Occupational Health and Safety
Initiatives
To ensure safety at its operating companies, the JFE Group regularly reports to the Board of Directors, which provides direction and supervision. It also holds discussions on health and safety with the labor union through the Occupational Health and Safety Committee.
To achieve our goal of zero workplace fatalities under the Seventh Medium-Term Business Plan, the JFE Group particularly prioritizes safety investments (around 10 billion yen per year Group-wide) to reduce risks by making workplaces inherently safe. We will also promote multifaceted occupational employee health and safety activities, including detection and monitoring, by harnessing advanced IT solutions.
The JFE Group also organizes seminars for newly appointed managers and supervisors to provide information on the Industrial Safety and Health Act and risk assessment regulations and on formulating work plans and policies for health and safety management. In the construction operations department, we offer programs for local superintendents in charge of construction work (Overall Safety and Health Controller) centered on the Industrial Safety and Health Act as well as related regulations for subcontractors and the Construction Business Act (400 participants in 2023). We also conduct new employee training and position-specific training on mental health (1,600 participants in 2023).
ST Occupational Health and Safety Initiatives Based on Two Strategies
In 2024, we are following two basic strategies: practicing autonomous safety activities while strengthening communication between employees and business associates and taking action based on the Group’s Health Declaration. In accordance with our goal of achieving zero accidents Group-wide and zero accidents at each workplace, management supervisors make a point to visit work sites every day, while workers are striving to handle their tasks with discipline. We are also proactively applying IT, such as by introducing safety monitoring systems* for safety management.
In order to more independently and systematically promote occupational health and safety management throughout the organization, we established an occupational health and safety management system in accordance with the ISO 45001 international standard and obtained ISO 45001 certification (JIS Q 45001) for all our construction and operating sites. We will continue making workplaces safer and healthier through an ongoing and effective operation of the occupational health and safety management system.
Management Structure for Health and Safety
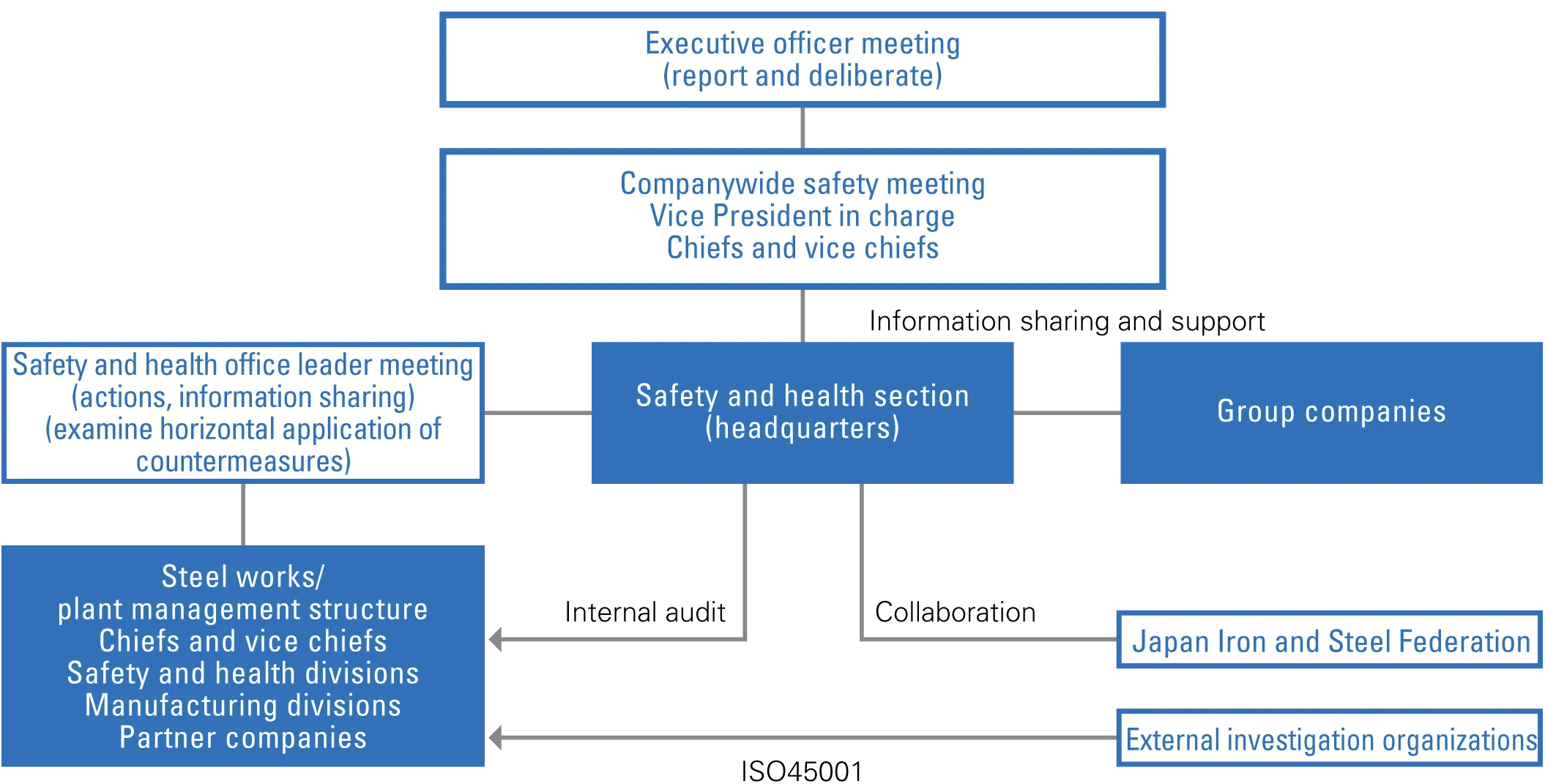
Certified Sites
- Chita Works (September 9, 2021)
- Fukuyama Area (December 16, 2021)
