Development and Provision of Eco-Friendly Processes and Products
Basic Policy
In accordance with its corporate philosophy of contributing to society with the world’s most innovative technology, the JFE Group develops and provides processes and products for addressing climate change and reducing environmental impact. In the JFE Group Environmental Vision for 2050, we announced our initiatives for reducing the CO2 emissions of the Group and expanding our contribution to reducing CO2 emissions in society as a whole. Apart from these initiatives, we also strive to enhance our corporate value and play our part in realizing a sustainable society through the development and provision of various processes and products related to preserving the global environment.
In the steel business, the Steel Research Laboratory is engaged in research and development under the Environmental Management System (environmental strategies) to create a recycling-oriented society capable of sustainable development by providing the world’s best technologies and sparking innovation. In the engineering business, the Research Center of Engineering Innovation conducts research and development of new technologies to support the society of the future, including the creation of next-generation energy and solutions to environmental problems.
For further details on the JFE Group Environmental Vision for 2050, refer to the following resources.
- The JFE Group Environmental Vision for 2050
- The JFE Group Environmental Vision for 2050, presentation material on May 25, 2021
Initiatives
Each operating company of the JFE Group leverages its respective strengths to develop and provide a variety of eco-friendly products and technologies.
- Eco-Friendly Processes, Products, and Technologies in FY2023
- Eco-friendly Processes, Products, and Technologies that Were Upgraded
- Major Eco-Friendly Processes, Products, and Technologies in the Past
Eco-Friendly Processes, Products, and Technologies in FY2023
ST Development of High-Efficiency Autonomous Cleaning Robot “GAZMASTER™-S”—Reduced Work Burden and Improved Safety and Productivity
- Environmental Benefit
- Environmental conservation
- Status
- Development stage
Steelmaking uses facilities for handling iron ore, coal, and other raw materials, and they are usually cleaned by workers. To meet the strong demand automation, JFE Steel developed “GAZMASTER™-S”*, a high-efficiency, autonomous cleaning robot that can clean the floors of these facilities containing piles of raw materials in lumps and powder forms. The robot is now being used by the West Japan Works (Fukuyama District) (Photo 1).
GAZMASTER™-S gets the job done even in narrow spaces and on stepped surfaces, requiring only a simple replacement of accessories depending on the space to be cleaned (Photo 2). This robot estimates its progress in cleaning a room by comparing its learned occupancy map with real-time information it obtains from its laser range scanner (Figure 1). It is capable of preventing its wheels from getting stuck and coping with low battery levels, and these functions and status conditions can be monitored and controlled using a tablet. Durability has already been assured through tests conducted at the steel manufacturing plant in Fukuyama. JFE Steel plans to deploy GAZMASTER™-S at its other steelworks across the country to ease the burden of labor, improve safety and performance, and keep the workplaces cleaner and more pleasant.
With the launch of the JFE Digital Transformation Center (JDXC™), JFE Steel is promoting DX, including the implementation of a cyber-physical system (CPS) for manufacturing as an innovation in productivity and a means for addressing resolve safety and related issues associated with manufacturing operations, ultimately contributing to a sustainable future.
- *GAZMASTAR: Coined from “Gather (dust)” and “Master”.
Photo 1:High-efficiency, autonomous GAZMASTAR-S™ robot
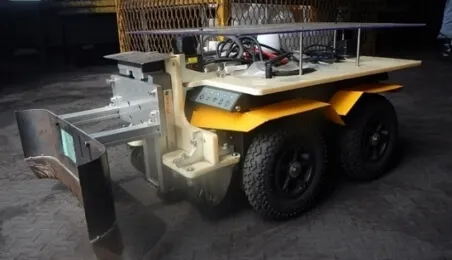
Photo 2:Before and after cleaning
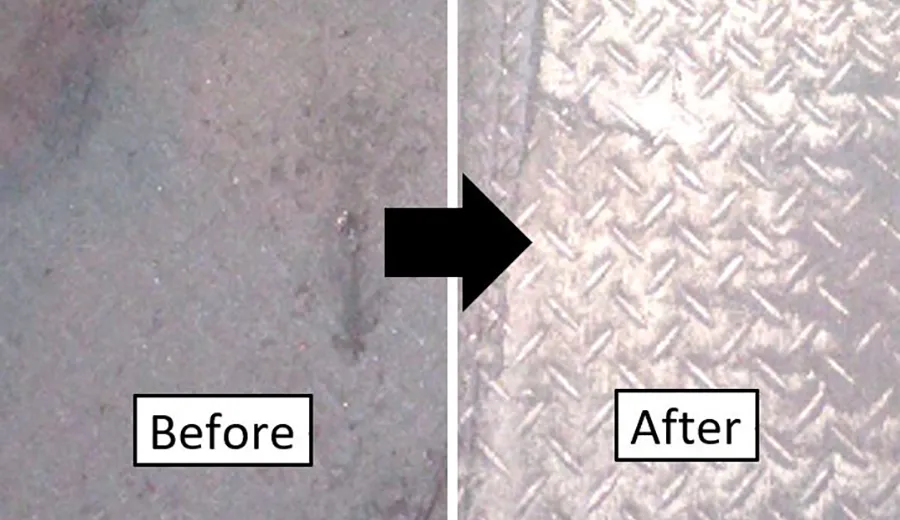
Figure 1:How robot calculates its position
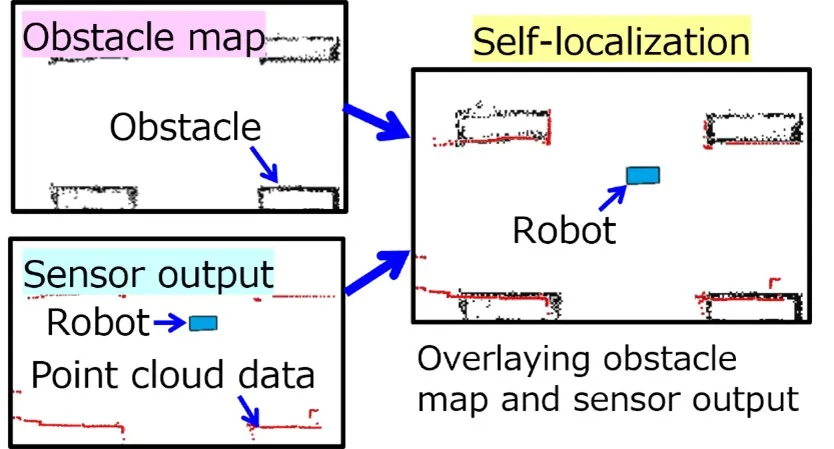
ST Receiving the 70th (FY2023) Okochi Memorial Technology Award for the Automation of Blast Furnace Operations through the Use of a Cyber-Physical System
- Environmental Benefit
- Reduce CO2 emissions
- Status
- Development stage
JFE Steel’s data science technology progress toward establishing a cyber-physical system in furnace operations was awarded the 70th (FY2023) Okochi Memorial Technology Award, a prize granted for a unique accomplishment in the fields of industrial engineering and production engineering that significantly contributes to academic progress and industrial advancement.
Reducing CO2 emissions from steelmaking requires increasing the efficiency and stability of blast furnace operations. While blast furnaces have high thermal efficiency, they must be handled by highly skilled operators with special knowledge and experience due to the difficulty of estimating internal conditions that are vulnerable to significant variances in the properties of raw materials and other factors. Furthermore, recently rising demand to reduce CO2 emissions is increasing the urgency of realizing furnace operations that can be controlled more precisely and reliably than conventional ones.
JFE Steel developed a cyber-physical system that controls and optimizes hot metal temperatures and ventilation inside a blast furnace in real time. The system uses a unique model based on real-time sensor data collected from a blast furnace and estimates hot metal temperatures up to 12 hours in advance while also controlling ventilation using an anomaly detection technology. The system is already in use at JFE Steel’s furnace operations, helping the company to boost labor productivity and reduce CO2 emissions. JFE Steel plans to implement the system across its entire steelmaking operations as a productivity innovation and to increase operational safety.
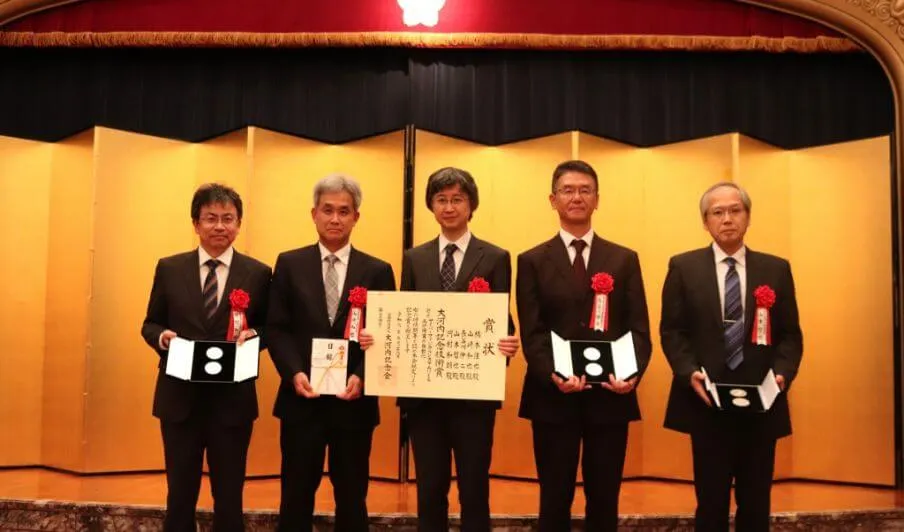
Cyber Physical System of Blast Furnace
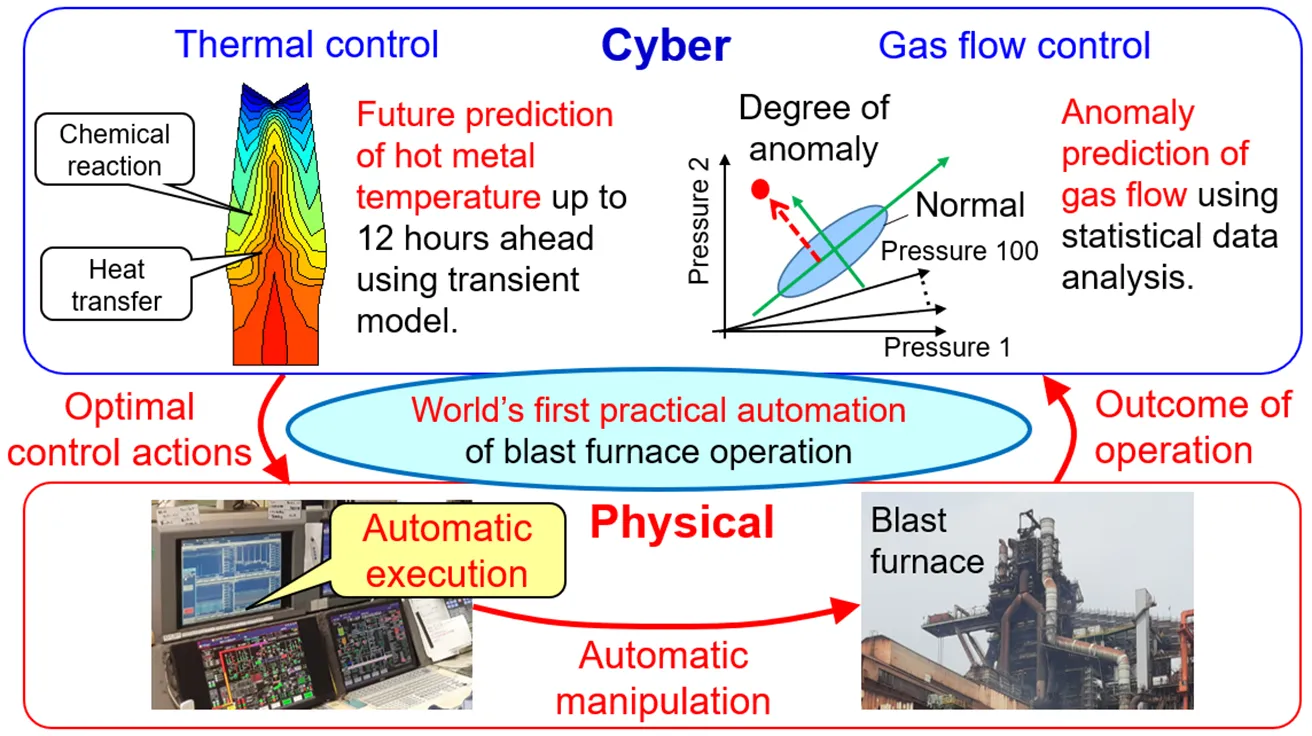
ST Verification of the Feasibility of Making Motors 48% Thinner Using Insulated Pure-Iron Powder Denjiro™
- Environmental Benefit
- Recycle resources and reduce CO2 emissions
- Status
- Commercialized
In a project with JFE Techno-Research Corporation and a venture company launched by Shizuoka University and named ARMIS CORPORATION, JFE Steel designed and prototyped a motor using Denjiro™, the company’s insulated pure-iron powder. The demonstration, also conducted by the three, established the feasibility of making motors 48% thinner and 40% lighter than existing ones while maintaining the same level of horsepower by using this powder.
Demand continues to rise for smaller but higher-performing electric motors for industrial equipment and vehicles. Axial-gap motors, which are thinner than general radial-gap motors, can deliver high power (Figure 1). Unlike radial-gap motors, however, axial-gap motors pose a significant manufacturing challenge by requiring a three-dimensional magnetic core that cannot be made by laminating electrical steel sheets. Meanwhile, a powder magnetic core made by pressure-forming insulated magnetic powder exhibits a magnetic property that is three-dimensionally uniform and can withstand complex shapes. Denjiro™ is an insulated pure-iron powder product developed and marketed by JFE Steel. The aforementioned three parties designed and prototyped an axial-gap motor using a powder magnetic core made from Denjiro™ and tested the motor’s performance (Figure 2). The test results showed that motors can be 48% thinner in height and 40% lighter compared to existing units while maintaining the same or higher level of performance (table and Figure 3). In response to these test results, JFE Steel and JFE Techno-Research Corporation launched a new service to support customers with the design of motor parts with a powder magnetic core. At the same time, the companies are now shipping samples of large green compacts for cutting and machining soft magnetic composite cores, as well as prototype soft magnetic composite cores that conform to specific designs.
In addition to developing products to meet customer demand, JFE Steel is going to increase its eco-friendly product lines to assist customers with reducing CO2 emissions while also promoting technological exchanges with customers, including consultation on the use of technologies and support for prototype production and testing, under the goal of contributing to a sustainable future.
Figure 1: Types of motors
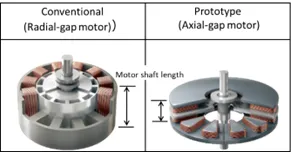
Figure 2: From powder to prototypes
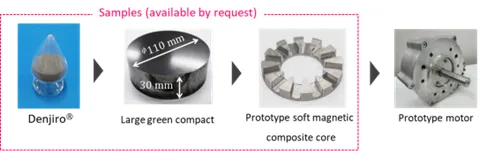
Conventional vs. prototype motor (test results)
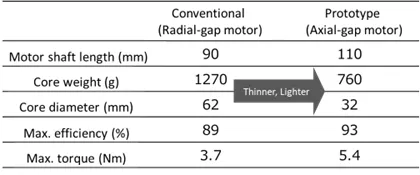
Figure 3: Efficiency of conventional vs. prototype motor
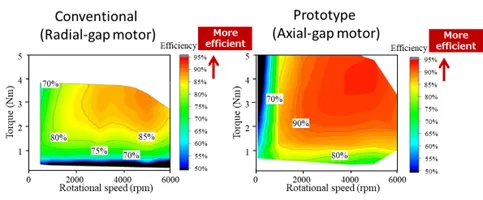
ST Introduction of a Test Facility to Develop a Steel Product for Liquid Ammonia Tank Containers
- Environmental Benefit
- Recycle resources and reduce CO2 emissions
- Status
- Development stage
JFE Steel started operating a test facility at the Steel Research Laboratory (Kurashiki District) at the end of October 2023, to evaluate the risk of stress corrosion cracking in steel products that can occur when exposed to liquid ammonia.
Amid growing worldwide initiatives for a decarbonized society, ammonia is expected to serve as an alternative fuel for thermal power generation and shipping, further increasing the importance of establishing supply chains for liquid ammonia, and the demand is rising for high strength steel required for the manufacture of larger liquid ammonia storage tanks.
Liquid ammonia carries the risk of causing stress corrosion cracking (SCC*) in steel. Generally, higher strength carbon steel is more vulnerable to SCC when exposed to liquid ammonia. Therefore, the risk needs to be properly evaluated during the development of a high-strength steel sheet product. Since liquid ammonia is a toxic and combustible liquefied gas, JFE Steel constructed a new building (Photo 1) for housing the test facility (Figure 1) in accordance with the High Pressure Gas Safety Act, enabling the Steel Research Laboratory to perform electrical and chemical measurements in the building, in addition to evaluating the durability of raw materials against SCC through the use of test pieces soaked in the gas (Figure 2).
JFE Steel plans to make good use of this test facility to both propel the development of steel for ammonia tanks and proactively respond to other social needs, including the standardization of test methods and raw materials. The company will thereby support efforts for increasing green energy sources for a decarbonized society.
- *Stress Corrosion Cracking: Occurs when metal materials are under tensile pressure and exposed to a corrosive environment.
Photo 1: Example of stress corrosion cracking that occurred during test.
