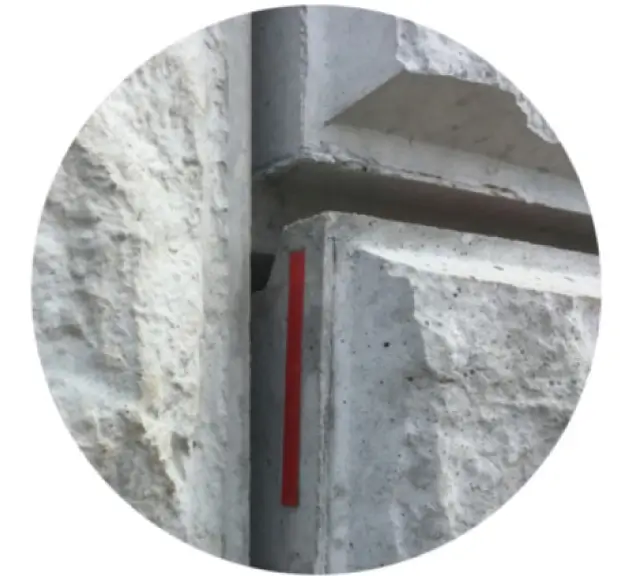
(red indicating internal anomalies)
JFE Group’s Strategy and Alignment with the Paris Agreement
Under the JFE Group Environmental Vision for 2050, the JFE Group designed a roadmap for achieving carbon neutrality, which included our short-, medium-, and long-term CO2 emission reduction targets. Until 2030, the Group will focus on fully using existing technologies to promote decarbonization while at the same time developing the ultra-innovative technologies needed to achieve carbon neutrality. The Group will then focus on commercializing the ultra-innovative technologies in the 2030s and 2040s, when we expect the required social infrastructure to be in place, to accelerate decarbonization toward achieving carbon neutrality by 2050.
The technology roadmap for Transition Finance toward decarbonization in the iron and steel sector, published by the Japanese Ministry of Economy, Trade, and Industry (METI), outlines a path for accelerating decarbonization and achieving carbon neutrality by introducing innovative technologies, with the same assumption that social infrastructure such as hydrogen supply and CCUS will be in place by the 2040s. This technology roadmap is aligned with Japan's Nationally Determined Contribution (NDC) based on the Paris Agreement, and is therefore aligned with the Paris Agreement.
In 2022, the JFE Group issued transition bonds through a public offering, which was selected as the first model example in the iron and steel sector for METI’s Transition Finance Model Projects in FY2021. During the evaluation process for this issuance, the Group’s initiatives were certified by a third party as being aligned with METI’s roadmap. We can therefore deduce that they are also aligned with the Paris Agreement.
- METI: Technology Roadmap for Transition Finance in the Iron and Steel Sector
- METI: Transition Finance Case Study
Risk Management (Climate Change)
JFE Holdings is responsible for comprehensive risk management in accordance with its Basic Policy for Building Internal Control Systems. The JFE Group Sustainability Council, chaired by the president of JFE Holdings, consolidates information and strengthens management across the Group to reduce the frequency and impact of risks.
The executive officer responsible for risk strives to identify potential ESG risks such as those associated with climate change. As necessary, the council confirms and evaluates risks and discusses and determines countermeasures. Key managerial issues are deliberated by the Group Management Strategy Committee.
The Board of Directors supervises initiatives on ESG risks such as those related to climate change and CSR by discussing, making decisions on, and receiving reports about these matters.
Climate-related risks are identified and evaluated based on a scenario analysis conducted under the framework recommended by the TCFD in 2017. Key factors that may affect management are selected for further analysis and incorporated into formulating business strategies, such as the Seventh Medium-term Business Plan.
Monitoring Method for Climate Change-Related Risks
Issues that may affect management are monitored by the JFE Group Sustainability Council, Group Management Strategy Committee, and Management Committee. Measures are implemented based on a quarterly report on climate change-related risks deliberated by the specialized committees of each Group company (e.g., the Environmental Committee). The JFE Group Environmental Committee consolidates information and strengthens management to reduce the frequency and impact of risks and to maximize opportunities.