- Chiba Area (May 26, 2022)
- Kurashiki Area (May 26, 2022)
- Sendai Works (December 15, 2022)
- Keihin Area (January 19, 2023)
To mitigate or prevent disaster risks, JFE Steel conducts risk assessments at the planning stage for new facilities as well as prior to periodic and as-needed repairs. We also constantly strive to make each facility inherently safe so as to lower the risk level for our workers.
In the event of an industrial accident, the department in which the incident occurred investigates the cause and formulates and implements actions to prevent recurrence. At the same time, we inform the relevant departments and labor union through the Occupational Safety and Health Committee. We will also set up a disaster investigation committee as necessary and forward recommendations to the department where the accident occurred as well as related departments so that they can develop appropriate measures to prevent recurrence. In the event of severe accidents, a response is deployed across the company, and a standard progress report is submitted to Corporate Officer Council until countermeasures have been completed. In the event of other incidents and near-misses, the health and safety departments discuss and determine the need to deploy a company-wide response and follow up on progress until the company-wide deployment is completed. This practice has been standardized across the entire company.
We immediately report industrial accidents to the Japan Iron and Steel Federation (JISF) under the required guidelines. We file an update once we have determined the cause and decide on countermeasures. In the event of severe accidents, we promptly submit a report on safety, disaster prevention and environmental issues to the Ministry of Economy, Trade and Industry, the Ministry of Health, Labor and Welfare, and the JISF.
- * A system that provides managers with real-time information about, for example, carbon monoxide concentration and oxygen concentration along with worker locations.
EN Ensuring Employee Health and Improving Occupational Health Level
Management Structure for Health and Safety
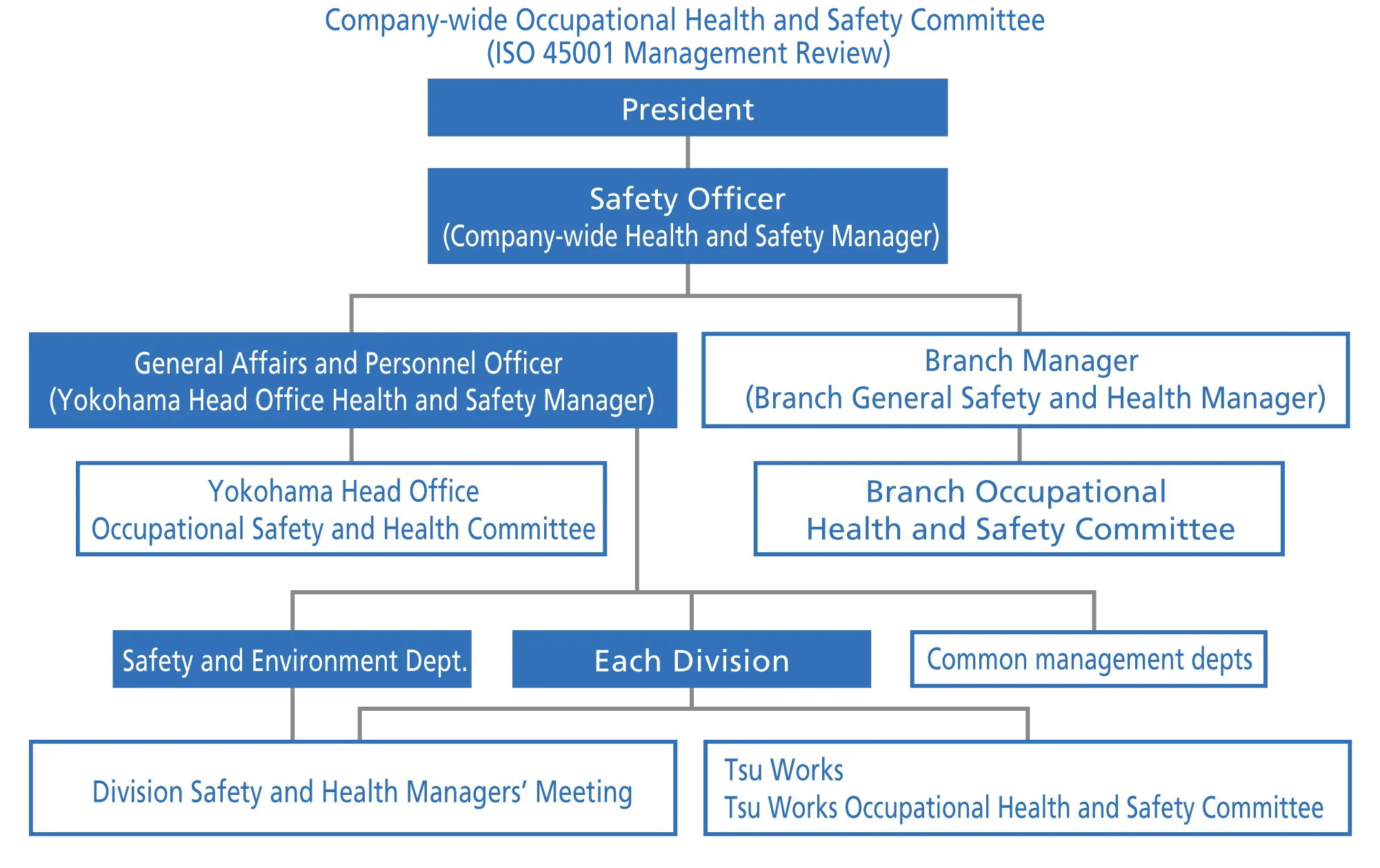
In addition to setting up governance organizations for health and safety at each operating site to comply with the Industrial Safety and Health Act and in line with the type of work and number of employees, JFE Engineering has established a governance structure for health and safety at each operational headquarters to facilitate and effectively implement company-wide management at its construction and operating sites and manufacturing plants. JFE Engineering strives to eliminate disasters at all suppliers and Group companies by establishing