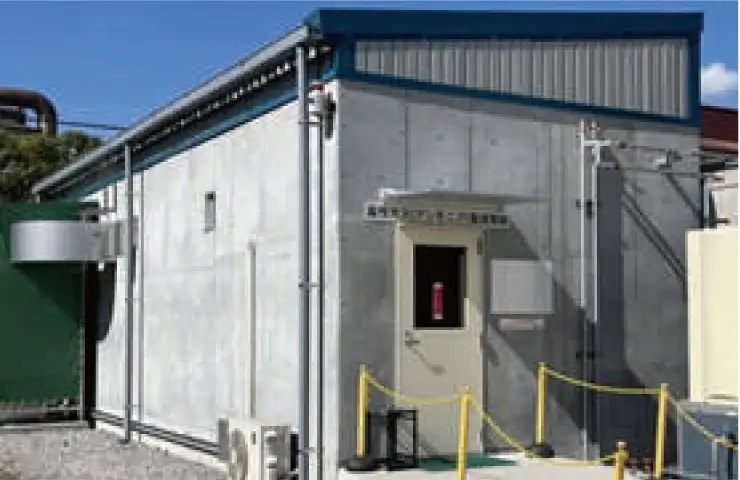
Figure 1: Building for testing stress corrosion cracking that occurs in liquid ammonia.
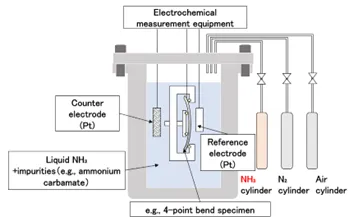
Figure 2: Overview of test equipment
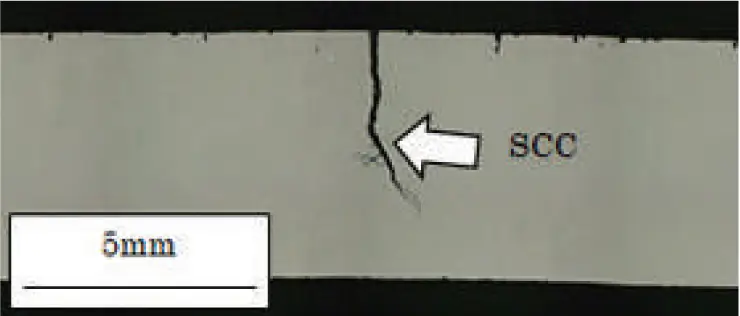
ST Receiving the National Commendation for Invention for an Anti-Weatherability Steel Product that Does Not Require a Paint Finish Even Under Coastal Environmental Conditions
- Environmental Benefit
- Recycle resources and reduce CO2 emissions
- Status
- Development stage
JFE Steel received the FY2024 National Commendation for Invention*1 for developing an anti-weatherability steel product that does not require a paint finish even for use in coastal settings. In addition to outstanding cost-performance, this product has weatherability nearly as high as the company’s anti-weatherability nickel steel, which is popular as a material for bridges in high-salinity environments. The newly developed steel technology was applied to LALAC™-HS*2, an all-weather steel sheet product designed for use in high-salinity environments. LALAC™-HS already boasts a record of being selected as a material for five bridges in and outside Japan.
The company’s anti-weatherability nickel steel is made with 1–3% additional nickel to achieve the prominent all-weather property, which has however made the product rather expensive. Instead of nickel, this award-winning invention adds a combination of tin and niobium. These elements thicken locally in the bottom layer of rust and form fine rust just as the anti-weatherability nickel steel would do, thereby controlling the permeation of chloride ions, which accelerates corrosion, into the steel (Figure 1). The anti-weather property of tin and niobium performs well even in small amounts thanks to their local thickening and allows a significantly reduced use of nickel, making this invention more affordable than anti-weatherability nickel steel, while exhibiting nearly the same level of weatherability (Figure 2). This newly-developed steel product with high weatherability and outstanding cost performance is expected to significantly reduce life cycle costs for structures by eliminating the need for painting or repainting.
JFE Steel intends to further expand the applications for this new product and develop other steel products with high functionality and quality, thereby increasing the safety and durability of steel bridges and contributing to a sustainable future.
- *1Sponsored by the Japan Institute of Invention and Innovation (Chairman: Takeshi Uchiyamada). This commendation, which is intended to encourage the advance of science and technology in Japan and support the nation’s industrial development, is given to an invention, idea, or design that has delivered or is expected to deliver significant benefits due to its excellence.
- *2LALAC™-HS: Abbreviation for Low Alloyed & Low Atmospheric Corrosion Steel – High Salinity.
Figure 1: Pattern Diagram Showing the Distribution of Elements in Rust Layers
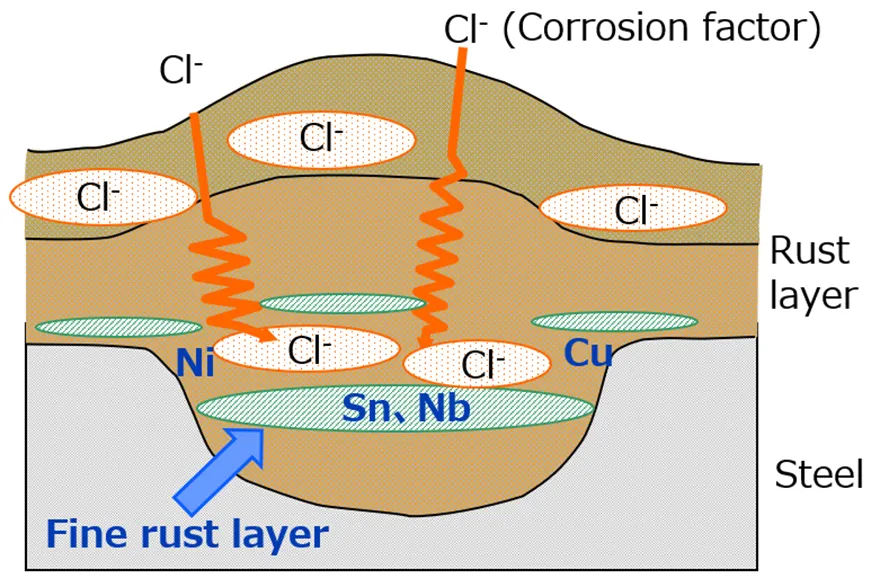
Figure 2: Exposure Test in Real-Life Environments
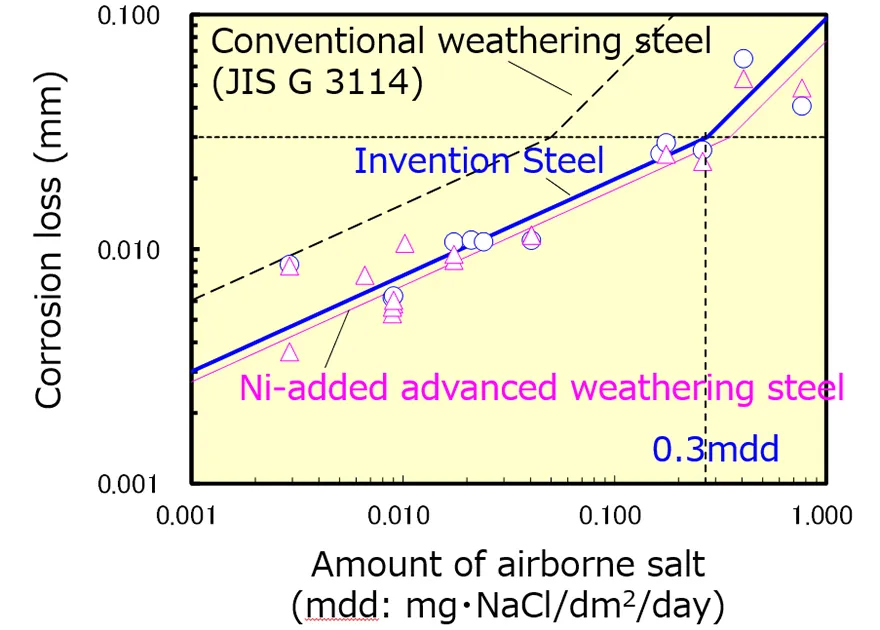
ST Receiving the FY2023 Ministry of the Environment Commendation for Action for Climate Change for the Development of an Ultra-Hydraulic Hydrogen Accumulator Using Steel and Carbon Fiber-Reinforced Resin Layers in Combination
- Environmental Benefit
- Recycle resources and reduce CO2 emissions
- Status
- Development stage
JFE Steel’s and JFE Container’s joint “Development of Ultra-Hydraulic Hydrogen Accumulator Using Steel and Carbon Fiber-reinforced Resin Layers in Combination” received the FY2023 Ministry of the Environment Commendation for Action for Climate Change in the Development and Productization (the Mitigation domain) category.
Hydrogen is being studied as a source of energy in a number of fields worldwide because it does not emit CO2 during combustion. For example, hydrogen stations represent a key component for popularizing its use as a green fuel for vehicles. The incorporation of a hydrogen accumulator for high-pressure storage enables these stations to essentially serve as stationary, large-capacity reservoirs that can quickly fill hydrogen into a vehicle.
This award-winning hydrogen accumulator was designed and is now manufactured by JFE Container using JFE Steel’s ultra-thick seamless steel pipe with high resistance to hydrogen embrittlement. The Carbon Fiber Reinforced Plastic (CFRP) of Mitsubishi Chemical Group Corporation is also used for the body of the accumulator to support a wide pressure range up to the highest levels in the industry. The accumulator was developed under a project of NEDO (New Energy and Industrial Technology Development Organization) and has been marketed by JFE Steel since FY2019, after having been authorized by the High Pressure Gas Institute of Japan and specially approved by the Minister of Economy, Trade and Industry in FY2018. The product is in use by multiple hydrogen stations around the country and has been recognized for its outstanding performance. It is also used for medium-pressure hydrogen accumulators, high-pressure hydrogen accumulators, and mock containers of the Fukushima Hydrogen Filling Research Center. The research facility was built under another NEDO project and mainly uses hydrogen produced by the adjacent processing facility, Fukushima Hydrogen Energy Research Field (FH2R). It facilitates the development and verification of filling and measurement technologies for large-flow-rate hydrogen for heavy-duty fuel-cell vehicles.
To further popularize the Ultra-Hydraulic Hydrogen Accumulator, JFE Steel is seeking to increase its manufacturing capacity and further developing the product to increase its internal volume, pressure range, and amplitude cycles to meet specifications likely to be requested as hydrogen stations become more popular for filling up fuel cell buses and trucks.
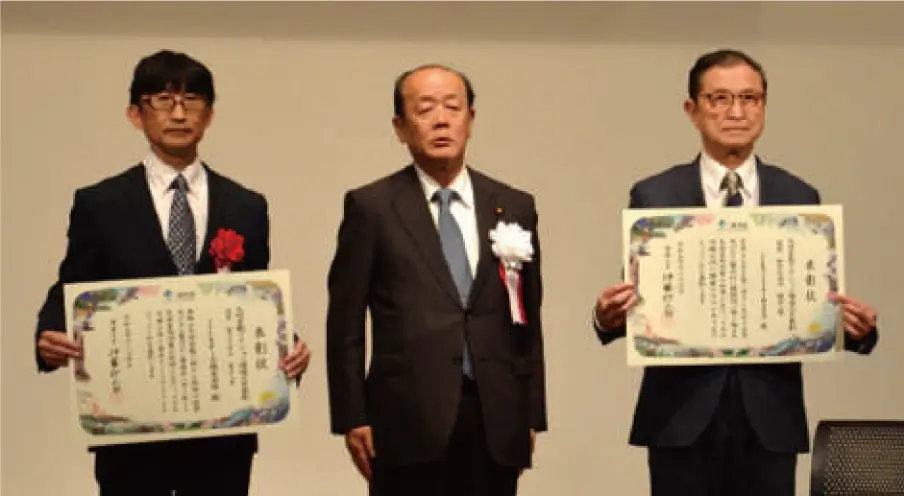
High-pressure hydrogen accumulator
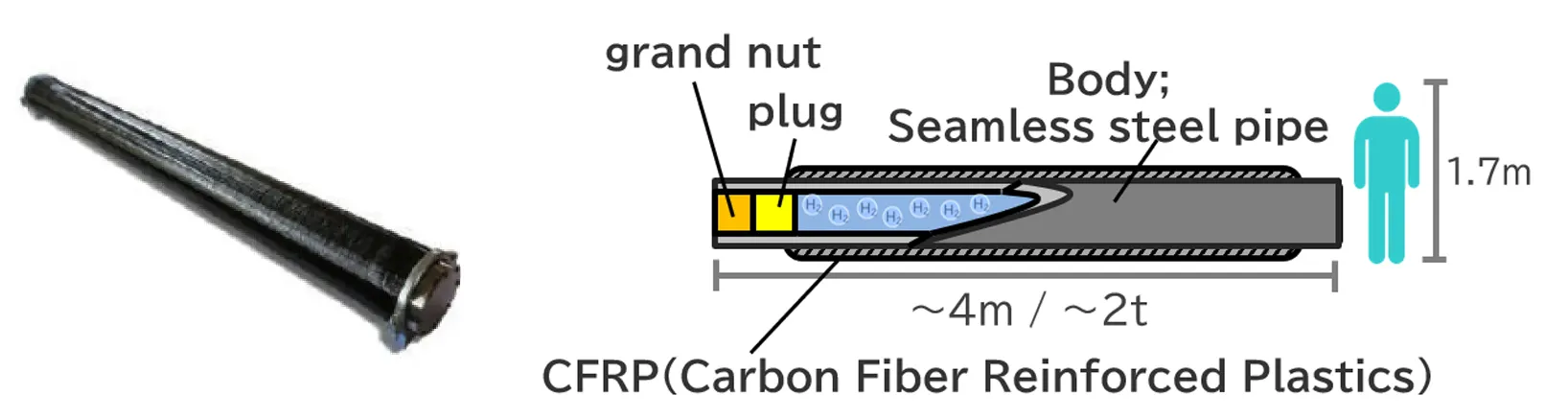
ST The Company’s Proprietary Wall Bending and Restrike Method Selected for Production of Parts Supplied to a Major Japanese Automaker —Development of a Forming Method to Suppress the Springback of Ultra-High Tensile Steel Sheets
- Environmental Benefit
- Reduce CO2 emissions
- Status
- Development stage
Inner rocker made with the Wall Bending and Restrike Method
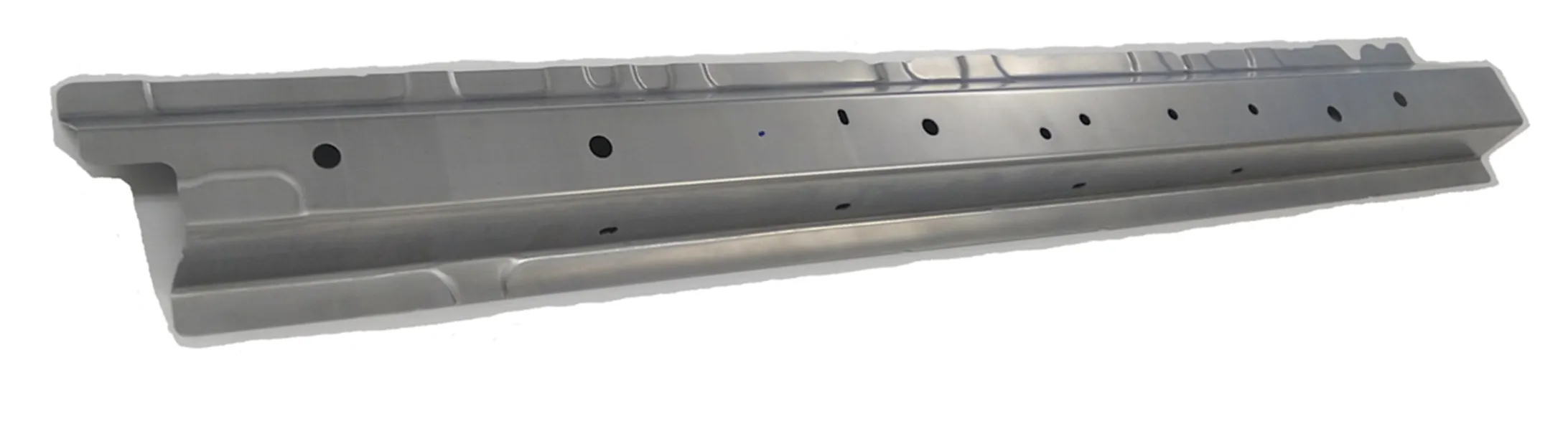
JFE Steel’s Wall Bending and Restrike Method has been adopted and used to produce inner rockers , a body frame component, for use in vehicles manufactured and sold by a major Japanese automaker. The Wall Bending and Restrike Method, a press-forming method, is applied to suppress the springback of 1,180 MPa class, ultra-high tensile steel sheets. JFE Steel has provided customers with these steel sheets to meet increasing demand due to the need for lighter-weight vehicles to reduce CO2 emissions and boosting fuel efficiency. Since pressed steel sheets are subject to springback—that is, returning to their original shape when removed from a mold—springback conditions must be corrected. Press-formed ultra-high tensile steel sheets generate greater stress than ordinary steel sheets and are therefore more susceptible to higher levels of springback. The resulting challenge of controlling deformation from the intended shape and the increased difficulty of bonding with other component parts has been a bottleneck to the wider application of ultra-high tensile steel sheets.
The Wall Bending and Restrike Method provides a solution for reducing springback by applying an offsetting force to springback-induced stress, particularly through the optimization of sheet shape prior to press-forming. The inner rockers, a structural component at the bottom of a vehicle door, for which the Wall Bending and Restrike Method is used, are manufactured by Kyoho Machine Works, Ltd. , and the application of this method to mass-production molds was achieved through a joint development by this company and JFE Steel.
JFE Steel is actively working on what it calls Early Vendor Involvement (EVI), an activity beyond the supply of raw materials, to provide customers with solutions to help them develop new products and increase the performance of existing ones. JFE Steel is developing various steel application technologies to offer comprehensive solutions, including a systematized solution called JESOLVA™, which is short for JFE Excellent Solution for Vehicle Application. JFE Steel strives to broaden the application of its ultra-high tensile steel sheets and help customers boost the performance and trim the weight of their vehicles to contribute to a sustainable future.