Countermeasures Based on Monitoring
- Group-wide deliberations
- Monitoring penetration of policies within the Group
- Monitoring deployment of policies throughout the Group
For further details, refer to the following links.
Metrics and Targets (Medium- and Long-Term Targets and Results in FY2023)
The JFE Group’s steel business is led by its operating company, JFE Steel, which is a member of the Japan Iron and Steel Federation (JISF). The JFE Group is promoting the JISF’s Commitment to a Low Carbon Society, which focuses on the Three Ecos initiatives and the development of innovative new iron and steelmaking processes. Under the initiative, the JISF’s target for FY2030 had originally been to reduce emissions by 9 million t-CO2. However, with the end of Phase I of this initiative in 2020, it was rebranded as the JISF’s Carbon Neutrality Action Plan, and the Phase II target (FY2030 target) was revised to a 30% reduction in energy-derived CO2 emissions in FY2030, compared to FY2013. JFE Steel is aggressively pursuing the achievement of this goal.
In addition, JISF has formulated and announced the Long-term Vision for Climate Change Mitigation in 2030 and beyond, which is intended to realize zero-carbon steel. JFE Steel played a key role in formulating this vision. Furthermore, in 2021, the JISF announced the “Basic Policy of the Japan steel industry on 2050 Carbon Neutrality sought by the Japanese government,” declaring that the Japanese iron and steel industry will boldly take on the challenge of realizing zero-carbon steel.
The JFE Group intends to increase sustainability through solutions that address global climate change while restructuring to respond to developments in the environment facing our steel business. We considered 2020 to be the landmark year for further reinforcing our efforts to tackle climate change, and we declared our target to reduce CO2 emissions in the steel business in FY2030 by 20% or more, compared to FY2013, and to achieve carbon neutrality by 2050.
In May 2021, the JFE Group placed top priority on its climate change initiatives and formulated the JFE Group Environmental Vision for 2050 as part of the Seventh Medium-term Business Plan, under which we will strive to achieve carbon neutrality by 2050. The Group also disclosed new CO2 emissions reduction targets, and in February 2022, the FY2030 target for the steel business was revised upward to 30% or more, compared to FY2013. Major Group companies of JFE Steel have formulated CO2 reduction targets at the same level as JFE Steel. The Group companies in Japan and overseas work together to incorporate efforts to address climate change issues into their business strategies. The Group will systematically pursue the reduction of CO2 emissions by incorporating the TCFD’s principles in its management strategies.
JFE Group’s CO2 Reduction Targets
Seventh Medium-term Business Plan Initiatives
- Reduce steel-business CO2 emissions in FY2024 by 18%, compared to FY2013 (JFE Steel).