priority items to be shared across the company and to which all employees and all staff at suppliers adhere. It also endeavors to identify sources of danger as well as safety measures through risk assessments aligned with the particular characteristics of each individual operational headquarters. Meanwhile, it promotes physical and mental health and the creation of comfortable working environments as a means of ensuring the health of employees and bringing occupational health to an overall higher level.
In the event that an industrial accident occurs, occupational health and safety managers will meet to determine the cause and consider countermeasures that will be deployed across the company. Since 2016, the company has been operating an occupational health and safety management system (ISO 45001 certified) for its construction activities in Japan and overseas as well as its manufacturing operations at the Tsu Works. As a new initiative, JFE Engineering applies IT solutions promoting occupational health and safety, including monitoring and detection by multiple approaches.
SH Enhanced Health and Safety Activities and Establishing a Safe and Secure Working Environment
JFE Shoji is implementing the following activities to eliminate unsafe operations that could lead to severe accidents for achieving zero severe accidents at its coil centers and other processing sites.
- Risk assessment by supervisors patrolling the site and identifying unsafe operations using the recording functions of safety cameras, or by ensuring that each worker is engaged in hazard prediction.
- Comparative study of similar disaster cases and hazard experience training for improving the ability to recognize and avoid unsafe operations
- Facility improvement for reducing risks, including installation of safety sensors
- Operation training (slinging for cranes and other skills) and review of operational standards
Furthermore, for each of its Group companies, JFE Shoji assigns a safety manager to spearhead these efforts to raise the level of health and safety activities. To ensure that all JFE Shoji Group companies operate under the same values, safety managers meet every other month to share knowledge and information on occupational health and safety.
All lost-work injuries must be reported to the top management from the president of each Group company as part of the JFE Shoji Group-wide effort to address safety management. Annual safety awards are also presented to encourage employees to actively engage in health and safety activities. Through these initiatives, the company will raise the level of safety management within the JFE Shoji Group and continue to maintain safe working environments.