ST The Company’s Proprietary Forming Technologies for Ultra-High Tensile Steel Sheets Adopted and Used for the Production of Parts for Suzuki Swift— An Inflow Control Method for Reducing Wrinkles around Pressed Areas and the Stress Reverse Forming™ Method for Reducing Variation in Dimensional Accuracies
- Environmental Benefit
- Reduce CO2 emissions
- Status
- Development stage
JFE Steel’s inflow control method and the Stress Reverse Forming™ Method were adopted and have been used for the production of three front bumper parts for Suzuki Swift to reduce the formation of wrinkles at pressed areas of 980–1,180 MPa class, ultra-high tensile steel sheets and reduce variation in dimensional accuracies.
JFE Steel has provided customers with ultra-high tensile steel sheets to meet rising demand due to the need for lighter weight vehicles to reduce CO2 emissions and raise fuel efficiency. When press-formed into a curvature shape, press wrinkles form on the steel sheets and the sheets tend to springback to their original shape; both conditions need to be corrected.
While contributing to vehicle weight reduction, ultra-high tensile steel sheets are susceptible to press wrinkles, mold damage, and shape variation, and all these issues are more likely to occur with thicker, stronger steel sheets, a factor that has inhibited the wider application of ultra-high tensile steel sheets. JFE Steel’s inflow control method is capable of reducing the formation of press wrinkles, particularly those around the flanges of pressed areas, by optimizing the inflow of materials at multiple press-forming processes.
The Stress Reverse Forming™ Method is designed to reduce variation in the scale of springback (or variation in dimensional accuracies), which increases as ultra-high tensile steel sheets have higher levels of strength. When press-formed, ultra-high tensile steel sheets are more susceptible to springback and to large variation in strength intensities than regular steel sheets. The Stress Reverse Forming™ Method uses the Bauschinger Effect, or the mechanical phenomenon in which deformation stress in steel sheets decreases immediately after the direction of the deformation is reversed. This method enables customers to stabilize their production of press parts even if there are changes in the intensities of steel sheets.
The front bumper parts for which these two methods are used are manufactured by Okamoto Press Industry, Co., Ltd. In fact, both the inflow control method and the Stress Reverse Forming™ Method were jointly developed by Okamoto and JFE Steel.
JFE Steel is actively working on what it calls Early Vendor Involvement (EVI), an activity beyond the supply of raw materials, to provide customers with solutions to help them develop new products and increase the performance of existing ones. JFE Steel is developing various steel application technologies to offer comprehensive solutions, including a systematized solution called JESOLVA™, which is short for JFE Excellent Solution for Vehicle Application. JFE Steel strives to broaden the application of its ultra-high tensile steel sheets and help customers boost the performance and trim the weight of their vehicles to contribute to a sustainable future.
ST Ultra-High Tensile Steel Sheet Product Adopted for the First time as a Material for a Hybrid EV Battery Module Component
- Environmental Benefit
- Reduce CO2 emissions
- Status
- Development stage
The 980 MPa class galvanized steel sheet was the first of JFE Steel’s ultra-high tensile steel sheet products to be selected and used as a material for a lithium-ion battery module frame used in hybrid EVs.
A vehicle battery pack is comprised of multiple battery cells and bound with a steel frame to achieve a high power output. The frame must have a high bonding force to prevent the battery from swelling and from losing performance due to heat during use, and thus there has been demand for a high strength steel sheet. However, high-strength steel sheets are known to be susceptible to fracture when formed by bending. This process is required to minimize the curvature of the folding area of the frame to almost a 90-degree angle and thereby shrink the size of the battery module.
This issue can now be resolved with the use of a press-forming method using CAE* and product specs developed by J-MAX Co., Ltd. , both of which have enabled the use of JFE Steel’s 980 MPa class, galvanized steel sheet that has the high processability suitable for a battery module frame on hybrid EVs. This galvanized steel sheet is a product of the JEFORMA™ series, a lineup of steel sheets with high strength and high bending formability, properties achieved by optimizing the metallographic structure of the steel sheet through intricate temperature control at the continuous galvanizing facility of the West Japan Works (Fukuyama District). JFE Steel is seeking to expand the application of this galvanized steel sheet and will develop products and methods that will also satisfy customer needs. JFE Steel will contribute to a sustainable future by supporting customers in their development of safe, eco-friendly vehicles with lower CO2 emissions and higher performance.
- *Computer-Aided Engineering. A design tool using computer simulation.
Ultra-High Tensile Steel Sheet Product Adopted for a Hybrid EV Battery Module Component
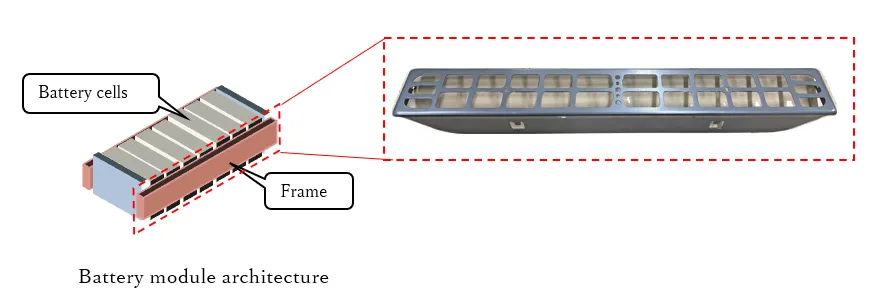
EN JFE Engineering’s Commitment through Its Business
With the corporate purpose “Foundation of Life—Just For the Earth” in mind, JFE Engineering is committed to achieving the SDGs in five areas: waste to resources, carbon neutrality, combined utility services, infrastructure, and digital transformation (DX).
Waste to resources businesses include food recycling, plastic recycling, and waste incineration/power generation. Businesses related to carbon neutrality focus on renewable energies, such as offshore wind, solar, biomass, geothermal, and hydroelectric power generation. Combined utility services offered by the company include utility services (e.g., water, electricity, gas) that address regional concerns by launching new local electric power companies and offering heat supply services. The company’s infrastructure business constructs bridges, gas plants, waterworks plants, pipelines, and other infrastructure by identifying needs such as robustness and longer service life. The DX project involves improving the efficiency of daily work as well as providing products and services that leverage digital technologies such as AI and IoT.
- JFE GROUP REPORT 2021 (PP. 43–44)
- JFE Engineering’s Five Fields in the Medium- to Long-term Strategy
- JFE Engineering DX Strategy
EN Offshore Wind Power: Launch of Operation at the Kasaoka Monopile Factory
- Environmental Benefit
- Renewable energy and reduce CO2 emissions
- Status
- Business expansion
- Feature
- Production of monopile foundations for offshore wind turbines
Amid growing expectations for offshore wind power as a source of green power production, an increasing number of projects are being introduced, as is seen in the public tender launched by the Japanese government in 2020 to select offshore wind power generation operators under the Act on Promoting the Utilization of Sea Areas for the Development of Marine Renewable Energy Power Generation Facilities. Foundation structures supporting offshore wind turbines are roughly categorized as seabed-fixed and floating. Seabed-fixed generators that can be installed in shallow sea areas are called monopile foundations. These are also the most economical option.
JFE Engineering built Japan’s first factory for monopiles on the premises of JFE Steel’s West Japan Works (Fukuyama District) Kasaoka City, Okayama Prefecture, and started operating the factory in April 2024. The Kasaoka Monopile Factory uses large, heavy steel plates supplied by JFE Steel’s West Japan Works (Kurashiki District) and is therefore reducing the amount of welding and streamlining assembly. The factory has an annual manufacturing capacity of around 100,000 tonnes of monopiles, with each unit having a diameter of up to 12 m, a plate thickness of 130 mm, a length of around 100 m, and weighing around 2,500 tonnes. The factory is also capable of manufacturing transition pieces for joining monopiles with wind turbine towers as well as large-scale steel pipes for building the columns of floating foundation structures.
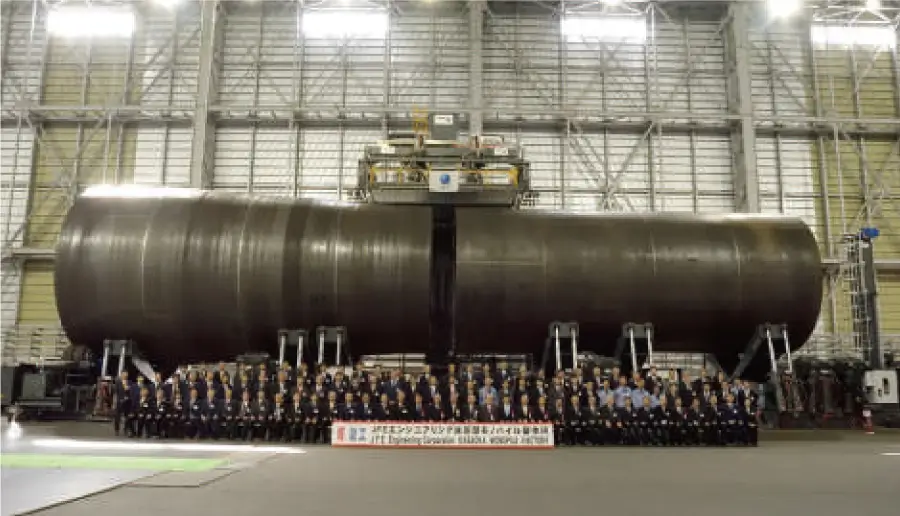
EN Offshore Wind Power, a Foray into O&M through a Remote Integrated Management System
- Environmental Benefit
- Renewable energy and reduce CO2 emissions
- Status
- Business expansion
- Feature
- Remote management of offshore wind power plants through the use of digital technology
For more than 25 years since 1996, JFE Engineering has been involved in EPC for onshore wind-power stations (131 generators at 25 sites) in addition to equipment supply and associated maintenance services. JFE Engineering will fully leverage its deep, extensive expertise in onshore wind power generation as well as technologies owned by other JFE Group companies to grow and advance its O&M services for offshore wind power plants.
In October 2023, JFE Engineering launched a 20-year O&M contract for offshore wind power facilities (three generators with the max output of 7,495 kW) off the coast of Nyuzen in Toyama Prefecture. These facilities were built under Japan’s first offshore wind energy project in a general sea area. JFE Engineering adopted a remote integrated management system for this project, the first of its kind in the nation for an offshore wind power project. The use of the system is allowing the company to provide systematic and preventive maintenance services and facilitate sensor management and data analysis for failure detection and diagnosis.
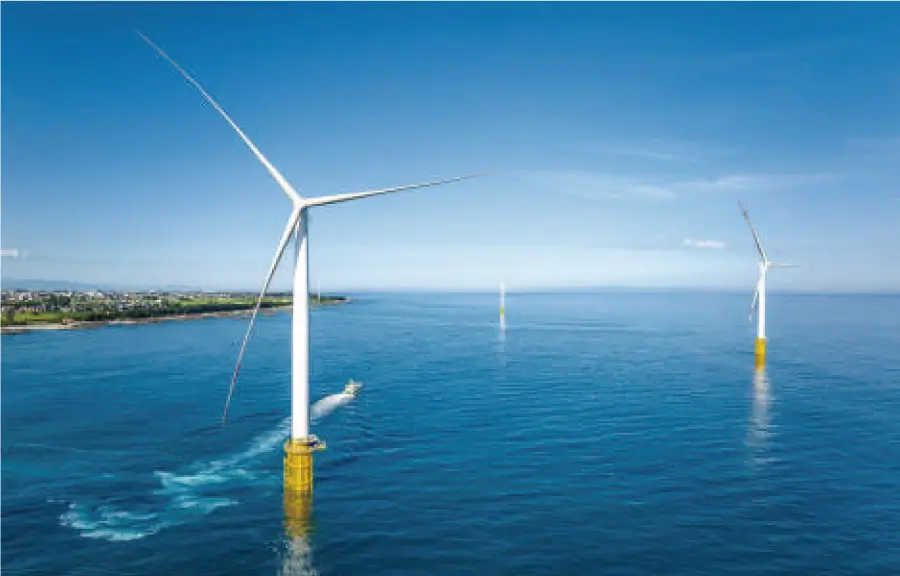
EN Contributing the Company’s Horizontal Directional Drilling Method to Japan’s First Installation of Telecommunication Optical Fiber Cables across Tokyo Bay
- Environmental Benefit
- Reduce environmental impact
- Status
- Commercialized
- Feature
- Telecommunication cable installation with the company’s Horizontal Directional Drilling Method
JFE Engineering has completed the construction of a transmission channel across Tokyo Bay as a project ordered from Nippon COMSYS Corporation. The ongoing advance of information and telecommunication technologies have made telecommunication networks indispensable in daily life, and the growing volume of telecommunication traffic requires an increasing number of optical communications facilities.
Construction involved laying a pipeline for installing telecommunication optical fiber cables between Tokyo’s Shibaura and Shinagawa areas, where many tech companies are located, and between the city’s Toyosu and Ariake areas, thereby establishing a network with the shortest route. The challenging work required laying the pipeline deep undersea to prevent damaging seawalls and other protection structures around Tokyo Bay as well as handling nearly 2,000 meters of pipeline, one of the longest in Japan. The construction was completed successfully without accident within just two months, thanks to the use of the JFE-RAPID™ method, a pipeline technology developed by JFE Engineering to facilitate quick, low-cost construction.
The JFE-RAPID™ method makes it possible to bring down construction cost and shorten the work period by drilling at the sea bottom and moving the pipeline forward through a circular boring method instead of installing vertical shafts. This is an effective method for installing telecommunication cable and a promising technique for laying power cable pipelines for offshore wind-power stations.
The pipeline (for illustrative purpose only)
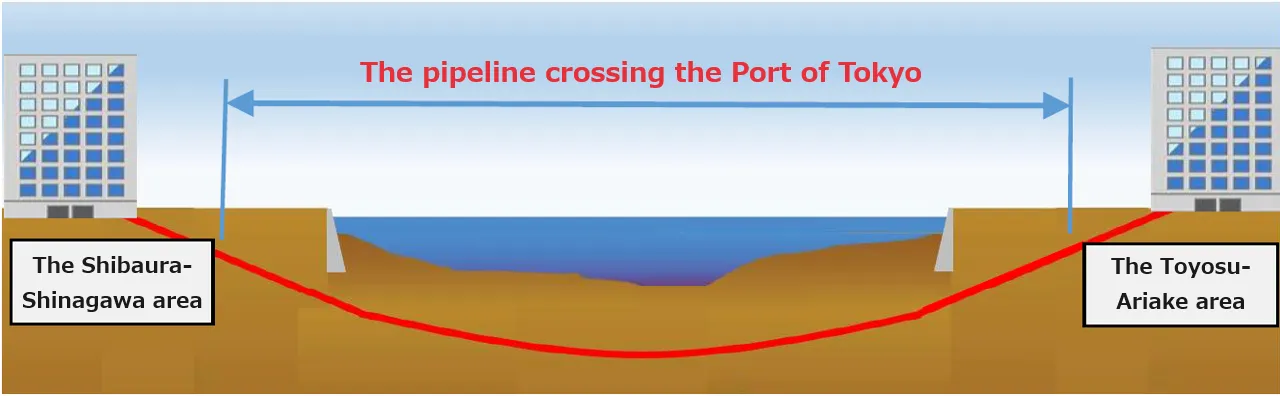
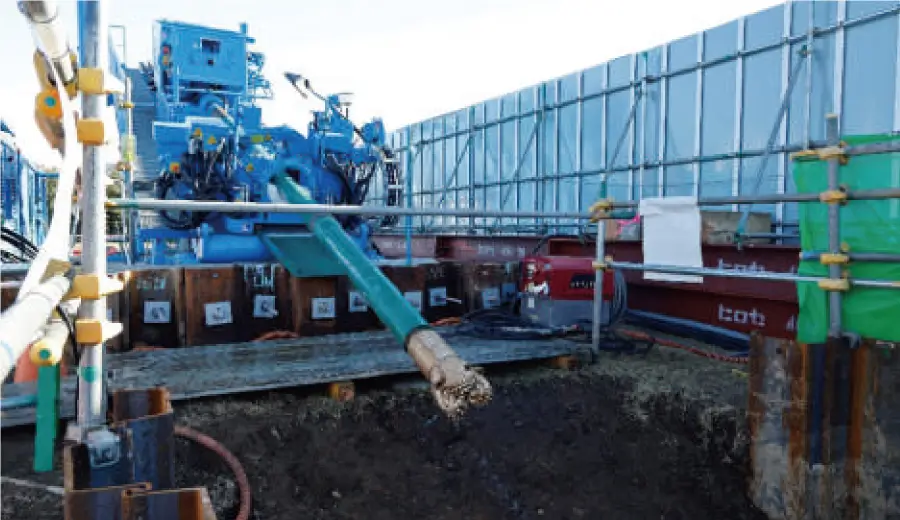
EN Aqua Connect Namie Corporation Launches Hydroelectric Power Generation Business at the Ukedogawa Hydro Power Plant
- Environmental Benefit
- Recycle resources and reduce CO2 Emissions
- Status
- Commercialized
- Feature
- Matching local social needs and JFE Engineering Group’s technologies
Aqua Connect Namie Corporation, a company established through the joint investment of JFE Engineering with The Tokyo Electric Generation Co., Ltd. and the Ukedogawa Land Improvement District (the town of Namie in the district of Futaba, Fukushima Prefecture), launched its power generation business at the Ukedogawa Hydro Power Station, becoming the first hydrogen power generation business for JFE Engineering. The business was established to take advantage of the agricultural water supplied from the Ogaki Dam to the ward of Odaka in the city of Minamisoma and to the towns of Namie and Futaba in the district of Futaba.
The Ukedogawa Hydro Power Station, with its waterwheel and power generator located at the foot of the Ogaki Dam, generates power by using the energy produced from the difference in water levels. All the power generated at this station is sold through the Feed-in Tariff System. Aqua Connect Namie Corporation is committed to operating the station safely and stably while supporting farmers in the Ukedogawa area. The company will thereby contribute to carbon neutrality and a sustainable future.