Furthermore, JFE Steel’s major group companies have also set their own CO2 reduction targets for FY2024 to ensure that these targets are achieved. With this, more than 99% of the total CO2 emissions of the entire JFE Steel Group is accounted for. - The target of reducing CO2 in FY2030: 30% or more, compared to FY2013 (JFE Steel)
Initiatives for Carbon Neutrality by 2050
- Reduce CO2 emissions at JFE Steel
- Pursue ultra-innovative technologies, mainly for carbon-recycling blast furnaces and CCU
- Develop hydrogen-based ironmaking (direct-reduction) technology
- Develop electric arc furnace process technology
- Expand engineering business contributions to CO2 emissions reduction in society
- Reduce CO2 emissions by 12 million tonnes in FY2024 and 25 million tonnes in FY2030
- Offshore wind power generation business
- Accelerate commercialization of our offshore wind power business by applying the strengths of the Group
CO2 Emissions of the JFE Group
CO2 Emissions of the JFE Group
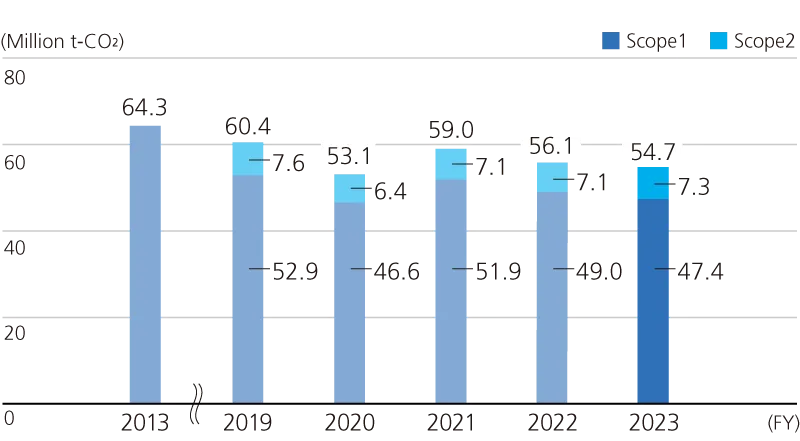
- Notes:
- - Data cover 75 companies
JFE Steel and 26 major domestic and overseas subsidiaries
JFE Engineering and 11 major domestic and overseas subsidiaries
JFE Shoji and 35 major domestic and overseas subsidiaries - - Data for JFE Steel include CO2 emissions from non-energy sources.
- - Starting with FY2018, data for JFE Steel’s subsidiaries and JFE Engineering’s subsidiary include CO2 emissions from nonenergy sources.
- - FY2013 figure includes data for the Sendai Works of JFE Bars & Shapes Corporation.
- - Since FY2021, the figures include data for an expanded list of JFE Steel, JFE Engineering, and JFE Shoji major subsidiaries.
Scope 3 Emissions of the JFE Group (FY2023)
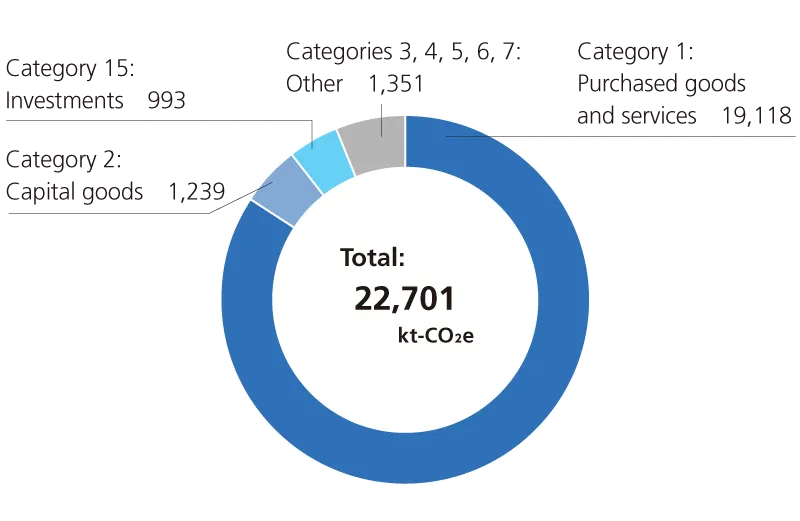
- Coverage:(Categories 1, 2, 3, 4, 5) JFE Steel, 21 JFE Steel major domestic subsidiaries, JFE Engineering, 1 JFE Engineering major subsidiary, and JFE Shoji
(Category 6, 7) JFE Steel, 21 JFE Steel major domestic subsidiaries, JFE Engineering, 12 JFE Engineering major domestic and overseas subsidiaries, and JFE Shoji
(Category 15) Japan Marine United, and 10 JFE Steel equity-method affiliates (7 domestic and 3 overseas) - Sources:Green Value Chain Platform (Ministry of the Environment) and others
For more on quantitative data related to CO2 emissions, refer to the following information.
ST Initiatives to Save Energy and Reduce CO2
JFE Steel has always aggressively pursued CO2 reduction and energy savings, including the introduction of energy-saving equipment.