Health and Productivity Management
Company-wide Targets for Each Operating Company
We are working on health and productivity management by setting Company-wide goals for each of our operating companies, in addition to KPIs common to the JFE Group.
Items | Indicators | FY2023 Results | FY2024 Targets | |
---|---|---|---|---|
JFE Steel | Thorough implementation of physical examinations Preventive health measures | Rate of complete exams for dependents | 55.2% | Rate of complete exams for dependents: 60% |
Rate of providing specific health guidance | -*2 | Rate of providing specific health guidance: at least 60% | ||
Preventive health measures Promotion of non-smoking and segregates smoking | Rate of obesity*2 (BMI: 25 or higher) | 30.7% | Rate of obesity (BMI: 25 or higher): 30% or less | |
Smoking rate*2 | 25.8% | Smoking rate: 24.3% (1.5% annual reduction) | ||
Measures related to sleep | Sleep-related risk (based on responses in health checkup questionnaire) | 36.7% | Sleep-related risk (based on responses in health checkup questionnaire): 35% or lower | |
JFE Engineering | Measures related to sleep | Sleep-related risk (based on responses in health checkup questionnaire) | 36.7% | 35% or lower |
Measures related to passive smoking | Smoking rate | 21.8% | 20.8% or lower (1% annual reduction) | |
Measures related to obesity | Obesity rate (BMI: at least 25 or abdominal circumference ≧85/≧90 for male/female) | 41.7% | 38.3% or lower | |
Collaborated health promotion | Rate of providing specific health guidance | -*2 | At least 50.0% | |
Rate of complete exams for dependents | 54.4%*1 | 60% | ||
JFE Shoji | Preventive health measures | Rate of providing specific health guidance | -*2 | 60% |
Measures for non-smoking and passive smoking | Smoking rate | 20.6% | 20.0% |
- *1Preliminary figures
- *2Actual rates of providing specific health guidance will be added as soon as they are confirmed.
- *JFE Steel manages the obesity rate and smoking rate on a calendar year basis.
Physical Health Initiatives
Changes in Smoking Rates (All Operating Companies)
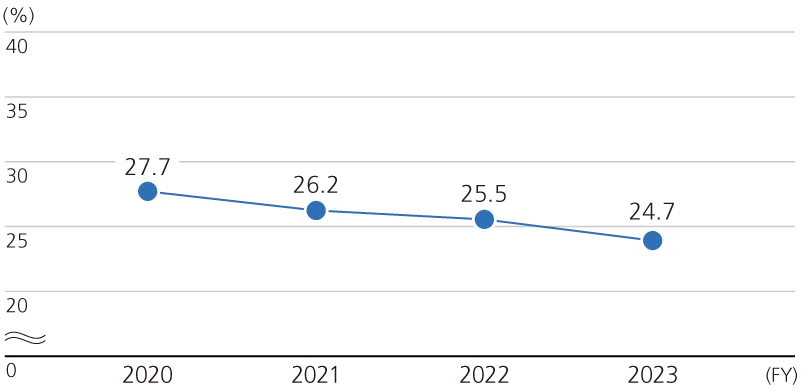
- Ensure the implementation of regular physical examinations and strengthen cancer screenings.
- Prevent aggravation of lifestyle diseases by conducting metabolic syndrome checkups and offering health guidance.
- Utilize the health insurance union’s health promotion app, PepUp, to educate employees on physical exercise and other healthy habits.
- Promote non-smoking areas and maintain separate areas for smokers and non-smokers in buildings. Provide guidance to help employees quit smoking through industrial physicians and public health nurses.
Maintaining and Promoting the Health of Employees’ Families
The JFE Group works with the health insurance union to maintain and improve the health of employees and their families by, for example, encouraging spouses to undergo health examinations. The rate of health examinations for dependents (age 40 or older) has been steadily increasing to 53.8% in FY2023, up 16.2 points from 37.6% in FY2014.
For employee health data, please refer to the following.
Mental Healthcare
The JFE Group conducts four basic initiatives to maintain the mental health of employees: “self-care” for workers who strive to remain aware of stress and take preventive measures; “care by management supervisors” who provide advice to subordinates; “care by industrial health staff” who support employees, managers and supervisors; and “care by human resources outside workplaces,” including specialist clinics and individuals.
JFE’s health insurance union also provides mental health counseling, including a 24-hour hotline for employees and their families (spouse and dependents).
Initiatives on Health Issues
We operate a health management system for continuously and effectively managing the health of all employees, including those on overseas assignments and business trips and those studying abroad.