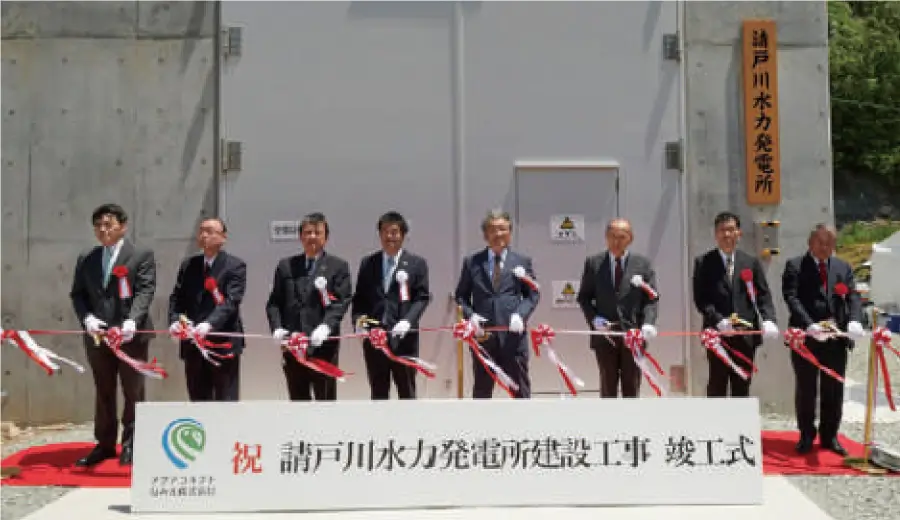
EN Provision of Combined Utility Services
- Environmental Benefit
- Electric renewable energy and reduce CO2 emissions
- Status
- Commercialized
- Feature
- Matching local social needs and JFE Engineering Group technologies
Myoko Green Energy Co., Ltd. was established through co-funding by JFE Engineering, Hokuriku Gas Co., Ltd. , and INPEX Corporation under a basic agreement with the city of Myoko concerning the transfer of the municipal gas business and the delegation of the water and sewage services from the city to the private sector. The company has been providing utility gas, supplying water, and managing sewage for Myoko City, Niigata Prefecture, since April 1, 2022, to establish an urban infrastructure that ensures stable utility services for the citizens.
Myoko City, where the company is located, announced the Myoko Zero-carbon City Declaration in June 2020 and enacted an ordinance promoting it in April 2021. Because of the project’s focus on carbon neutrality, Myoko was selected by the central government as a SDGs Future City in May 2021 and has been working on the project plan. To contribute to this initiative, Myoko Green Energy entered into a partnership for realizing a zero-carbon society with Myoko on March 14, 2022. One of the goals of the partnership focuses on the local production and consumption of electricity. To that end, the company started a local effort to collect and recycle renewable energy sources and has since distributed approximately 3,000 kW of zero-carbon electricity to 20 establishments belonging to the city.
Myoko Green Energy aspires to serve as a utility coordinator for local communities and is acquiring the required capabilities for handling infrastructure projects and services like those conducted and provided by Stadtwerke in Germany (See the diagram below).
Myoko Green Energy’s vision for itself in the future—Serving as an infrastructure company
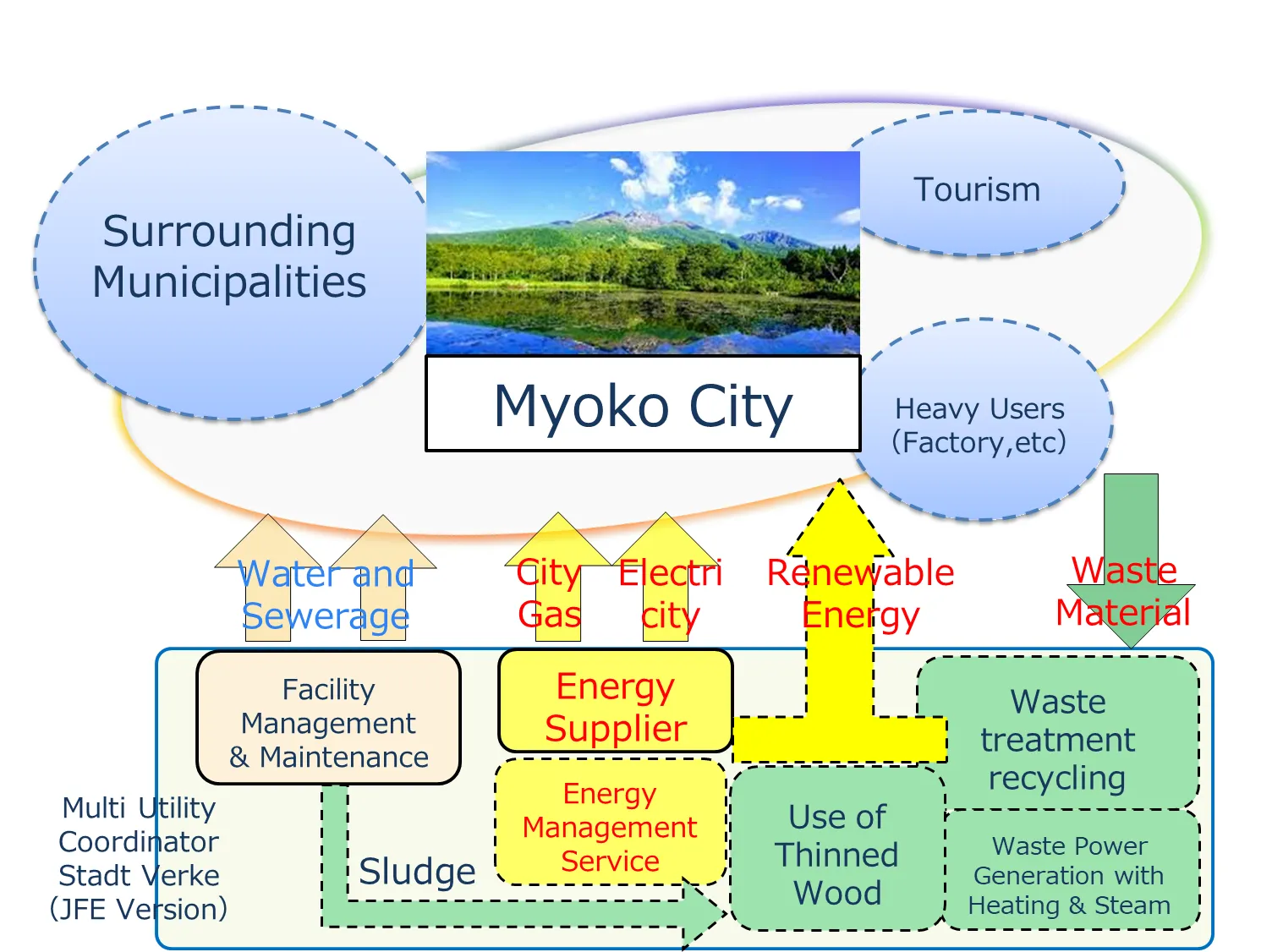
EN Promoting Plastic Recycling
- Environmental Benefit
- Recycle resources
- Status
- Commercialized
- Feature
- Matching local social needs and JFE Engineering Group technologies
J&T Recycling Corporation joined Sendai City’s plastic recycling project, the first of its kind authorized by the Minister of the Environment and the Minister of Economy, Trade and Industry. The project was launched under the renewed Act on Promotion of Resource Circulation in September 2022 and subsequently started a service in April 2023 to recover waste plastic products and containers in the city. Waste plastic products previously had been disposed of by incineration, and the service launched by J&T Recycling to recover waste plastic products and containers has boosted the efficiency of the city’s plastic recycling efforts.
Moreover, J&T Recycling partnered with the JR East Japan Group and established J Circular System Co., Ltd. , in Kawasaki, Kanagawa Prefecture in July 2023 to promote the recycling of plastic items across the country. The company’s facilities are capable of processing 200 tons of waste plastic a day as one of the largest recycling operations in the Tokyo metropolitan area. J Circular System is expected to launch full-scale operations in April 2025, to include segregating waste plastic items by type beyond simply recovering them, and recycling the goods into raw materials for other plastic items or converting them into chemicals.
In cooperation with the city of Kawasaki and its neighboring municipalities, J Circular System is developing a plastic recycling plant based on the aforementioned renewed act and seeking to obtain a national license to operate its integrated plastic-recycling business. This will help make the conventional intermediate treatment process for waste plastic simpler and more rational.
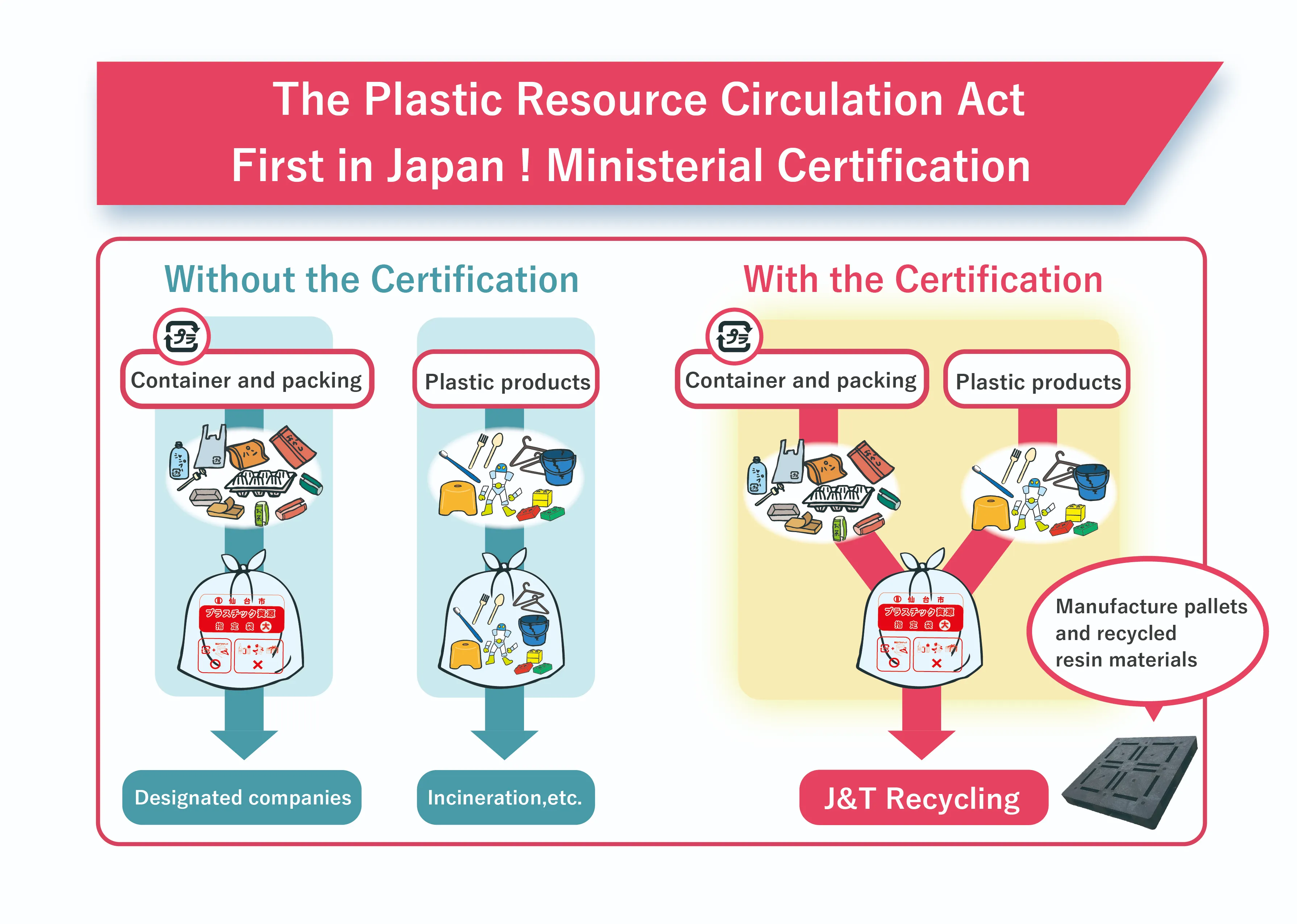
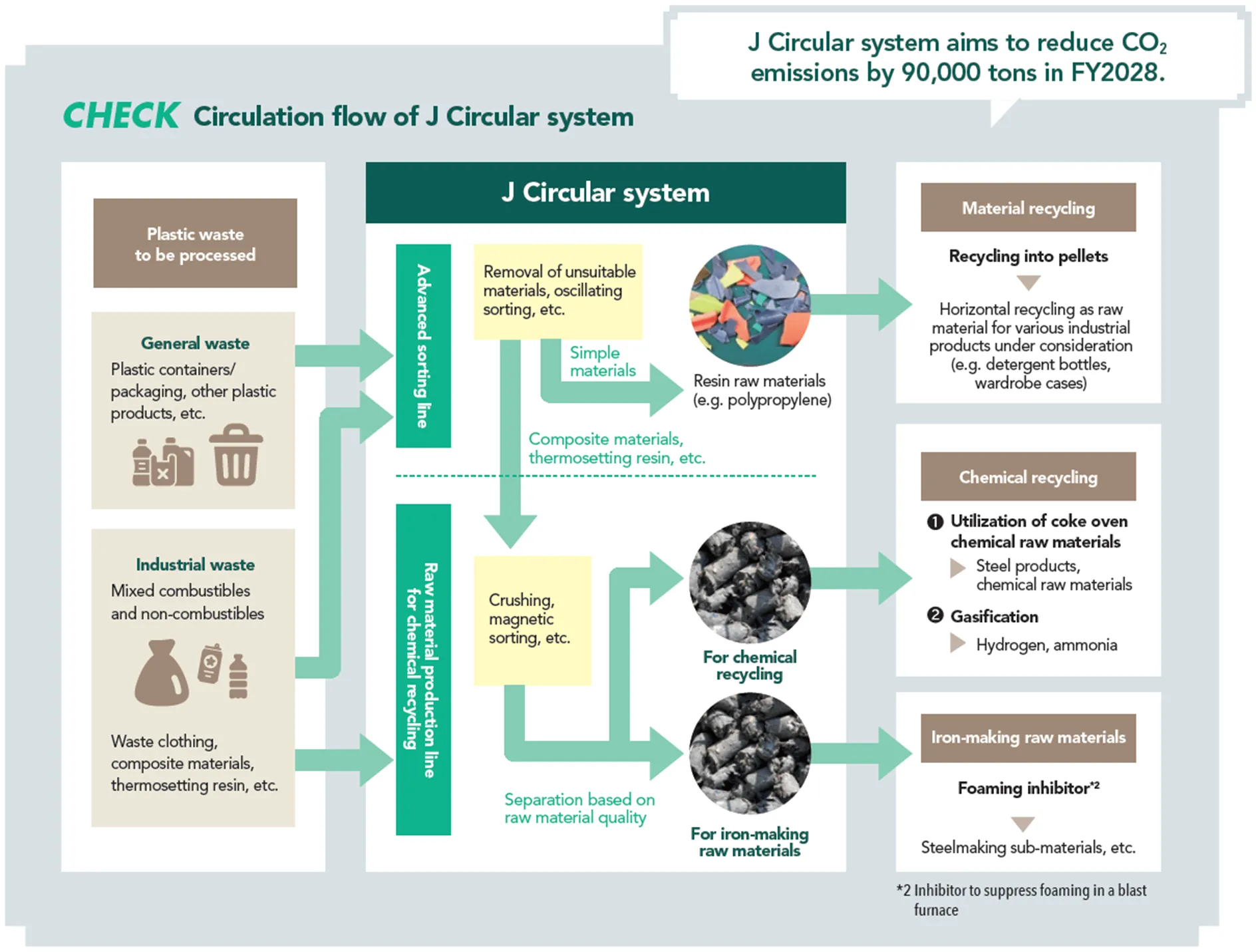
- J&T Recycling Corporation Joins the Municipal Waste Plastic Recycling Project of Sendai as Japan’s First Private-Sector Recycling Operator
- J&T Recycling Corporation Establishes J Circular System Co., Ltd.—Its Plastic Recycling Facilities on the Kawasaki Waterfront Have the Largest Scale in the Tokyo Metropolitan Area
EN Renewal of the Chugoku Expressway, the Company’s Largest-Scale Project
- Environmental Benefit
- Reduce environmental impact
- Status
- Commercialized
- Feature
- Proprietary technology for streamlining bridge construction
Large-scale construction to renew aging express highways are either underway or about to be launched around Japan. The Chugoku Expressway, western Japan’s traffic aorta opened in 1970 to coincide with the Japan World Exposition Osaka 1970, is one of these aging highways, with the renewal under way between Suita JCT and Chugoku-Ikeda IC toward completion in October 2024. This project involves replacing a total length of 10.8 km of bridges and using about 17,300 tonnes of steel. JFE Engineering represents a joint venture established for this project at the largest scale JFE Engineering has ever undertaken.
In March 2023, the work requiring all-day closures, one of the larger construction components of this project, was completed. The work was carried out in six separate 90-day sessions to ease public impact, because the bridges stand along the Osaka Central Loop Motorway and intersect with railways. During periods of heavy traffic, however, the closures had to be suspended, limiting the available time for this work. Several new methods and technologies proposed by JFE Engineering, including the company’s jack-up method, were adopted to facilitate these all-day closures.
The JFE Engineering’s jack-up method allows for construction preparation regardless of weather conditions while maintaining a constant workload. This method, in which new beams are built below older ones, also reduces the costs of scaffolding and the need to transport new beams while streamlining construction.
JFE Engineering will deploy its latest technologies and rich expertise to minimize the disruptive impact of bridge renewal work on traffic and society.