ST Energy Consumption and CO2 Emissions in FY2023
Production of Crude Steel of JFE Steel
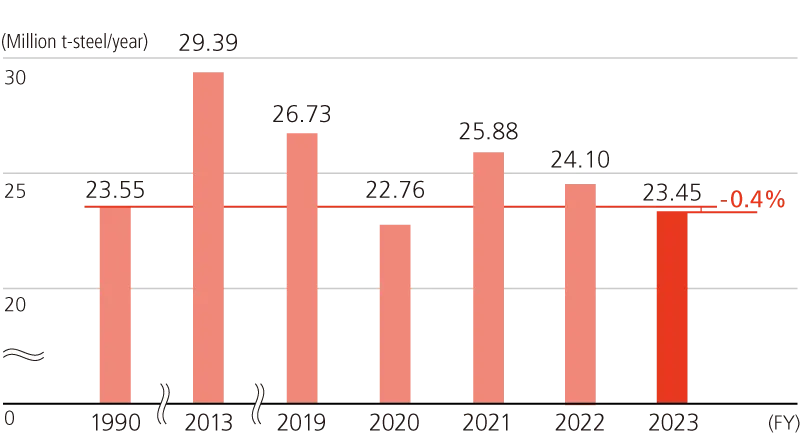
- Note:FY2013 figure includes data for the Sendai Works of JFE Bars & Shapes Corporation.
Energy Consumption and Unit Energy Consumption of JFE Steel
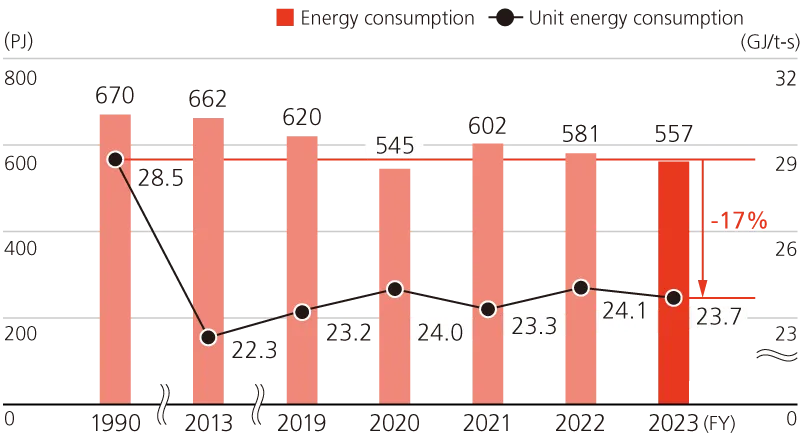
- Note:FY2013 figure includes data for the Sendai Works of JFE Bars & Shapes Corporation.
CO2 Emissions from Energy Sources and Unit CO2 Emissions of JFE Steel
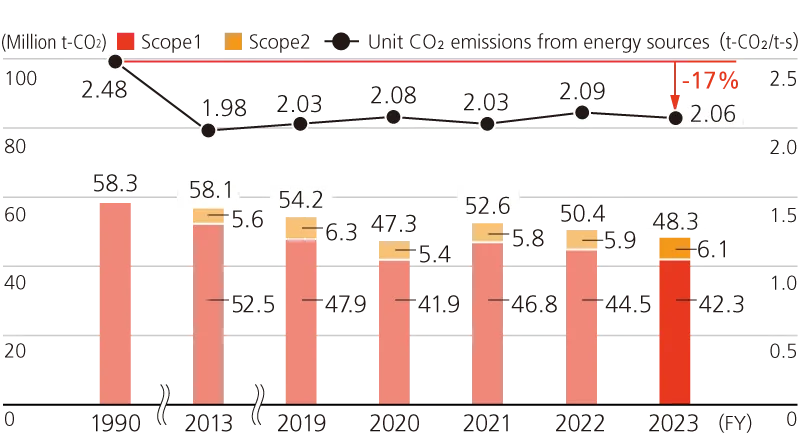
- Notes:
- - The CO2 emissions and emission intensity in FY2023 are calculated using the CO2 emission factor for electricity purchased in FY2022, adopted by the Japan Iron and Steel Federation’s Commitment to a Low Carbon Society.