We particularly seek to ensure that employees working abroad, under healthcare systems that differ from those in Japan, can maintain a healthy lifestyle, along with their accompanying family members, by conducting health checkups and vaccinations before they move overseas, in accordance with Company-wide regulations. In a proactive effort to prevent infections, we also provide information on global health issues such as COVID-19, HIV, tuberculosis, and malaria during assignment briefings. We will continue to monitor and appropriately respond to global health issues.
ST Promoting Health and Productivity Management to Maintain and Improve Health
To drive key initiatives for maintaining and improving the health of employees and their families, JFE Steel launched the Health and Productivity Management Promotion WG upon the establishment of its Group Health Declaration in 2016 and is monitoring the achievement of medium- to long-term goals. Through these ongoing activities, we want all employees to work healthily and vigorously and to establish a health culture in which every employee practices activities on their own initiative to maintain and improve their health.
In 2016, the Health and Productivity Management Promotion WG first focused on physical health established key initiatives regarding: (1) thorough implementation and reinforcement of physical examinations, (2) preventive health measures, (3) establishment of sound exercise and health habits, and (4) non-smoking and segregated smoking activities. Since 2024, we have been implementing activities with all of our operating sites.
Structure of Health and Productivity Management Promotion WG
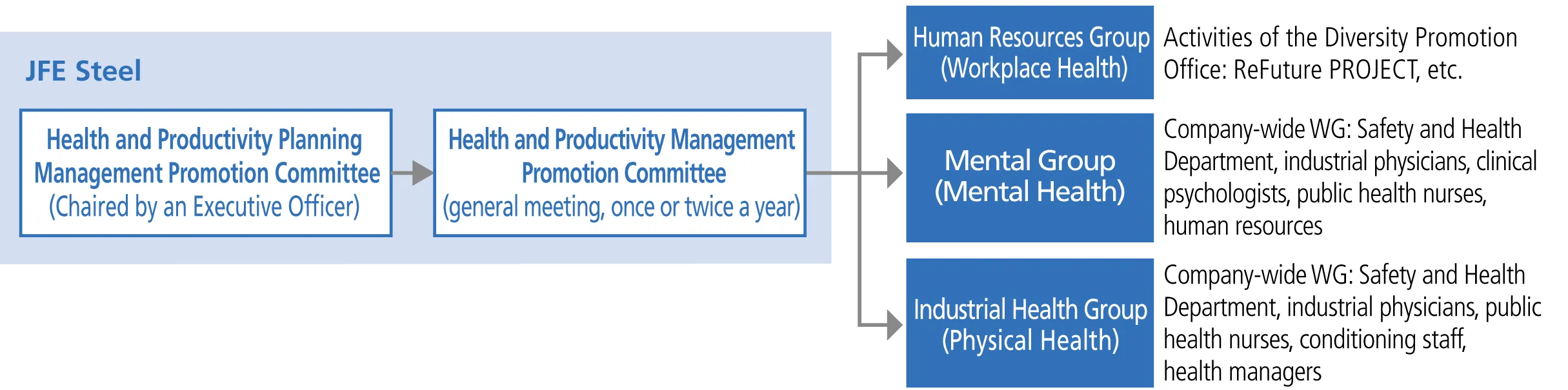