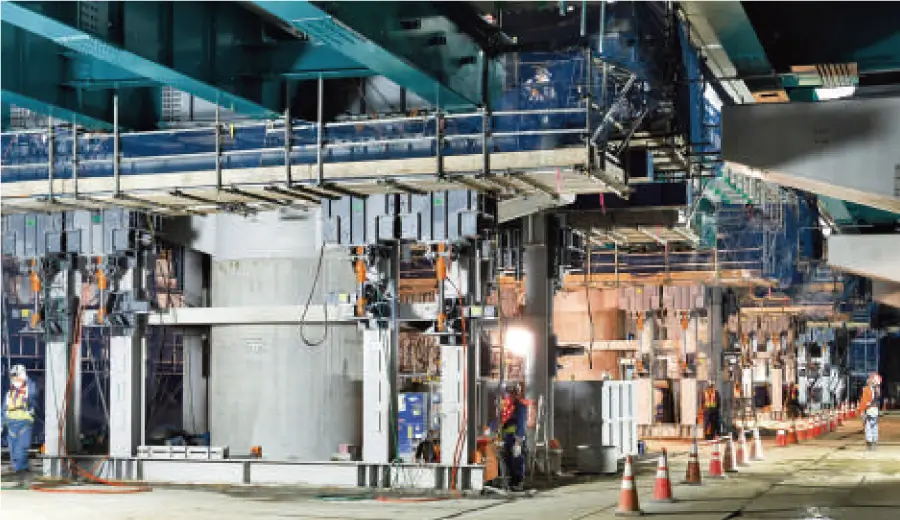
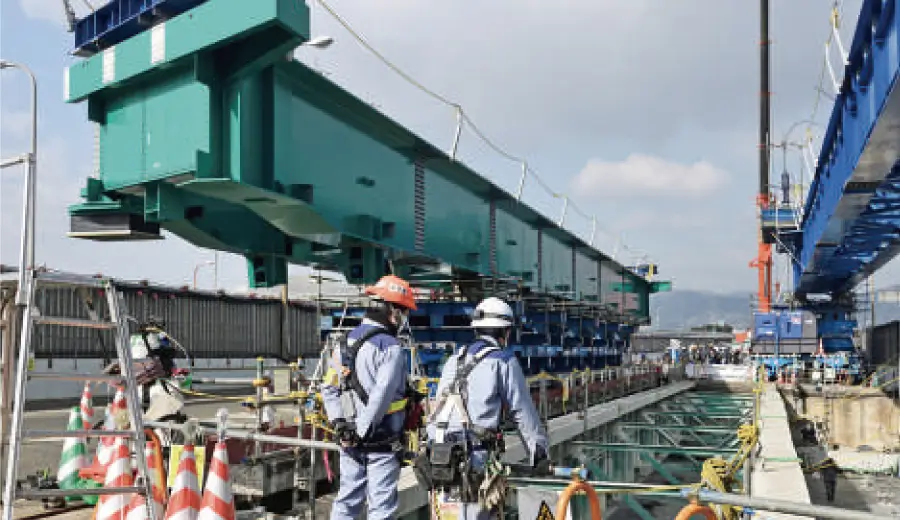
JFE Engineering’s Jack-up Method
This is a method for assembling new bridge beams in advance and thereby enabling them to immediately replace old ones after a highway has been closed off. New beams are used as the scaffolding for removing old ones. The method allows operators to arrange workers and machines in advance while maintaining a constant workload during a highway closure.
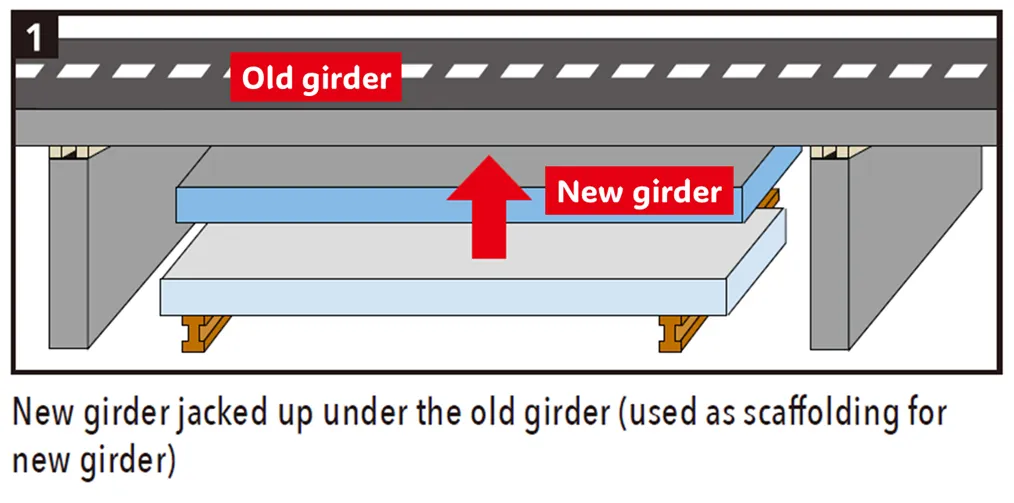
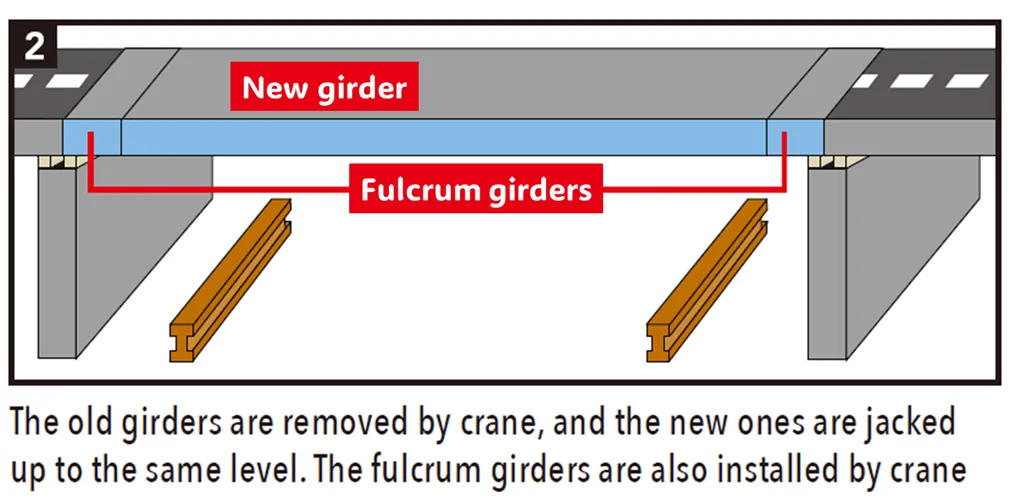
EN Development of a Waste Chemical Recycling Technology (C-PhoeniX Process™) through the Use of the Green Innovation Fund
- Environmental Benefit
- Recycle resources
- Status
- Development and verification stage
- Feature
- Participating in a national technology development project
JFE Engineering responded to a public invitation to participate in a Green Innovation Fund Project issued by NEDO (New Energy and Industrial Technology Development Organization) in February 2024 and was selected*1. Following more than two decades of trial and error, JFE Engineering established a technology to convert domestic and other kinds of waste into processable gases. The company’s unique gasification furnace has the longest running record in the world. The company is currently developing a new gasification technology, C-PhoeniX Process™ (or CX Process™), to improve and ultimately replace the current technology for carbon neutrality.
The C-PhoeniX Process™, based on the company’s accumulated technological expertise, exhibits an advanced capability to constantly produce high-quality, purified synthesis gases, consisting primarily of hydrogen and carbon monoxide, from a wide range of waste materials. Once established, this technology will be applicable to the waste-to-chemical (WtC) process, enabling many types of waste to be recycled for different purposes, including the production of plastic, sustainable aviation fuel (SAF), and hydrogen.
Through the use of the national Green Innovation Fund, JFE Engineering is set to develop a waste chemical recycling technology in cooperation with SEKISUI CHEMICAL Co., Ltd. , which owns a technology for converting waste-originated purified synthesis gases into ethanol. In the meantime, JFE Engineering will accelerate the development of its C-PhoeniX Process™ for the advancement and social implementation of WtC. Development under the Green Innovation Projects is scheduled to be completed by the end of FY2030. JFE Engineering will deploy these two technologies, once established, overseas as well as in Japan, and will thereby contribute to the achievement of carbon neutrality by 2050.
- *1NEDO launches its Green Innovation Fund Projects to Achieve Carbon Neutrality in Waste and Resource Circulation
Overview of Waste Chemical Recycling
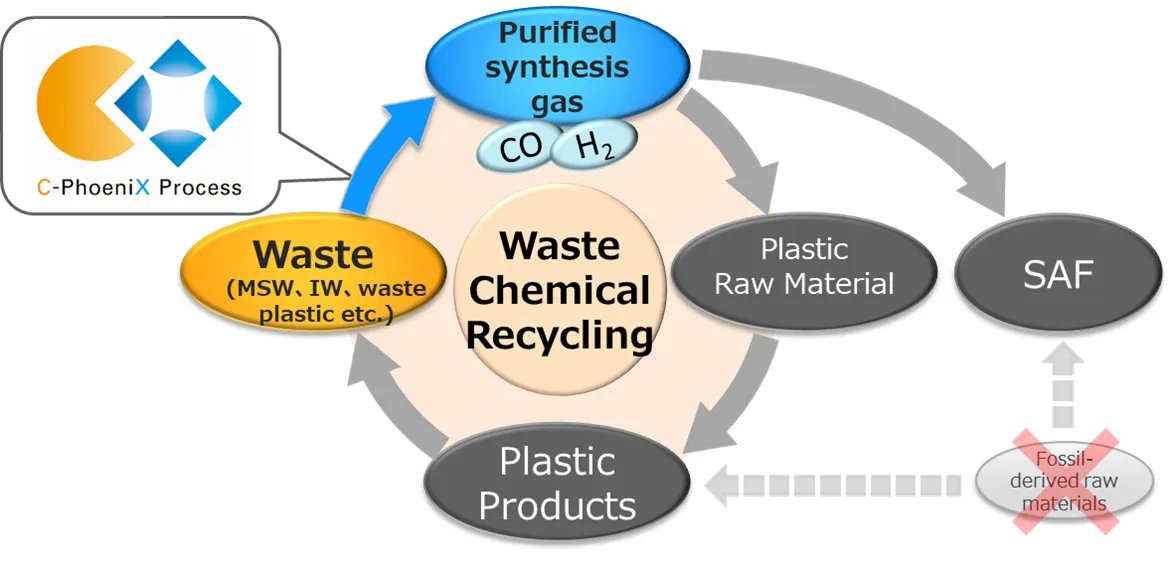
Entire Process and Development Domains
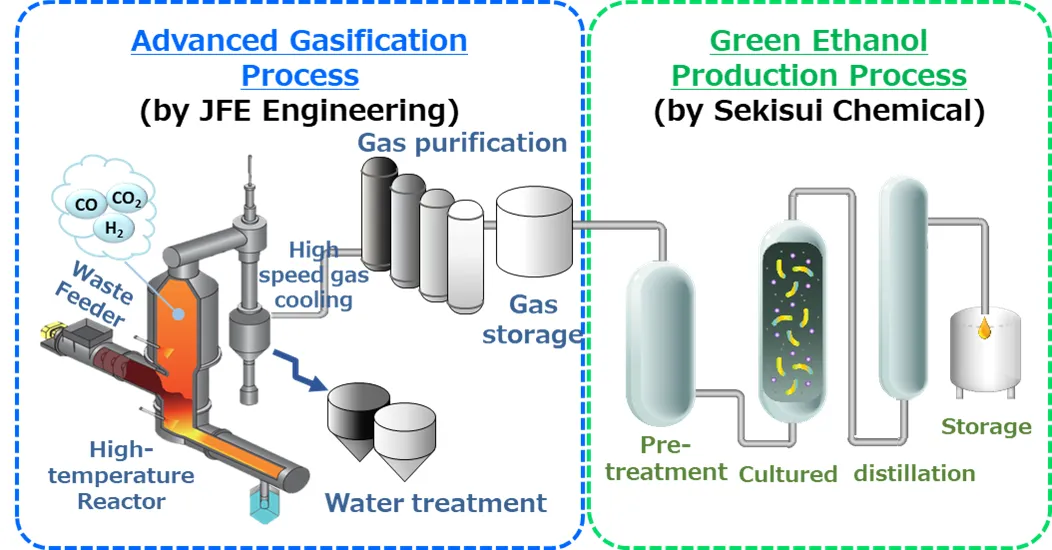
- Developing the Advanced Waste-to-Chemical Gasification Process, the “C-PhoeniX Process™” Toward Practical Use in Society
- “Waste-to-Chemical Technology Development for Green Ethanol Production by Integrating Advanced Gasification and Biochemical Conversion Technologies” adopted for the NEDO Green Innovation Fund project
EN The Energy Forest Project (Demonstration Project for Creating Stable and Effective Supply Systems for Woody Biomass Fuel)
- Environmental Benefit
- Renewable energy and reduce CO2 emissions
- Status
- Development and verification stage
- Feature
- Participating in a national technology development project

The town of Yuni, located in Hokkaido, and JFE Engineering are jointly carrying out an Energy Forest Project, which will continue until the end of FY2028. This project, named JFE Forest NEXTAGE Project and drawn up by JFE Engineering, was selected by NEDO (New Energy and Industrial Technology Development Organization), a national research and development agency, for inclusion in the FY2023 Demonstration Project on Development of New Fuel Sources Such as Fast-growing Trees on August 3, 2023. JFE Engineering is specifically engaged in pioneering research for creating a large “energy forest,” involving the silviculture of trees that grow well and fast in a subarctic climate (clean larch and Sakhalin willow) on land owned by the town of Yuni.
The town of Yuni is seeking to nullify CO2 emissions by 2050 under the Unicho Zero Carbon City declaration. JFE Engineering is working with the town of Yuni to contribute to carbon neutrality and prevent global warming, thereby fulfilling its corporate purpose, “Foundation of Life—Just For the Earth.”
- The Town of Uni and JFE Engineering Enter into an Agreement Concerning the Energy Forest Demonstration Project
Eco-friendly Processes, Products, and Technologies that Were Upgraded
ST Certification by SuMPO’s EcoLeaf Environmental Labeling Program
- Environmental Benefit
- Reduce environmental impact
- Status
- Commercialized
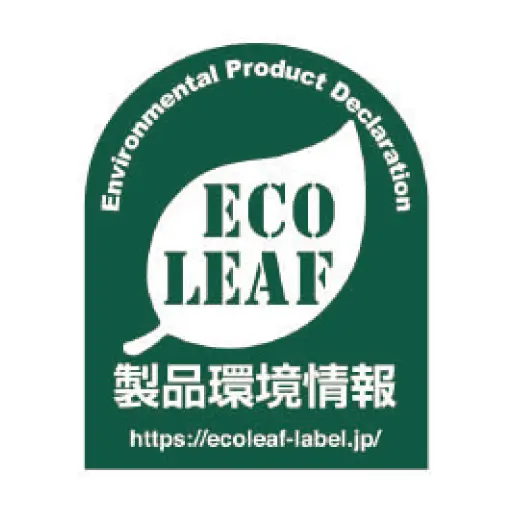
JFE Steel has acquired certification for EcoLeaf, a Japanese environmental product declaration (EPD) program managed by the Sustainable Management Promotion Organization (SuMPO) in Japan for three types of steel sheets for cans: tinplate, JFE Universal Brite (laminated steel sheet), and tin-free steel; five types of building materials: H-beams, JFE Super HISLEND-H beams, extra- thick H beams, construction steel plates, and construction steel columns; and three types of steel plate products: for offshore structures and wind power generating equipment, ship building, and UOE steel pipes; and three types of steel pipes: welded steel pipes, seamless steel pipes, and Kakuhot™ construction seamless square steel pipes.
EcoLeaf is a Type III EPD program managed by SuMPO for quantitatively disclosing the environmental impact of products and services throughout their life cycle, from raw material procurement to disposal and recycling in accordance with ISO 14025:2006 (environmental labels and declarations, Type III Environmental Declarations, Principles and Procedures). The environmental impact of our products is presented as graphic representations of data to increase transparency. The disclosure of environmental impact data with fairness and reliability assured by third-party review and verification enables customers to quantitatively and objectively evaluate the environmental impact of the products they use.
EcoLeaf was renamed SuMPO EPD in April 2024. Going forward, JFE Steel will actively promote the acquisition and publication of SuMPO EPD for its products.
ST Ferro-Coke
- Environmental Benefit
- Save energy and reduce CO2 emissions
- Status
- Experimental operation
How energy saving and CO2 reduction are assessed at model steelworks
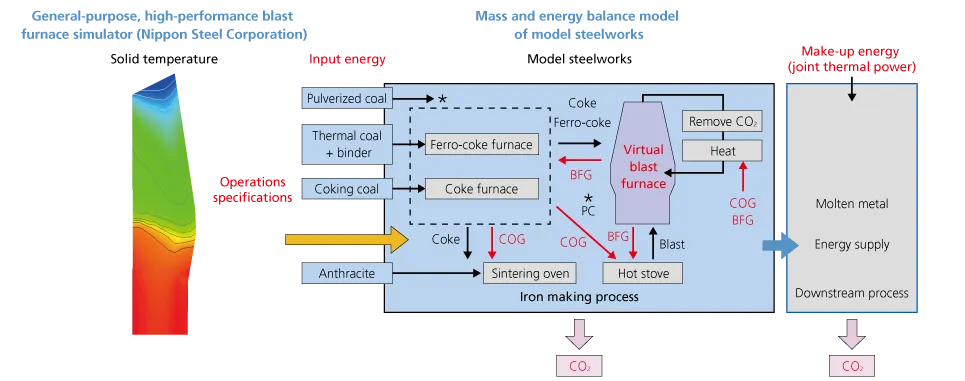
Ferro-coke is an innovative raw material for blast furnaces made by mixing low-grade coke and iron ore. In this energy- saving technology, metallic iron contained acts as a catalyst, reducing the amount of coke required in the furnace and thus significantly reducing CO2 emissions in the iron making process.