- - FY2022 data was revised by applying the CO2 emission factor for electricity purchased in FY2022, as adopted by the Japan Iron and Steel Federation’s Commitment to a Low Carbon Society.
- - FY2013 figure includes data for JFE Bars & Shapes Corporation’s Sendai Works.
EN Initiatives to Reduce CO2 Emissions through Business Operations
JFE Engineering contributes to CO2 emissions reductions in society as a whole through its business operations, such as by expanding renewable energy generation and constructing and operating plastic and food recycling plants. In FY2023, the Company contributed to reducing 11.53 million tonnes of CO2 emissions (a 3% increase compared to FY2022) across society. JFE Engineering will further expand its business and contribute to CO2 emissions reductions of 12 million tonnes in FY2024 and 25 million tonnes in FY2030.
In addition, since FY2021 we have been implementing such initiatives as subscribing to on-site solar power PPA and zero-emission electricity plans at the Yokohama office and a low-emission electricity plan at the Tsu Works. As a result, in FY2023 we have achieved a 28% reduction in CO2 emissions, compared to FY2013. We have also been working on reducing waste and implementing energy-saving activities at our steelworks and in our offices. The Company will steadfastly conduct business in ways that save resources and are environmentally sound, including expanding the use of renewable energy.
JFE Engineering’s Contribution to CO2 Emissions Reductions (FY2023)
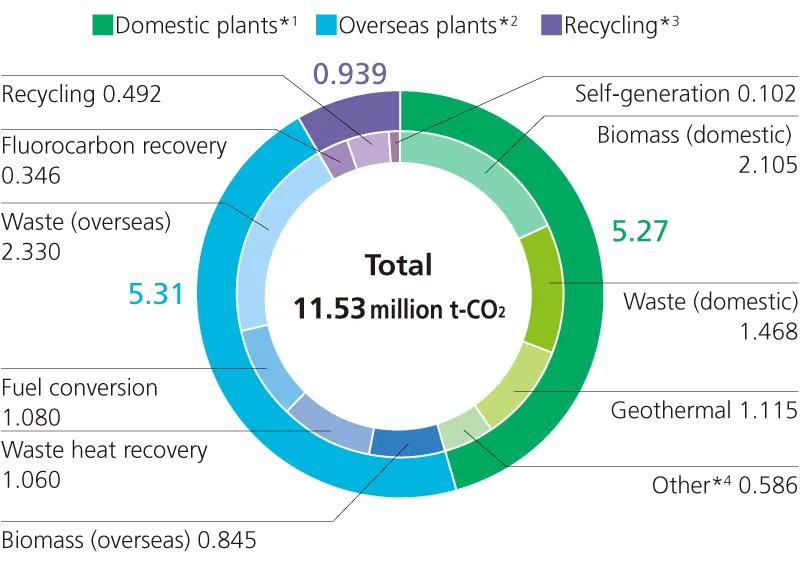
- *1 Data cover JFE Engineering.
- *2 Data cover JFE Engineering and Standardkessel Baumgarte GmbH (SBG), a German subsidiary of JFE Engineering Corporation.
- *3 Data cover J&T Recycling Corporation and JFE Urban Recycle Corporation.
- *4 Other includes digestion gas, geothermal, solar, wind, waste heat recovery, fuel conversion, energy service, and logistics products.