Health and Productivity Management Promotion WG
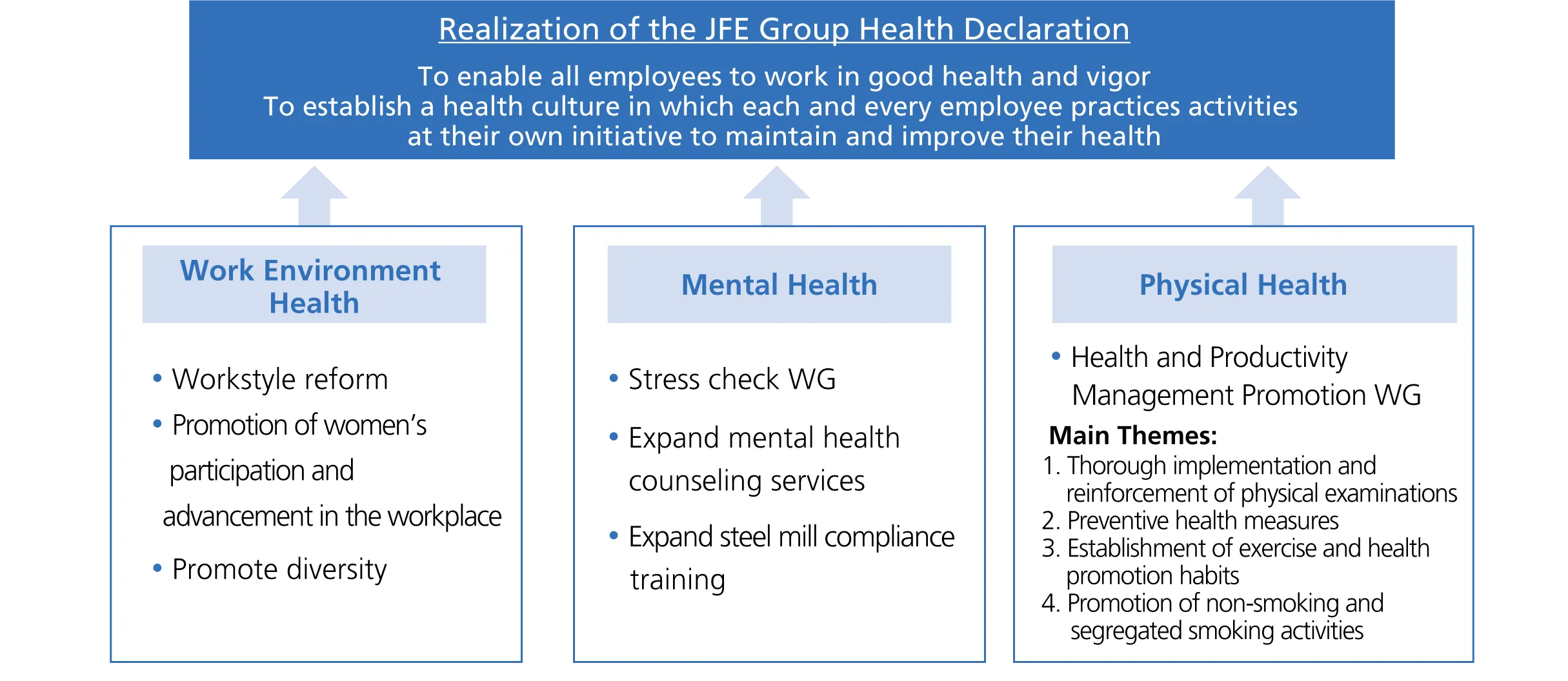
Health and Productivity Management Promotion WG
Members |
|
|
---|---|---|
|
|
|
Discussion topics |
Evaluation of indices and activities:
|
|
Frequency |
|
ST Active Exercise™ Health
JFE Steel business sites offer the Active Exercise™ program, designed by West Japan Works to help people increase their physical strength and prevent injuries from falling. The program’s effectiveness in preventing occupational accidents and improving health has even attracted attention outside the company, so it is being actively shared not only among Group companies but also with on-site suppliers and companies across a broad range of industries. To prevent accidents such as falls and back injury, we participate in the Ministry of Health, Labor and Welfare and the SAFE Consortium as well as activities such as Active Exercise™ and Safe Physical Fitness™ Functional Tests.
EN Engineering Activities for Boosting Health Based on Health Checkup Data
JFE Engineering maintains a system centered on the Health Management Center of the Human Resources Department, under which industrial health staff at each office and branch office cooperate to promote activities. The company is pursuing initiatives for improving health focused on five domains, including sleep, smoking and obesity issues extracted from past health checkup data, along with cancer and mental health. Every year, the Health Management Center compiles basic health checkup data and prepares the Data Book, which shows changes over time at a glance for the entire Company and major business sites. The center follows the PDCA cycle while reviewing the results of its initiatives.