In the six years from FY2017 to FY2022, JFE Steel engaged in a project to develop environmental technology for the steelmaking process, and technological development of the iron making process using ferro-coke, a project by the New Energy and Industrial Technology Development Organization. In 2022, the company conducted a test using ferro-coke made from affordable iron core at a facility with a daily capacity of 300 tonnes. In the test, the company used 30 kg/t of the ferro-coke at a furnace of the West Japan Works (Fukuyama District) and observed a 10 kg/t reduction in the reducing agent ratio. In 2023, the company produced ferro-coke from a mixture of even more economical iron core with fuel coal for use in pulverized coal injection and tested the ferro-coke at a furnace.
JFE Steel plans to conduct a laboratory test to clarify the materials for ferro-coke production that can reduce both material cost and the agency ratio before moving on to a pilot experiment.
ST R&D into Line Pipe for Transporting High-Pressure Hydrogen Gas (Selected for Inclusion in the Nippon Foundation), and DeepStar Joint Research & Development Program Phase II
- Environmental Benefit
- Recycle resources and reduce CO2 emissions
- Status
- Development stage
JFE Steel conducted research and development into the property evaluation of line pipe for transporting high-pressure hydrogen gas in a hydrogen-related technical development Phase-I under The Nippon Foundation*1—DeepStar*2 Joint Research & Development Program on Offshore Oil and Natural Gas*3 (“the Project”), which is being conducted in cooperation with major oil companies. Recognition of Phase-I results led to the selection of the R&D project for inclusion in the program’s Phase II. In this phase, JFE Steel will expand the scope of the research to include thick, high-strength UOE steel pipes*4 intended for seabed pipelines, and it will continue to work with DeepStar consortium members ExxonMobil and Chevron of the U.S.A. and TotalEnergies of France to establish evaluation criteria and methods using the company’s Mighty Seam™ electric-resistance-welded steel pipe*5 to transport high-pressure hydrogen for realizing the world’s first commercial high-pressure hydrogen pipeline.
Since hydrogen does not emit CO2 during combustion, the large-scale use of hydrogen for various purposes, such as fuel for power generation, is being widely considered for achieving carbon neutrality by 2050. The use of a pipeline similar to the current supply chain for natural gas is being explored for transporting hydrogen in bulk from its production plant and receiving terminal to where it is needed. Meanwhile, hydrogen causes steel materials to become brittle (reducing ductility). Consequently, methods for evaluating the performance of materials are being established in countries other than Japan to support safety standards and quality inspections. As in Phase I, JFE Steel’s Steel Research Laboratory in Chiba, Japan, will research properties required for high-pressure hydrogen pipelines, particularly through the application of the Engineering Critical Assessment*6. The company will also evaluate performance under high-pressure hydrogen environments using a steel pipe specimen as well as welded area samples to verify safety.
The JFE Group will continue to promote research and development that will contribute to the realization of a hydrogen society. By meeting the needs of customers who are working on the supply and wider application of hydrogen, the JFE Group will help realize carbon neutrality.
- *1A public interest incorporated association designated as a ship promotion organization by the Ministry of Land, Infrastructure, Transport and Tourism of Japan. Funding for its activities is drawn from the proceeds of motorboat racing held by local governments throughout Japan, to primarily support maritime shipping-related business, engage in public services/welfare business, and international cooperation.
- *2An offshore technology development consortium consisting of businesses that engage in globally exploring, developing, and producing offshore oil and natural gas, such as Chevron, Shell, and Equinor, as companies that carry out offshore oil field development and production, and other businesses, universities, and research institutions that offer products and services to those businesses.
- *3A joint grant program of the Nippon Foundation and DeepStar for research and development projects for advancing decarbonization in offshore oil and natural gas areas.(Japanese only)
- *4Made by forming a steel plate through cold-pressing in two steps, first into a U shape and then an O shape, and then, after arc-welding the joint, expanding the tube while adjusting the shape.
- *5An electric-resistance-welded steel pipe for line pipe, with excellent weld quality.
- *6A technology for evaluating safety from a mechanical standpoint, by comparing the forces acting on a structure with material toughness obtained from material testing.
ST Steel Slag Hydrated Matrix
- Environmental Benefit
- Recycle resources and reduce CO2 emissions
- Status
- Commercialized
Steel slag hydrated matrix is a steel slag product that can be used as a substitute for concrete but uses ground granulated blast furnace slag instead of cement, and steel slag instead of natural gravel and sand aggregate, as its ingredients. It effectively uses steel slag and does not rely on natural aggregate, thereby reducing environmental impact, and uses less cement, in turn reducing CO2 emissions.
There are many examples of blocks and artificial stones made from steel slag hydrated matrix being used as a substitute for concrete blocks and natural stones in harbor works, apart from the expected application for scour-prevention at the growing number of offshore wind-power stations to be constructed in the near future. In addition, we are conducting on-site monitoring in the Katsunan Central Zone of Chiba Port with the help of a local fishing association to assess the impact of these blocks on marine biodiversity.
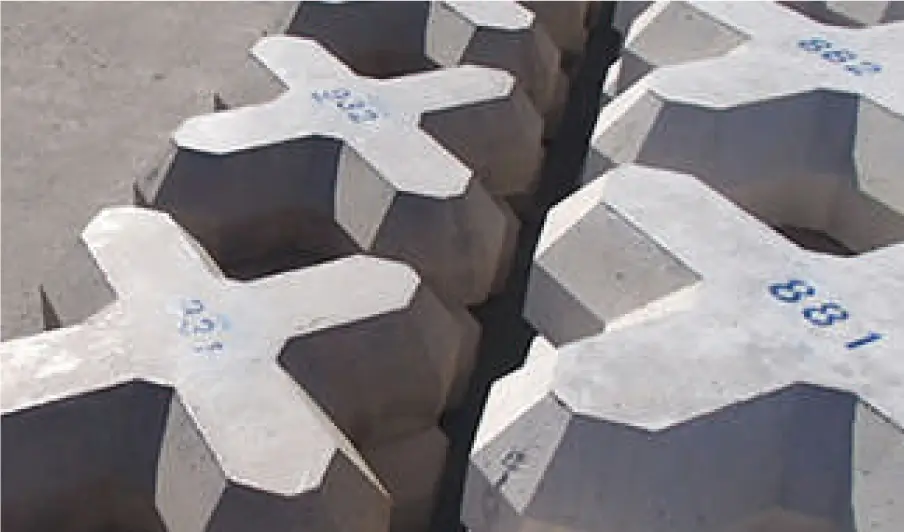
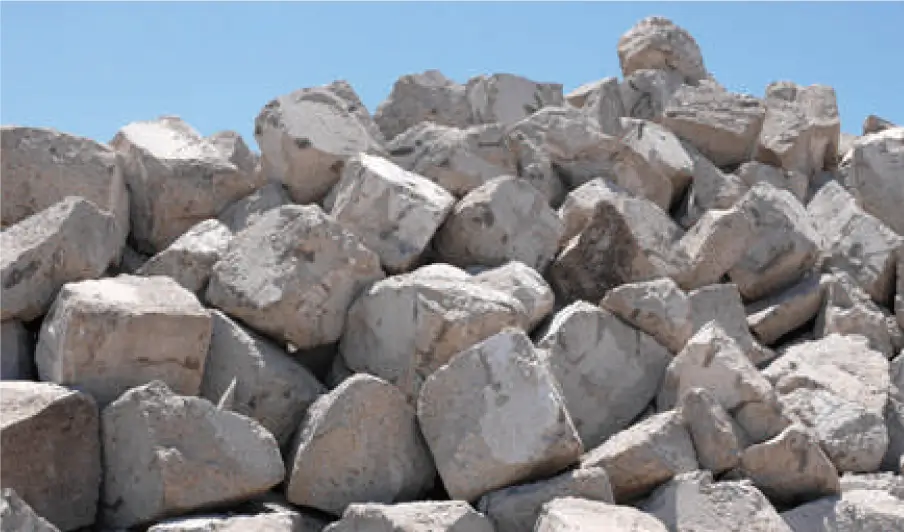
ST Initiatives for Blue Carbon Using Steel Slag Products and Acquisition of J Blue Credit™
- Environmental Benefit
- Recycle resources, preserve biodiversity, and absorb and secure CO2
- Status
- Commercialized
In recent years, research on blue carbon (carbon absorbed and stored by living organisms in the ocean) has been advancing. JFE Steel has been participating in the research by creating a seaweed bed using steel slag products and measuring the amount of carbon captured by the entire bed.
The company has been collaborating with Koujiro Fisheries Cooperative (Iwakuni City, Yamaguchi) and the National Institute of Technology, Ube College (Ube City, Yamaguchi) on a project to create a seaweed bed and ecosystem using recycled materials at areas around Shinto, Iwakuni City, since FY2012. The initiative involves creating a seaweed bed with rich biodiversity using Marine Stone™, a grain-size-adjusted steel slag, and other steel slag products, and measuring CO2 absorption of the created beds. The cumulative amount of CO2 absorbed and stored from 2018 to 2022, which totaled 80.7 tonnes, received J Blue Credit™ certification by the Japan Blue Economy Association. This was the first certification ever given to a three-party joint project by the Fisheries Cooperative, academia, and private business. The seaweed bed created through the project had the co-benefits of offering a gathering place for diverse fish. The sea area is also useful for education and research.
This initiative was highly regarded, and its members and JFE Steel received the Ministry of Agriculture, Forestry and Fisheries Prize for the 32nd Global Environment Award*, sponsored by the Fujisankei Communications Group in 2024.
- *The Global Environment Award recognizes environmental preservation and related efforts that will help establish a circular society for a “harmonic coexistence between industrial development and the environment of the Earth.”
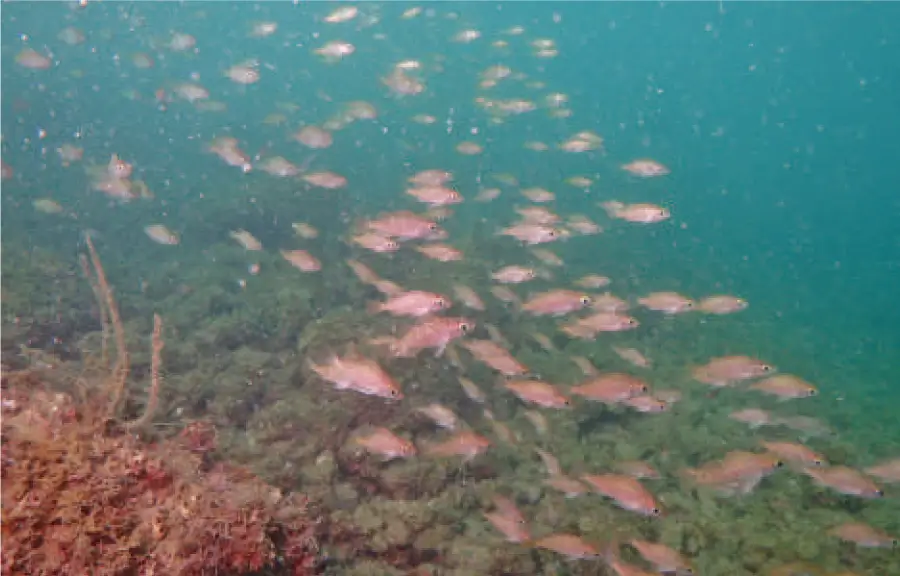
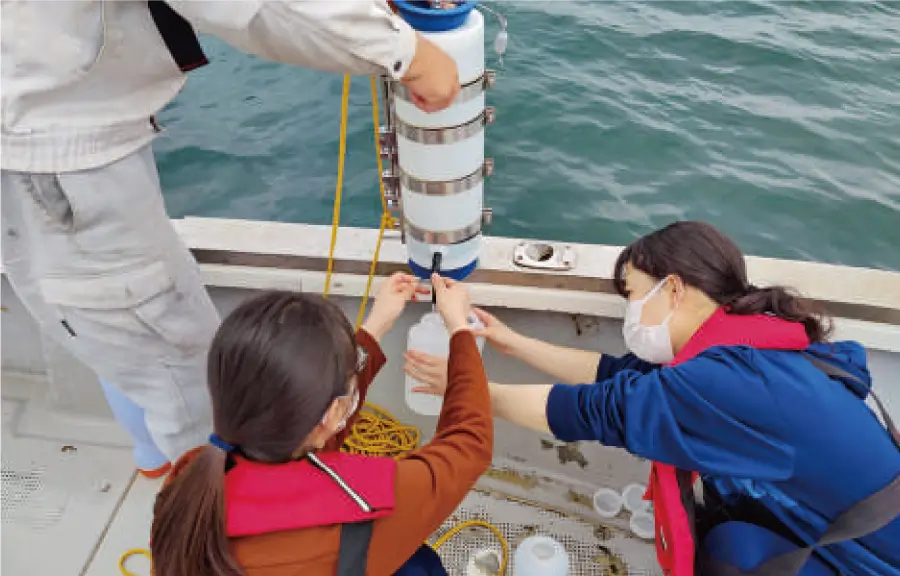
SH Building a Supply Chain for the Offshore Wind Power Generation Industry
- Environmental Benefit
- Renewable energy
- Status
- Sales expansion
Initiatives toward carbon neutrality are expanding around the world to tackle the shared issue of climate change. Japan has set its goal to achieve carbon neutrality by 2050 and formulated the Sixth Strategic Energy Plan in 2021 to lay out strategies to that end. These ambitious strategies include reducing greenhouse gas emissions by 46% in FY2030, boosting renewable energy in its electricity mix to 36–38%, and increasing the ratio of wind in the renewable energy mix to 5% (generating capacity of 23.6 GW) compared to the 0.9% (generating capacity of 4.5 GW) in FY2019.
As for offshore wind power generation, the industry is expected to expand, as targets were set to accept proposals to build 10 GW capacity by 2030 and 30–45 GW by 2040, and the commercialization of those proposals is in progress. Moreover, as is seen in the selection of a demonstration project for floating offshore wind-power generation as a Green Innovation Fund Project, efforts are underway to adopt many internationally competitive technologies.
JFE Shoji is collaborating with a local enterprise that manufactures the wind turbine foundations in Taiwan, which is leading in the offshore wind power generation market, and have been achieving progress regarding supply chain of steel materials for foundation structures. Looking ahead, the company will capitalize on the knowledge acquired and contribute to the realization of carbon neutrality by establishing a supply chain that supports the domestic production of goods and the local economy while also meeting customer demand in the offshore wind power generation industry in Japan.
Major Eco-Friendly Processes, Products, and Technologies in the Past
ST Technology for Optimized Combustion of a Coke Furnace
- Environmental Benefit
- Save energy and reduce CO2 Emissions
- Status
- Operation in production process
Architecture of the coke furnace and the digital twin model
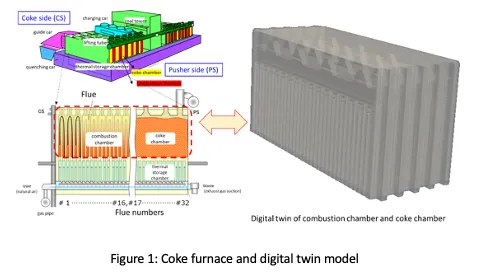
JFE Steel has completed technological development of a new facility at the coke furnace in the West Japan Works (Fukuyama District), which is capable of saving energy and cutting CO2 emissions, by using digital-twin technology, and has started the operation of the process.
We intend to transform into an intelligent steel works through the deployment of cyber physical systems (CPSs) as part of our digital transformation (DX) strategy. Digital twins are a core CPS technology in which physical systems and processes in the real world are replicated with equivalent properties in a digital model (“twin”) in a virtual space, allowing for an accurate simulation of the real world. These digital models make it possible to visualize highly inaccessible internal areas of facilities to optimize the design and operation of manufacturing processes for which internal conditions have conventionally been difficult to confirm via sensors or direct observation. The use of the digital twin also makes it possible to predict the effects of major changes to facilities or operations.
The technology was applied to process improvements for the operation of the Number 5, D Group coke furnace in the Fukuyama District of the West Japan Works. The information obtained from the digital twin of coke furnace constructed in virtual space confirmed that a mechanism for partially controlling air supply will achieve greater operational efficiency, information that the company can use for calculating the amount of supplemental air needed to optimize combustion. JFE Steel then applied these learnings in developing the new facility, which is now in commercial operation. The company has achieved an approximately 5% reduction in the amount of fuel used and has reduced its CO2 emissions by 6,600 tonnes a year, compared to the level with the furnace’s previous design. This project was chosen for the Japanese government’s Sustainable Open Innovation Initiative funding.
ST Fuel and Power Operation Guidance System for Steelworks
- Environmental Benefit
- Save energy and reduce CO2 emissions
- Status
- Development stage
Guidance System Overview
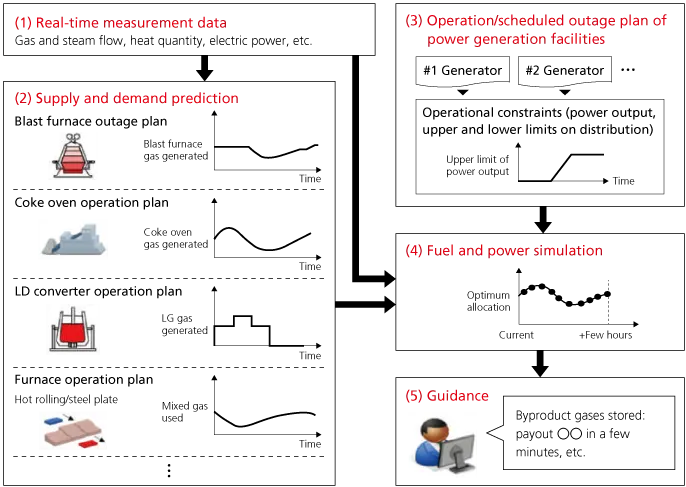
JFE Steel developed a fuel and power operation guidance system for steelworks and succeeded in saving energy and reducing CO2 as well as fuel and power by optimizing the fuel, steam, and electric power used in the steelmaking process.