JFE Engineering Group’s CO2 Emissions from Energy Sources
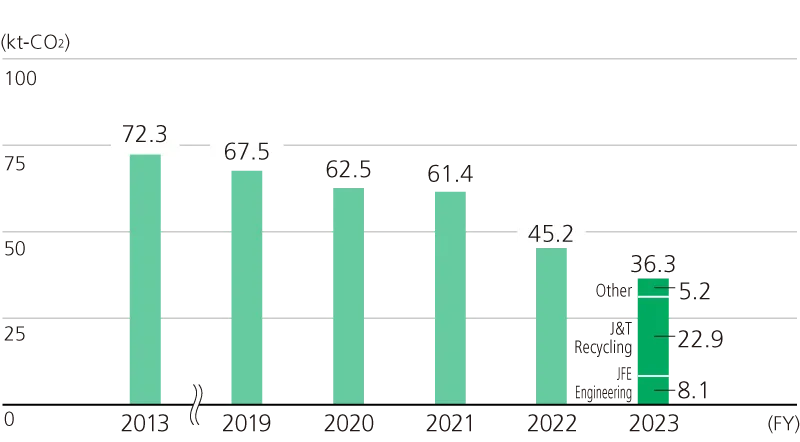
- Notes:
- - Data cover JFE Engineering and 11 major domestic and overseas subsidiaries.
- - FY2021 figure includes data for an expanded list of JFE Engineering major subsidiaries.
SH Energy Reduction Initiatives in Accordance with Environmental Strategies
Under the environmental strategies formulated in 2001, JFE Shoji is continuously implementing initiatives to reduce paper and electricity consumption and strictly manage waste separation as part of its energy reduction efforts.
In terms of reducing paper consumption, the company continues to use recycled paper to conserve natural resources, and we also ensure that documents are printed in black and white using both sides of the paper. We are also promoting paperless meetings through the use of large monitors and web conferencing systems. Consequently, the amount of paper used per employee is on a downward trend. As for electricity consumption, JFE Shoji is reducing its environmental impact by introducing motion-sensor lighting and energy-saving equipment through office renovations, implementing leave-on-time days, improving operational efficiencies through robotic process automation (RPA), and other measures.
In addition, the company has established a new goal in the domestic operating companies to reduce CO2 emissions by installing solar panels and purchasing electricity derived from renewable energy sources. In February 2023, we completed installing solar panels, which in October began generating electricity at JFE Shoji Coin Center Corporation in Shizuoka and then at Tochigi Shearing Corporation, a Group company that processes steel plates. As a result of this and other ongoing efforts to reduce the amount of electricity consumed, CO2 emissions in FY2023 in the domestic operating companies were reduced by 20.7%, compared to FY2019.
Electric Power Consumption by JFE Shoji

CO2 Emissions of the JFE Shoji Group (FY2023)
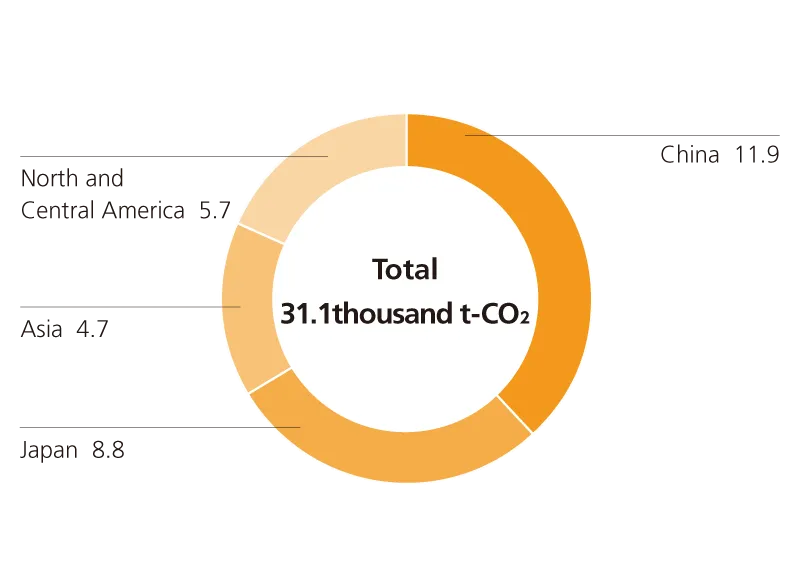
- Note: Data cover CO2 emissions from electricity use by JFE Shoji and 35 major domestic and overseas subsidiaries (steel-processing companies).