Health and Productivity Management Promotion System
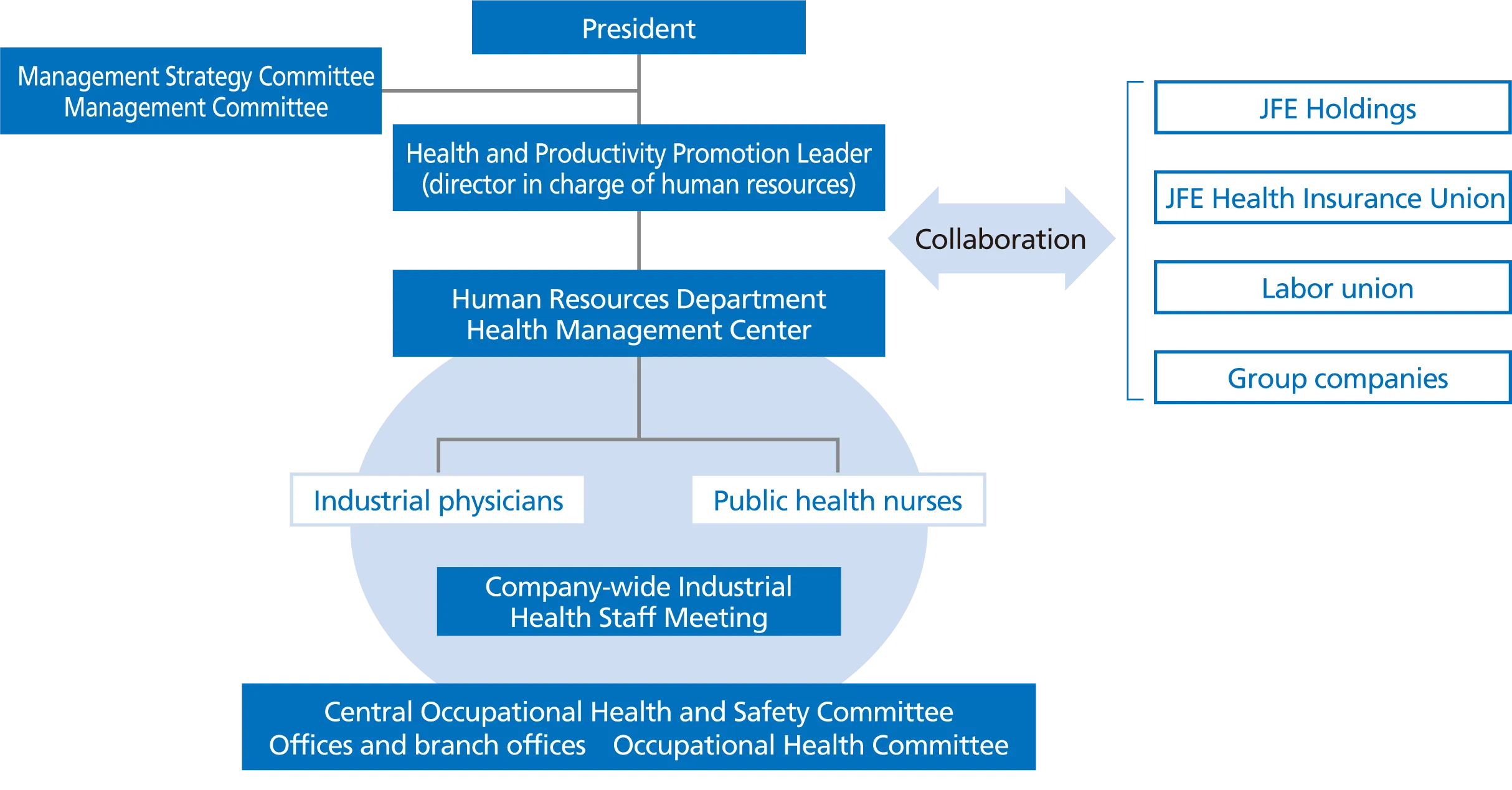
Initiatives Based on Past Health Checkup Data
Fiscal Year Launched | Purpose | Initiatives |
---|---|---|
2018 | Preventing cancer | Stomach endoscopy during regular health checkups |
2019 | Improving sleep habits | Company-wide self-care seminars to practice napping and breathing exercises |
2020 | Addressing obesity | Labor and management co-sponsored RIZAP seminars and workplace exercises at home |
2021 | Ending exposure to passive smoking | Complete ban on indoor smoking |
Improving sleep habits | Company-wide self-care seminars to practice sleeping and breathing exercises | |
2022 | Providing more personalized guidance | Provision of more individualized guidance on sleep, obesity, smoking, etc. |
2023 | Preventing cancer | Colonoscopy subsidy system introduced, charity walk held |
SH Detecting Illnesses at an Early Stage, Maintaining and Promoting Health for Employees and their Families
JFE Shoji believes that the health of employees and their families holds the key to the further development of the company and is therefore creating workplace environments in which employees can work with vigor.