Previously, operators determined various factors such as the distribution of byproduct gas to each process, amount of fuel (heavy oil, city gas, etc.) and electricity to purchase, and the amount of byproduct gas stored, taking into account energy demand and supply (amount generated and used) as well as the operating conditions of power generation facilities, to minimize cost and energy loss. However, it was difficult to use this method to accurately estimate the change in energy demand and supply. The guidance system (diagram 1) developed by JFE Steel uses voluminous real-time measurement data (1) obtained through a cyber physical system (CPS)* and the precise production plans of each factory to predict future demand and supply with high accuracy (2), and by taking into account information such as in-house power generation capacity (3), fuel and power simulation allows for the calculation of the optimal operating conditions with the lowest possible purchase from external sources (4), and the results are fed back to guide the operator (5).
The system’s development was awarded the Academic Award (Technical Division) of the 2022 Japan Institute of Energy Award. JFE Steel established the JFE Digital Transformation Center (JDXC™) to promote CPS within the manufacturing process and other digital transformation initiatives to achieve innovative production improvements as well as stable operations. We remain committed to realizing a sustainable society by adopting digital transformation to address the various issues identified at production sites.
- *A system that brings together a vast amount of sensor information about physical space as big data in cyberspace and generates value by feeding back in real time the results analyzed by various measures for application in the physical space.
ST Resource Saving Silicon-Gradient Steel Sheet
- Environmental Benefit
- Save energy and reduce CO2 emissions
- Status
- Commercialized
CVD Continuous Siliconizing Process and Si Concentration Distribution Control
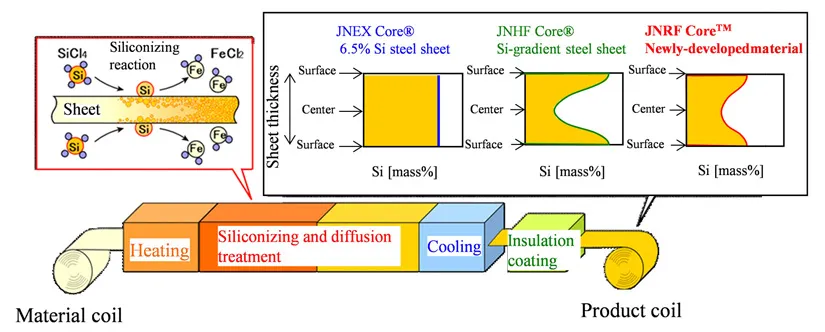
The recent trend toward increasing driving frequency due to the downsizing of electrical equipment has intensified the need to reduce iron loss*1 in the high-frequency range for electrical steel sheets*2, widely used as iron core material for electrical equipment such as motors and transformers. Meeting this demand depends upon increasing the concentration of silicon (Si), an element that strengthens electrical resistance. However, increasing concentration also causes magnetic flux density to decrease at the same time.
To overcome this, JFE Steel developed JNHF™, JNSF™, and JNRF™ using its proprietary chemical vapor deposition (CVD) continuous siliconizing process technology for controlling Si concentration distribution. These products exhibit low iron loss at high frequencies and high magnetic flux density, significantly contributing to greater efficiency while downsizing electrical equipment, and they are used as an iron core material for reactors for solar power generation and high-speed motors.
In recognition of the positive social impact of this development, we received the 2022 Award for Science and Technology from the Minister of Education, Culture, Sports, Science and Technology under the development category of the science and technology field. JFE Steel will continue to contribute to improving electrical equipment by raising efficiency, reducing size, and saving energy by providing high-performance, high-grade electrical steel sheets.
- *1The loss of energy, primarily as heat, that occurs when the iron core is excited by an alternating current. The less iron lost, the higher the efficiency of electrical equipment.
- *2Electrical steel sheets are obtained by adding silicon to iron and are widely used as iron core materials in equipment such as motors and transformers.
- Received the 2022 Award for Science and Technology from the Minister of Education, Culture, Sports, Science and Technology under the science and technology field (development category). (Japanese only)
- External Awards
ST Anti-Fatigue-Damage Steel for Increased Bridge Safety (AFD™ Steel)
- Environmental Benefit
- Recycle resources and reduce CO2 emissions
- Status
- Development stage
Examples of Thin AFD Steel Application
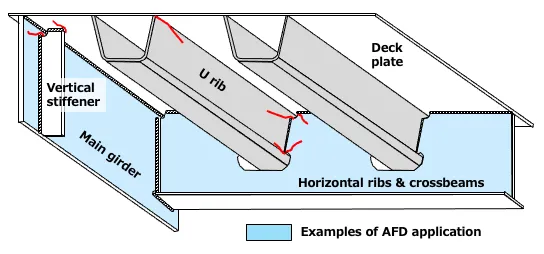
JFE Steel has developed a thin version of its anti-fatigue-damage steel (AFD™ steel) with improved fatigue resistance. The steel plate, produced by a plate mill at the East Japan Works (Keihin District) using the Super-RQ system with advanced cooling control, has a minimum thickness of 9 mm and retains the mechanical properties of conventional plates while offering improved fatigue resistance. Compared to AFD™ steel, the thin-walled version is expected to be deployed in a wider range of applications, including bridge structural members that are prone to cracking over time.
Ensuring low maintenance and renewal costs associated with aging is crucial for steel structures purposed for long- duration use. Thin-walled members of bridges are susceptible to fatigue cracking over time, and the cracks may increase in size between inspections and maintenance. The newly developed AFD™ steel increases the durability of steel structures because it can be used in places prone to fatigue cracking. Compared to ordinary steel, AFD™ steel reduces the fatigue-crack growth rate*1 to half or less of the upper limit of ordinary steel and roughly doubles product life, thereby reducing life cycle costs associated with long service life.
Looking ahead, JFE Steel will continue to improve the performance and quality of steel to achieve superior durability, safety, and economy in steel structures, including bridges, ships, construction machinery, and industrial machinery, thereby contributing to a more sustainable world.
- Note:AFD is the abbreviation for Anti-Fatigue Damage.
- *1Fatigue damage is caused by small, repeated forces that create cracks that gradually grow until the material fails. Since these cracks propagate incrementally with the repeated application of force, the length over which the cracks propagate per repetition is called the fatigue crack growth rate.
ST Extra-Thick, High-Strength Steel Plate for the Materialization of Large Container Ships
- Environmental Benefit
- Recycle resources and reduce CO2 emissions
- Status
- Commercialized
The world’s thickest crack arrest steel plate*1, developed by JFE Steel, is applicable to large container ships, with its 460 MPa class yield strength and a thickness of 100 mm. The technology is the first in the world to satisfy two different properties in the extra-thick steel plate: weldability and crack arrestability. Container ships are designed with wide open areas at the top of the deck. Since the hull is exposed to heavy wave force throughout the voyage, the top of the deck and the side of the hull (hatch side coaming) must be built with steel that is thick with high strength. In response to the recent trend of upsizing container ships for more efficient transportation, the thickness of steel plates has increased from 50 mm to 100 mm, with an expected yield strength of 460 MPa. At the same time, an excellent crack-arrest property is required to prevent the propagation of brittle crack. To ensure the safety of hulls that are rapidly becoming larger, the International Association of Classification Societies mandated that all 80 mm to 100 mm class thickness steel used in hatch side coaming must have at least 8,000 N/mm3/2 arrest toughness (Kca). Using TMCP technology*2, JFE Steel precisely controlled the heating and rolling temperatures and established a proprietary technology that increases the crystallization ratio in the central part of the steel plate’s thickness, helping ensure high brittle crack arrestability in the world’s thickest, 100 mm, high-strength steel plate.
The development of this technology received the 2023 Award for Science and Technology from the Minister of Education, Culture, Sports, Science and Technology under the development category of the science and technology field for significantly contributing to the materialization of ultra-large container ships. It has been awarded many other prizes including the 2018 Invention Prize of National Commendation for Invention and the 2019 Okochi Memorial Prize. We will continue to improve the economic efficiency, safety, and reliability of vessels by providing high-performance, high-quality steel material while meeting the diversified needs of customers and also addressing global environmental concerns, and contributing to the realization of a sustainable society.
- *1A steel plate with excellent performance in minimizing vessel damage by stopping brittle crack propagation in the event of weld cracking.
- *2A thermo-mechanical control process technology that improves the strength and toughness of steel material in an online process using controlled rolling and accelerated cooling systems.
ST Calcia Improvement Material
- Environmental Benefit
- Recycle resources and preserve biodiversity
- Status
- Commercialized
Calcia improvement material is a slag product that uses converter-type steelmaking slag as raw material and is manufactured by controlling the composition and adjusting particle size. Dredged soil mixed with calcia improvement material is called calcia improvement soil, which is stronger than the original weak dredged soil and is therefore able to prevent dredged soil from dissipating into the surrounding area and having a negative environmental impact placed in water.
This enables the effective use of weak dredged soil in land reclamation, shoal and tideland construction, and refilling former dredging sites. Calcia improvement soil has been used to construct a mid-section submerged breakwater* (Shin Honmoku Pier, Port of Yokohama), the main embankment material for creating a shallow area (incidental facilities at the sediment disposal site, Tokuyama-Kudamatsu Port) and backfilling material for an earthquake-resistant quay wall in the Mino offshore area, Fukuyama Port.
- *An embankment built under the water surface on the inside of a perimeter wall to divide the land into sections for reclamation.
Calcia Improvement Material and Calcia Improvement Soil
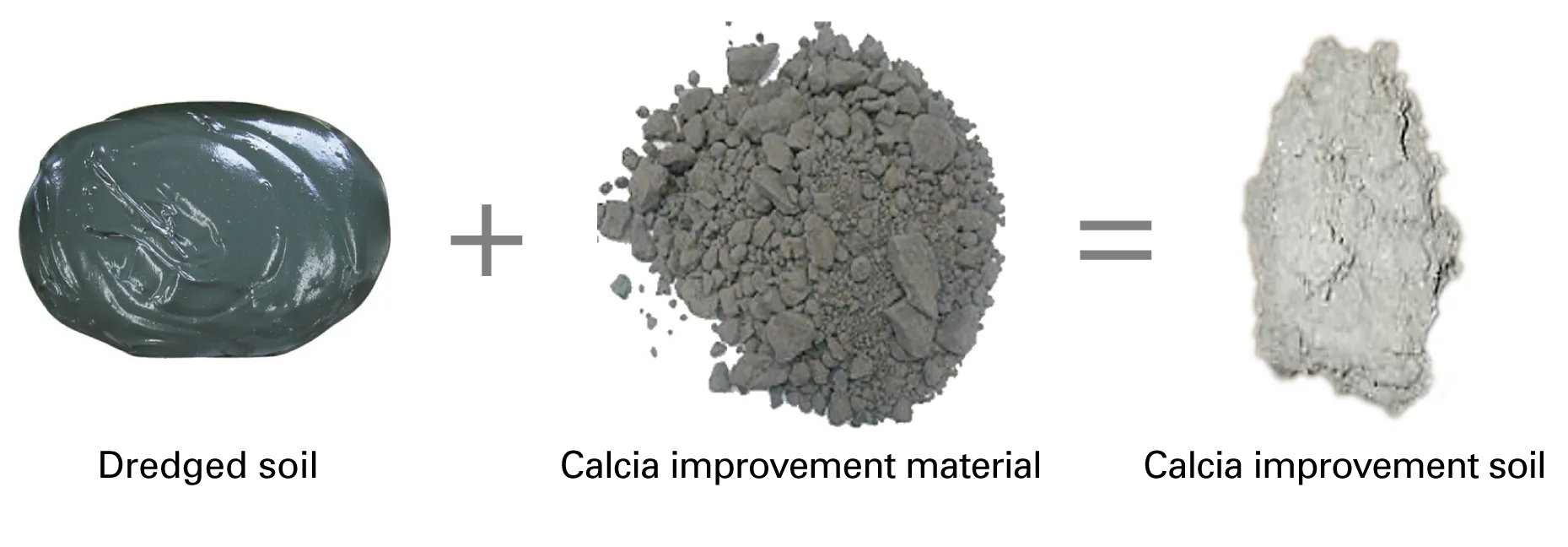
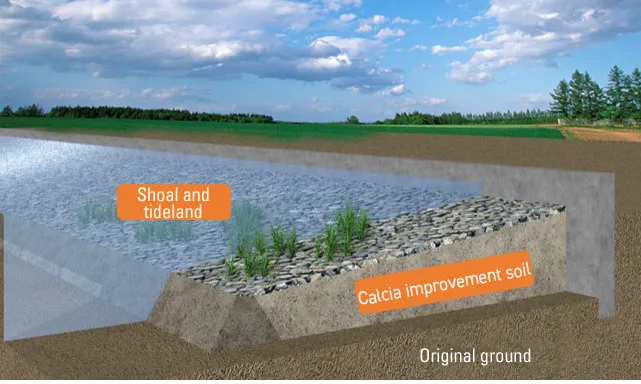
ST Precast Concrete Products Mixed with Finely Ground Blast Furnace Slag
- Environmental Benefit
- Recycle resources and reduce CO2 emissions
- Status
- Commercialized
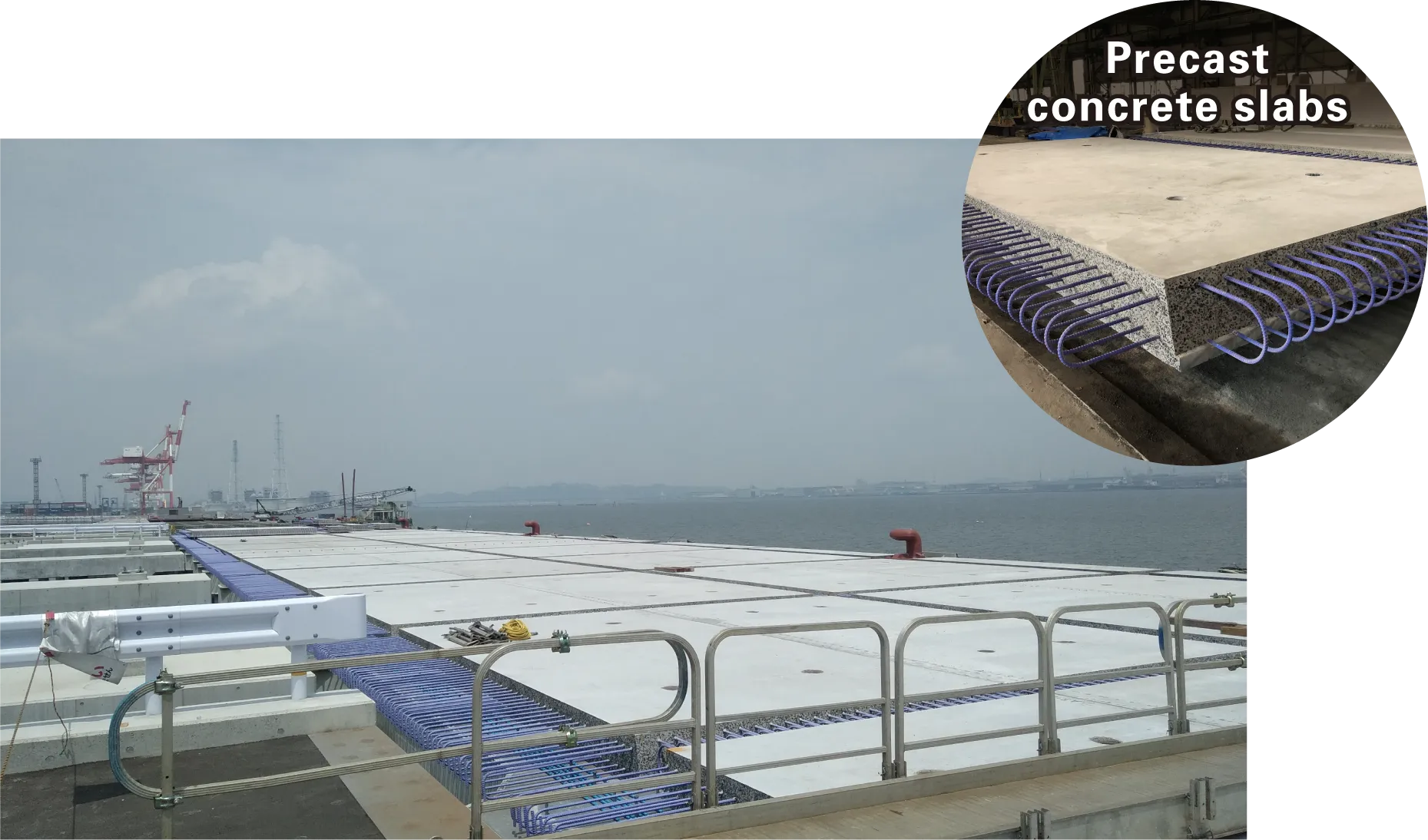
Finely ground blast furnace slag can be used as a cementing material in concrete. This type of concrete exhibits significantly higher durability under harsh conditions such as applications in sewers and exposure to anti-freeze agents. Its effectiveness in reducing environmental impact is widely understood, although there has recently been growing interest in its practical applications for concrete constructions that require higher durability.
As one of the deliverables for the Japanese government’s Strategic Innovation Promotion Program, the Japan Society of Civil Engineers published a draft guideline in March 2019 on the application of finely ground blast furnace slag to precast concrete product, and its application now includes precast concrete slabs installed in highways and piers. With the application of finely ground blast furnace slag in concrete, the durability of precast products is expected to be greater and more consistent, allowing them to contribute to building national resilience.
ST Use of Granulated Blast Furnace Slag to Reduce CO2 Emissions
- Environmental Benefit
- Recycle resources, preserve biodiversity, and reduce CO2 emissions
- Status
- Commercialized
Granulated blast furnace slag in crushed and powdered form can be mixed with cement and used as a substitute for cement for making concrete. This leads to reducing the production of cement, thus lowering CO2 emissions. For example, producing 1 tonne of blast furnace slag cement with 45% of its content substituted with granulated blast furnace slag emits 42% less CO2 than conventional cement. In FY2023, JFE Steel supplied approximately 5.94 million tonnes of granulated blast furnace slag to cement production, equivalent to a reduction of approximately 4.21 million tonnes of CO2 emissions.