Health and Productivity Management Promotion System
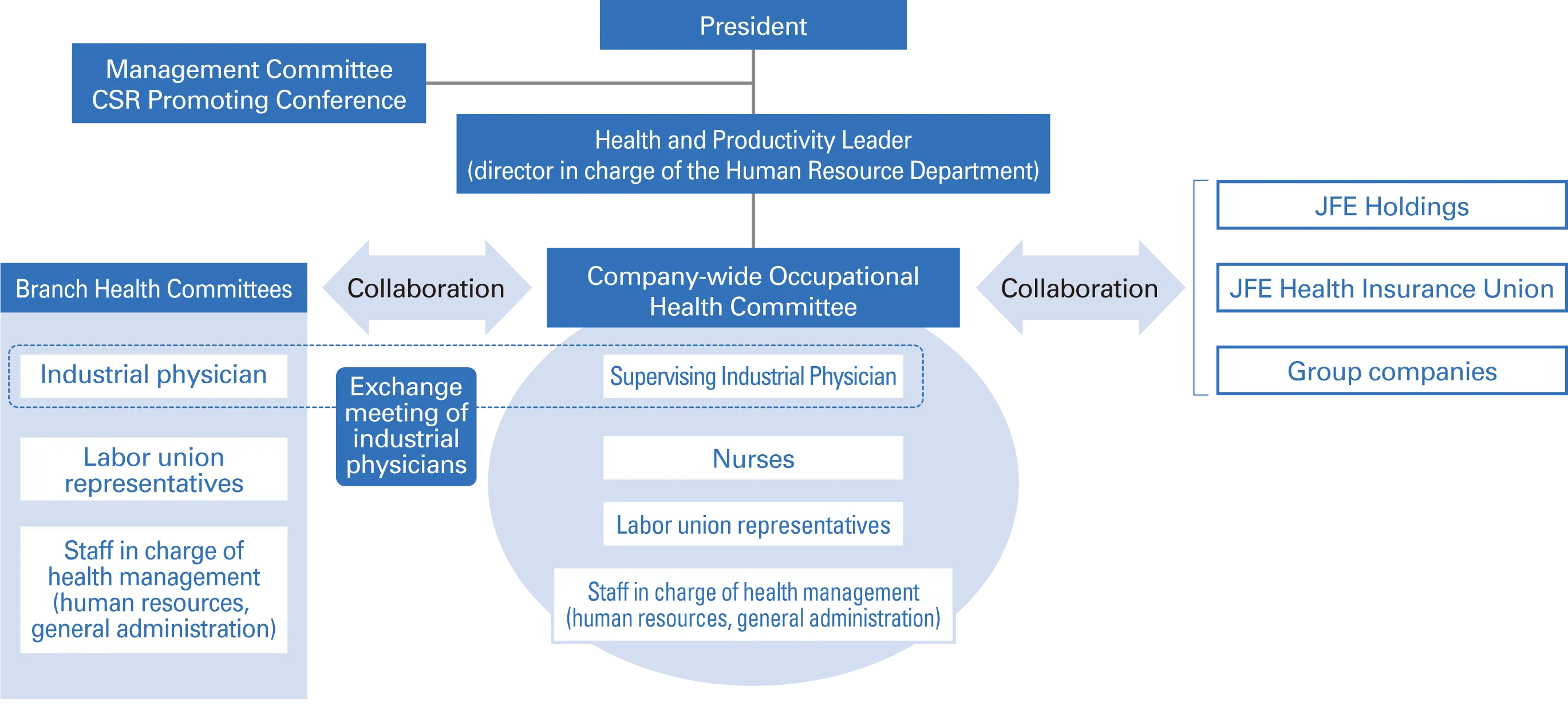
Past Initiatives
Fiscal Year Launched | Purpose | Initiatives |
---|---|---|
2018 | Prevent cancer | Helicobacter pylori tests conducted during regular health checkups |
New program for subsidizing examination fees for breast cancer and uterine cancer | ||
Raise employee health awareness | e-learning program based on the importance of regular health checkups, and reducing heart and brain disease | |
2019 | Prevent lung cancer and stroke | New program for subsidizing smoking cessation clinic fees |
Measures related to passive smoke (reduction in smoking rate) | ||
2020 | Encouraging employees to exercise as a habit | Encourage participation in the Powering Up Health Care program |
2022 | Providing more individualized guidance | Encourage individual consultation to those eligible for specific health guidance |
2023 | Early detection of stomach cancer | Gastrointestinal endoscopy tests conducted during regular health checkups |
Response to the COVID-19 Pandemic
The JFE Group recognizes the importance of social infrastructure that manufactures and supplies the necessary goods for society. It has therefore been formulating a BCP that includes setting response policies for the phase of a new influenza epidemic. In response to the COVID-19 pandemic since 2020, it fully understands the purpose and content of the government’s basic policy to respond to COVID-19. We place the highest priority on employee health and have taken action from the perspective of the basic approach to preventing infection and specific measures to be taken as outlined in the guidelines issued by the Japan Business Federation. While taking into account the conditions of factories and other factors, we have worked to prevent the transmission of COVID-19 and have continued to fulfill our role as a social infrastructure, including providing vaccinations at workplaces.
Since COVID-19 was reclassified as Class 5 in May 2023, we have been responding in accordance with government guidelines, and every Group company has returned to normal working rules. Nevertheless, all employees are encouraged to take basic infection prevention measures, such as washing hands and gargling. As mutant strains or new infections occur in the future, we will use all of our experience in responding to COVID-19 while acting in accordance with prevailing government policy.