CO2 Emissions for Producing 1 Tonne of Cement (Unit: kg-CO2/ton)
CO2 Emissions Source | Regular Cement | Blast Furnace Slag Cement |
---|---|---|
Limestone | 478 | 270 |
Electricity/energy | 278 | 168 |
Total | 756 | 437 |
- Source:Data published by the Japan Cement Association (compiled from the actual FY2022 data)
ST Restoring Marine Ecosystems Using Steel Slag Products
- Environmental Benefit
- Recycle resources, preserve biodiversity, and absorb and secure CO2
- Status
- Commercialized
Marine Stone™ is a grain-size-adjusted steel slag that controls the generation of hydrogen sulfide from the silty sediment in enclosed coastal seas and improves the environment in which organisms can live. Its effectiveness in improving marine environments is widely recognized, and the joint project with Hiroshima University has received external commendations.
Frontier Rock™ is another steel slag product that consists of artificial stones made from steel slag hydrated matrix and provides an excellent base for seaweed beds and fishing reefs. A submerged bank built on the seabed off the coast of Minami- Izu Town, Shizuoka Prefecture, has become a gathering place for large perennial seaweeds as well as useful fishery resources such as lobsters, turban shells, and a wide variety of fish. We are also testing the effects of Marine Block™ as beds for corals.
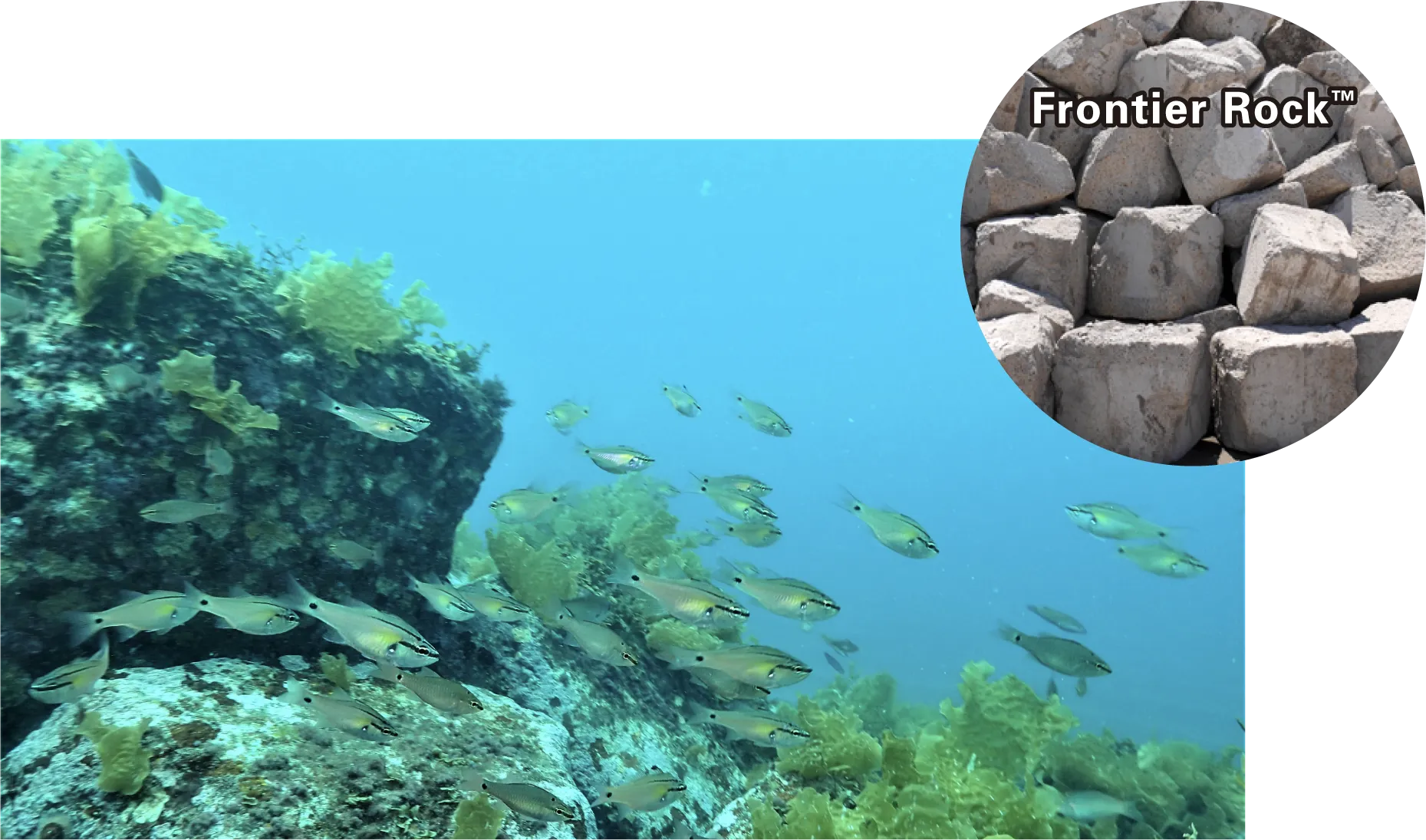
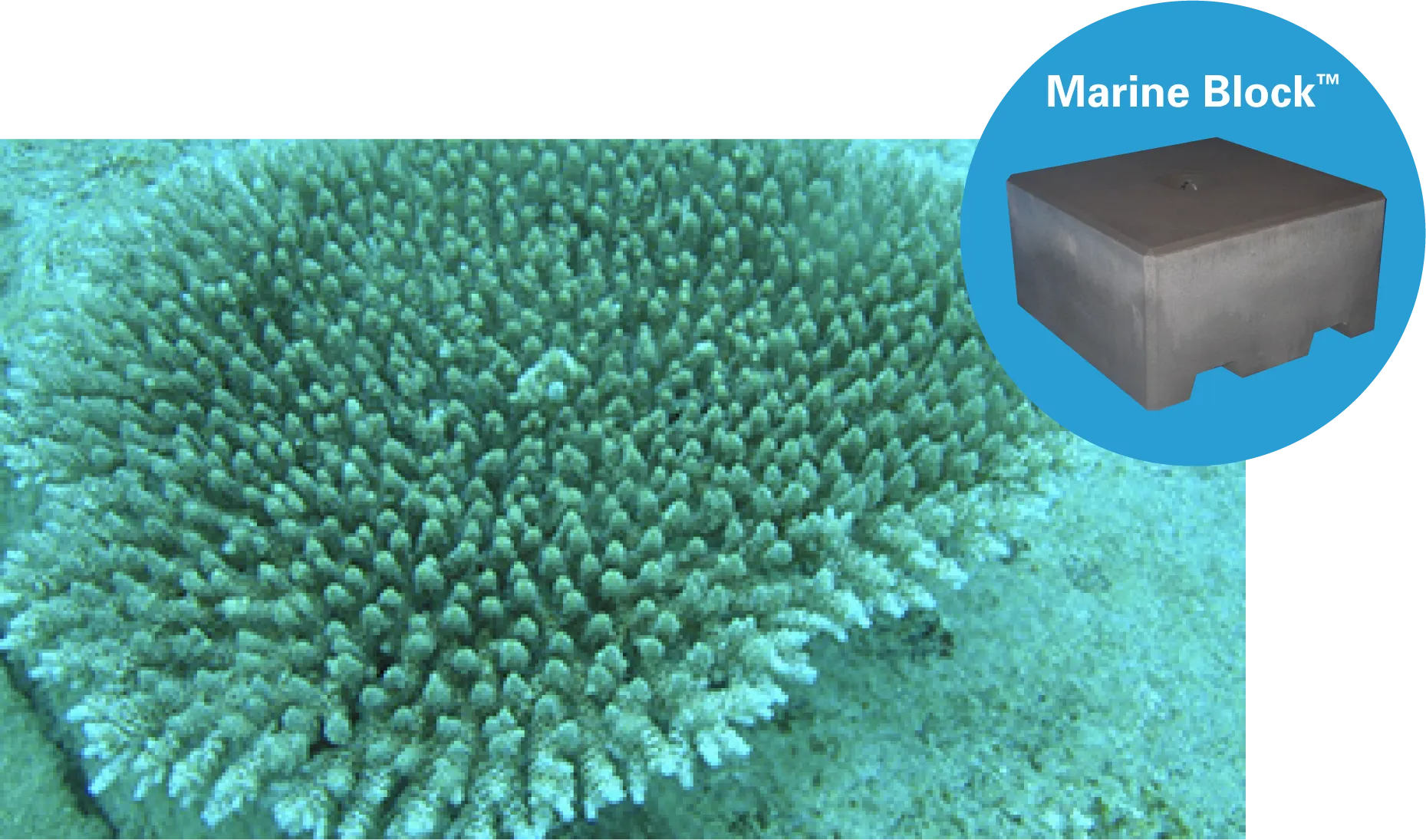
ST JFE Steel and Tohoku University’s Collaborative Research Laboratory for Green Steel
- Environmental Benefit:
- Reduce CO2 emissions
- Status
- Development stage
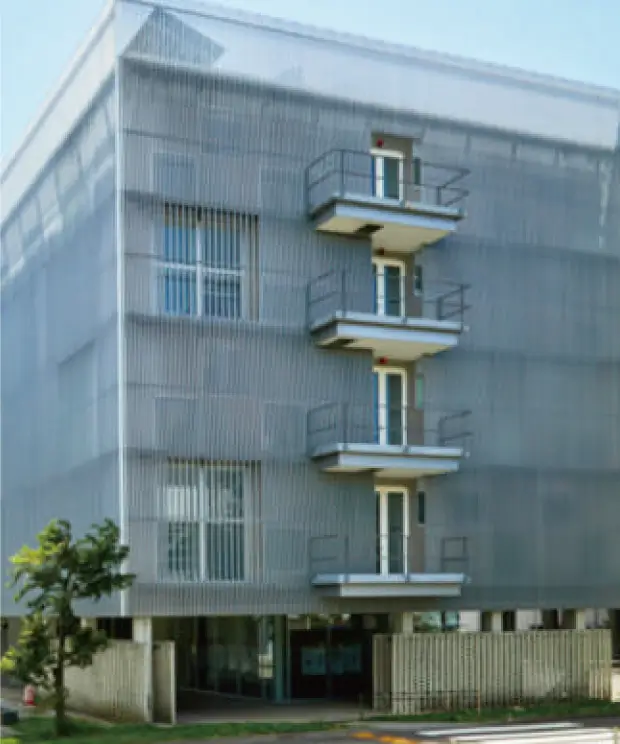
In February 2022, JFE Steel and Tohoku University jointly established the Collaborative Research Laboratory for Green Steel within the university’s Graduate School of Engineering to research eco-friendly steel materials and production methods for the carbon-neutral era. The Collaborative Research Laboratory is managed under a cross-divisional system and develops collaborations across a wide range of fields, including the development of steelmaking processes and materials. This will facilitate a multifaceted approach to resolving issues related to low-carbon steelmaking processes and to discover innovative development themes from new perspectives. Furthermore, we will dispatch young researchers to nurture highly specialized human resources who will lead the next generation of the steelmaking industry.
EN Carbon Neutrality Collaborative Research Center Established with the Tokyo Institute of Technology
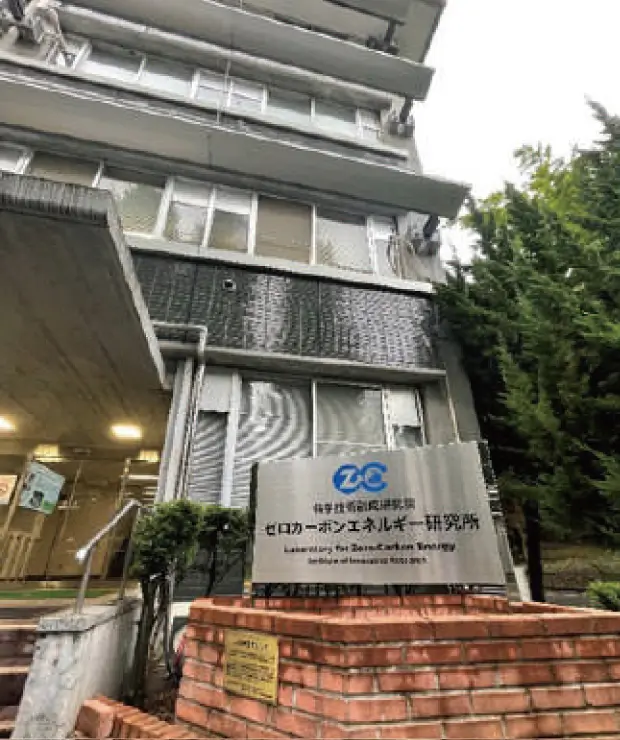
JFE Engineering and the Tokyo Institute of Technology opened the JFE Engineering Carbon Neutrality Collaborative Research Center (CRC) at the Institute’s Laboratory for Zero-Carbon Energy under the Institute of Innovative Research on July 1, 2022. The purpose of the CRC is to promote new technologies for realizing a carbon-neutral society. The two parties are comprehensively and jointly working on technical developments in carbon neutrality, transcending the boundaries of a typical individual joint research framework to pursue a multilayered approach and generate innovation across the wide range of fields required for realizing a carbon-neutral society.
The CRC will promote the development of new technologies to help realize a carbon-neutral society by combining JFE Engineering’s engineering technologies related to plant and infrastructure construction in the fields of energy and the environment with the Tokyo Institute of Technology’s advanced academic knowledge in a wide range of areas. The CRC will also continue collaborating with a variety of organizations through the Tokyo Tech GXI*, an industry-academia partnership project run by Tokyo Institute of Technology.
- *Intended to promote research activities that will initiate a GX (green transformation) society, strengthen startups, and substantiate industry-society collaboration.
SH Expanding Business in Biomass Fuels
- Environmental Benefit
- Renewable energy and reduce CO2 emissions
- Status
- Sales expansion
JFE Shoji imports fuels such as palm kernel shells (PKS) to Japan from Malaysia and Indonesia and wood pellets from Southeast Asian countries as fuel supplies for domestic biomass power plants.
PKS and wood pellets serve as carbon neutral fuel sources by absorbing CO2 as they grow. JFE Shoji is working to procure biomass fuel through a process that is environmentally and socially sound, thereby maintaining a sustainable business model. Additionally, the company launched alternative fuel initiatives for exiting the use of coal as it strives to become an environmentally sound company.
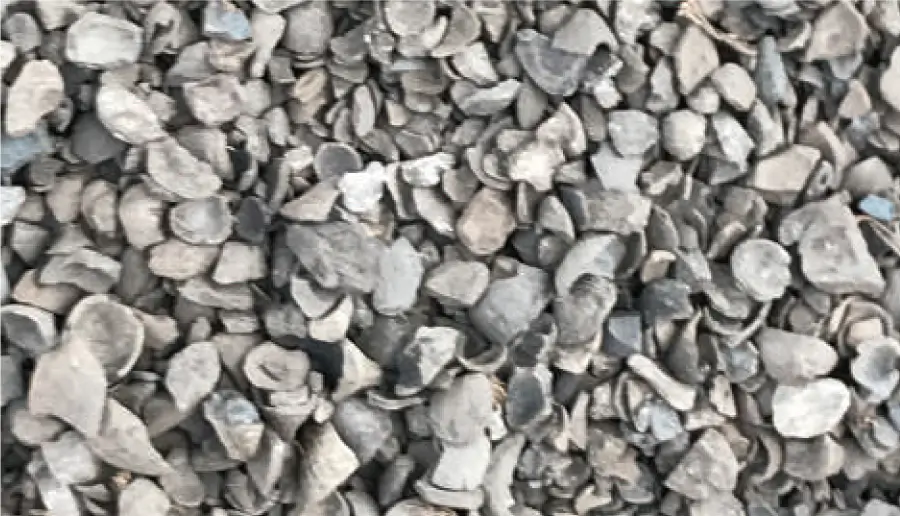
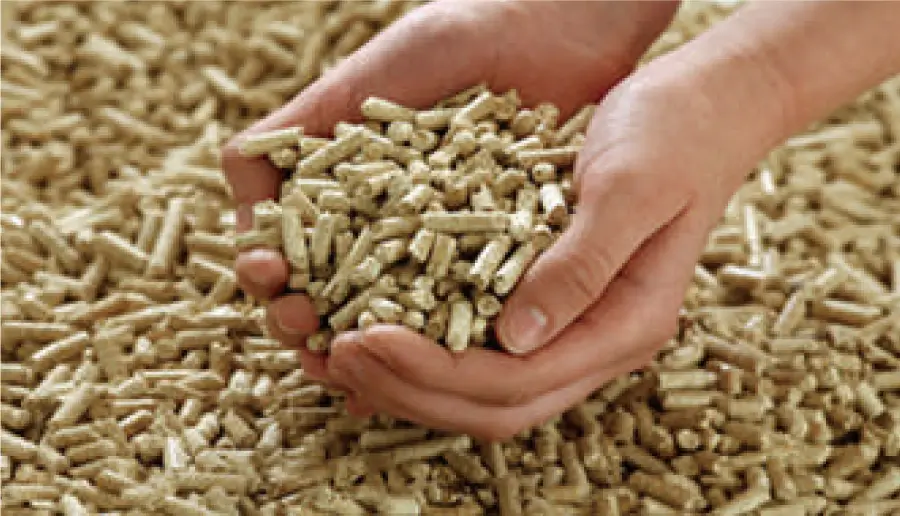
SH Expansion of Scrap Trading to Support the Development of a Recycling-Oriented Society
- Environmental Benefit
- Recycle resources and reduce CO2 emissions
- Status
- Sales expansion
JFE Shoji engages in a recycling business for steel and aluminum scrap. Demand for steel scrap is particularly expected to grow in Japan and overseas as the global community advances toward carbon neutrality. JFE Shoji will contribute to building a recycling-oriented society by increasing scrap recycling across the globe.